SOLIDWORKS Surface Tools for Industrial Applications
Need for Surface
Surface Modelling is a method used to create and represent complex shapes with high curvature controls. Generally, surfaces are used as an alternative where a particular feature is difficult to create using solid modeling. It is helpful especially in applications like centrifugal pumps, Organic shapes, Car body panels, Boat Hulls, etc., Continuity between the curves is very important for aesthetic reasons. NURBS ( Non-Uniform Rational B-Spline) curves are widely used by most of the CAD software. SOLIDWORKS surface uses a parameterized mesh of curves ( U-V curves). The face curve option available to capture a curve from the surface.
Solid Vs Surface
Most of the Engineers preferred solid modeling due to the easier definition of boundary condition. But the applications like Turbine blades, Aerofoil profiles require surface modeling.
In solid modeling, we can create thick solids with regular shapes. For example, we can create a cube with a square sketch alone. It produces six faces with a single solid body. In surface, we can create an individual face, each faces act as a surface body and after creating all the bodies we can knit them to make a perfect solid body. Surface bodies have no thickness (negligible). In the Design as well as the costing sense, the mass properties of a model play a major role. For that purpose after creating surface bodies, we want to convert them into solids. Some tools available in SOLIDWORKS for the conversion of the surface to solids are Thicken Surface, Knit Surface.
Offset Surface
It is also known as the copy surface. Offset is used when we want to create an exact replica of any face.
Surface from Mesh
When a .stl is imported into SOLIDWORKS, It is imported as a tessellated or mesh data. Before SOLIDWORKS 2018 we were not able to make a surface from a graphic body. In 2018, SOLIDWORKS introduced the Surface from Mesh tool to make a surface from *.stl, *.obj, *.off, *.ply, *.ply2 or *.3MF files. This tool has been used for for reverse engineering.
Flatten Surface
The imported files such as Sheet Metal with non-standard bends can be converted to the surface using an offset surface and then we can find the flatten length using surface flatten tool. The deformation plot is available to view the stretching concentrations that occur while flattening.
Thicken & Thicken Cut
Used to convert a surface to solid, we can give the amount of thickness and direction. Similarly, Thicken cut option is also available to cut a solid body with a surface body.
For example, to cut an irregular shape in cylindrical bodies.
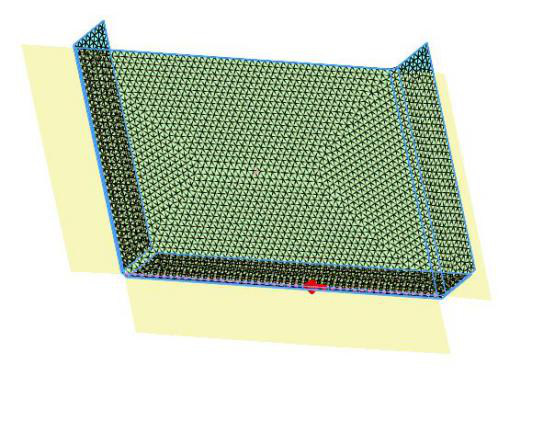
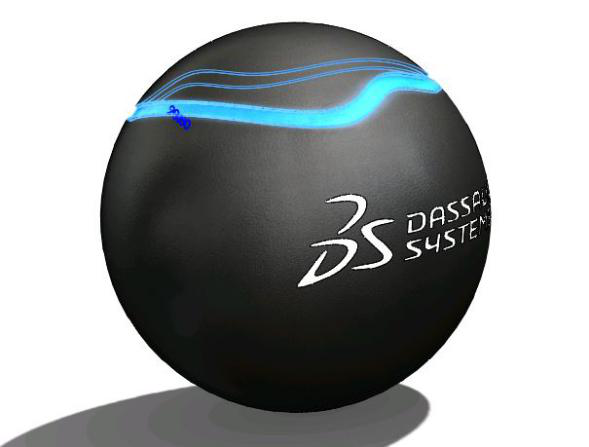