The Speed Shop-Concept Handlebars for a Classic Track Bike
As someone who has a need for speed in the two-wheeled self-propelled category, I enjoy playing around with bike concepts. The off-season generally provides time and open space for this, and this last one was no different. The target bike? My late 80’s Colnago Master Pista. For those not familiar, the bike equivalent of the Ferrari F40, Italian heritage and all. Except on a bit more of a budget. The purpose? Track racing.
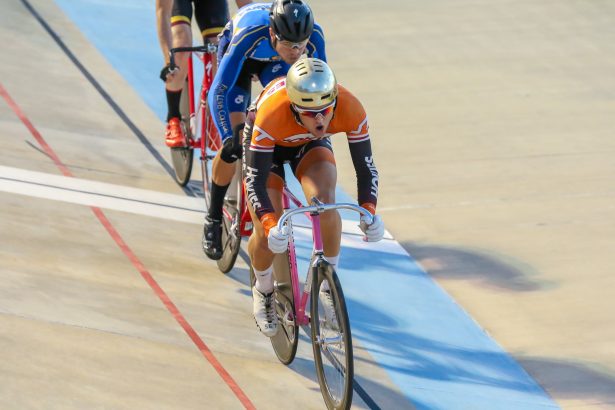
The target component? Handlebars. Why? Well, with one gear and no brakes, there aren’t a lot of components to play around with in the first place. This is also 1 of the 3 contact points, all of which can make a tremendous difference in fit.
Concept
There were a few things I wanted to do with the handlebars-make them really narrow, integrate them with the stem, and get wild with them. Narrow handlebars are generally more aerodynamic. Or really, they put the rider in a more aerodynamic position. And they’re rather hard to find. I generally like the look of integrated stem/handlebars, so I made that a target. Finally, with free range, I decided to get crazy with them and came up with the concept below.
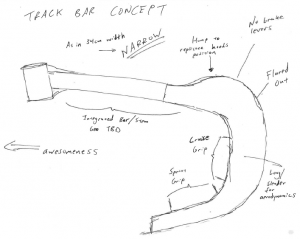
Topology
Topology is such a cool tool in that we can start with a basic shape, run simulation studies much earlier in the design process, and use the resulting shapes as a more advanced starting point for modeling. For the studies, I started with a pretty basic shape, modeling all the volume material could take up.
With symmetry, and just one load modeled as a max effort pull on the bars in a sprint, the set-up was rather simple. I ran the topology study for two set-ups, a solid model and a shelled out model.

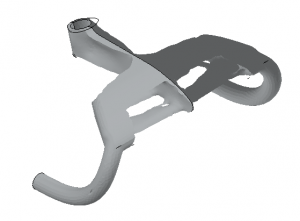
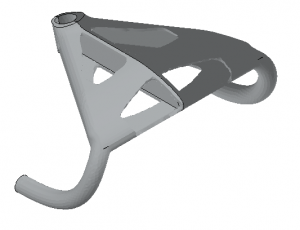
Interestingly enough, the solid results didn’t turn out too differently from a standard bar/stem combo. The shelled results, however, produced some rather wild geometry. I really liked the concept of the outside angled pieces, creating more of a v-shape instead of the traditional stem. So I took the idea and ran (rode?) with it.
Modeling
For the actual modeling, I decided to use a top-down assembly approach. There was no way this was getting 3D printed in one go, so multiple parts inside of an assembly made sense here. I first made a 3D sketch for the basic layout using these tips on 3D sketching.
Wanting to avoid getting yelled at for using all of our 3D printing material, I decided to incorporate off the shelf carbon fiber tubing. That way, I could focus on modeling just the handles and connection piece to the steerer tube.
The handle was modeled with a spline in 3D using these tricks and a surface loft, incorporating much of the concept ideas from earlier.
To connect to the steerer tube of the fork, I needed a lug. I used a combination of surface lofts and filled surfaces to blend the tube connections together.
From there, all that was left was to mirror the right handle to create a left handle, and model in the carbon fiber tubes. I did bring the front cross bar significantly lower than in the initial topology study. Why, you ask? Partly to be able to wrap my thumbs around it and pull myself even lower. Mainly just because I could.
To make it come to life, I printed out the three parts I modeled and ordered some carbon fiber tubing. After taking a hacksaw, hammer and epoxy to the components, it all came together.
The bars put together. Photo credit: Jack Connolly, Jack Robert Photography
And on the bike
The bars on the bike. Photo credit: Jack Connolly, Jack Robert Photography
Unfortunately, I don’t have a vacuum bagging set-up yet, so no additional carbon fiber was laid up to make it usable. Will I get around to it? Maybe. But for now, it’s time to quit messing around with off season projects and get to training again. Because no matter how cool your bars look, it’s still the engine that counts.
Link 1: https://blog.tpm.com/three-minute-thursday-3d-sketching-basics
Link 2: https://blog.tpm.com/three-minute-thursday-3d-curves
By: Luke Woodard • Application Engineer • TPM