The Cubie Awards: A SOLIDWORKS Story
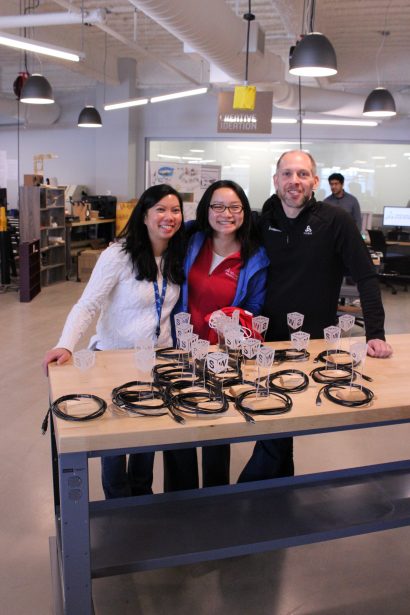
If you ever have the chance to visit the DASSAULT SYSTEMES campus in Waltham, MA, you’ll initially be greeted with what looks like an ordinary office. Inside the Water Building, pods of cubicles dot the wide, open floor plan. Across from the incredible view of the Cambridge Reservoir, there are offices with floor to ceiling windows, where directors and executives have their desks and open doors. White walls, grey ceilings, bustling employees; you can be forgiven for thinking this is your average, modern office building. But then, among the pods, on the desks in the offices, you see some things that stands out, eye-catching and red. Sprinkled around the office, you start to see the Cubies.
The last thing you expect, walking into a software company, is a stunning yet unassuming art piece like the Cubie, shining crimson from atop desks and cubicle walls, but there it is. There are many of them. They’re all over. This year’s Cubie awards were designed and manufactured in-house by Product Definition Senior Manager Annie Cheung, User Experience Design Senior Manager Chinloo Lama, and Product Definition Director Sal Lama.
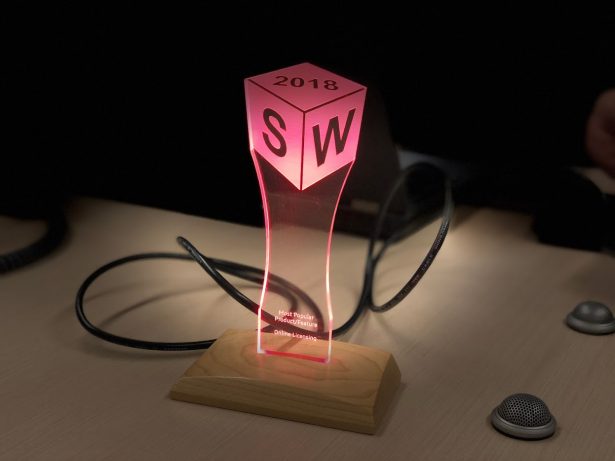
From their labor birthed the sleek, deceptively simple 2018 Cubie: a tall piece of acrylic with a floating SOLIDWORKS cube logo etched on top, tapering down to a squared, then beveled bottom where the award recipient’s name is lasered in. This piece is held steady and secure inside a maple base, with a USB cord to power the red LEDs shining up the acrylic. On the bottom of the base, holding in the wires, is a plywood plate reminding all SOLIDWORKS employees to “Keep on lighting the way!” The awards are gorgeous. The first time I saw a Cubie, I didn’t even know it was an award—I thought it was just a decoration, a modern day, nerdy SOLIDWORKS version of a sculpture. Which, on one level, they are. But on many others, they’re not. And like any art or engineering piece, there was a lot of trial and error involved in the production.
I had the chance to sit down with Annie, Chinloo, and Sal, and learn about the process and challenges that went into the new Cubie design. “If we break down the responsibilities, Chinloo primarily did the acrylic, I did the base design, and Annie [did] all of the electronics,” said Sal. “In the end, we all sanded and soldered…It was fun and exhausting hours of labor love.” He held up one of the many Cubie prototypes for me to see and said, “It takes a lot to produce 100 of these darlings.”
Release the Cubes
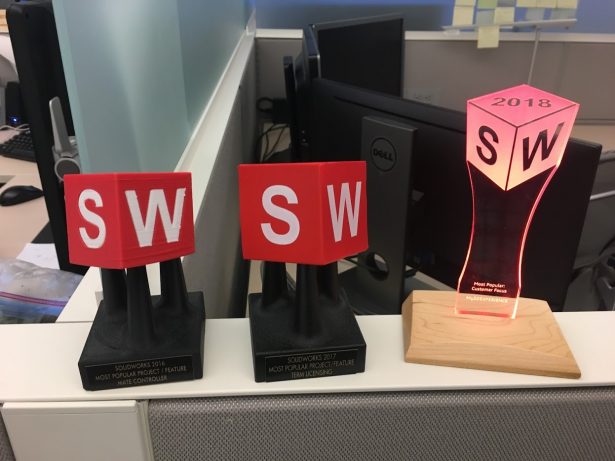
What even is a Cubie? Why produce 100 of them? What did the old design look like? And why was this new design even necessary?
Three years ago, the SOLIDWORKS R&D department decided to stage a celebration for the new software release, and part of that celebration would involve honoring members of the SOLIDWORKS team who’d worked on projects. It’s like the SOLIDWORKS Oscars: members from departments world-wide are nominated in various categories, their peers vote, and the winners are announced at the SOLIDWORKS release party. As a token of appreciation, winners receive a Cubie award they can proudly display on their desks.
The first year, Cubies were a 3D printed cube object sitting on a 3D printed stand. Next year, the Cubies transformed into a foam cube, squishable, fun and throw-able, on the same stand. All perfectly fine designs and objects, but SOLIDWORKS CEO Gian Paolo Bassi made it clear to the R&D team that he thought they could do better. So when it was time to think about the Cubies for 2018, User Experience Architecture Vice President Jim Wilkinson and SOLIDWORKS Applications Senior Director John Sweeney decided to surprise everyone and completely redesign the awards. Jim sent out an e-mail to members of his team who he knew would be up for the challenge, would be willing to create a new design and think beyond 3D printing. And thus, the Cubie Team was born. Annie, Chinloo, Sal, Jim, and Product Definition Senior Manager Rob Jost worked together with the simple mission of redesigning the Cubie base. But because they are all engineers, specifically SOLIDWORKS engineers, the project exploded into something much more ambitious.
Cutting Out the Cube
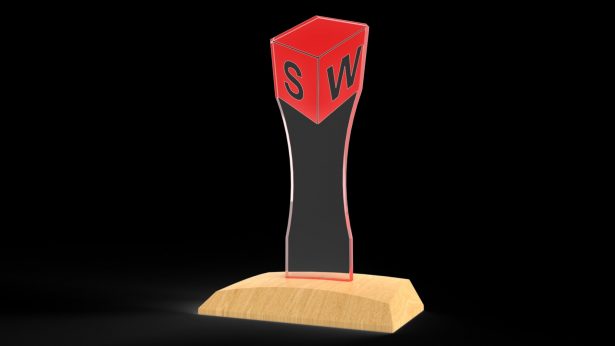
In the beginning, the squishy cubes from 2017 were ordered and ready to go. The original task was to make them look different, to redesign the stand with the initial foam product. An inspiring image of a winged creature holding a cube, drawn with curved, fluid lines, sent in by Rob, led to Annie’s idea of scrapping the foam cube and 3D printed base and creating something entirely out of acrylic and wood. Then they could add LEDs to brighten the lines of the acrylic and make the final product even more exciting. After seeing a similar, finished product in the 3DEXPERIENCE Lab, the Cubie Team knew it could be done. With the final design agreed on, Jim and Rob stepped back, and the modeling, material sourcing, and fabrication of the Cubies was entirely in the hands of Annie, Chinloo, and Sal.
“When we started out, we were already talking about trying to reproduce what looks like a three dimensional block,” explained Chinloo. “The traditional logo we use for SOLIDWORKS is a red cube that’s tilted, specifically the [isometric] view, so we wanted to see if we could capture it in a two dimensional laser engraving and then still look 3D…We knew we wanted to lift it up and make it all look like it was floating.” Chinloo and Annie worked together to shape the new acrylic design and model it with the LED lighting. Simultaneously, Sal was working on the base design, “pestering” (his word) Annie for specific part sizes so he could measure out the channel needed to hold the USB power cord and LEDs.
After being modeled and rendered in SOLIDWORKS, the Cubies were manufactured in the 3DEXPERIENCE Lab, utilizing the machines available for all DASSAULT SYSTEMES employees. These machines, however, are meant for consumer use, not mass production, and one of the challenges the team faced was working with the machines to make over 100 acrylic figures and wood bases.
Acrylic Artistry
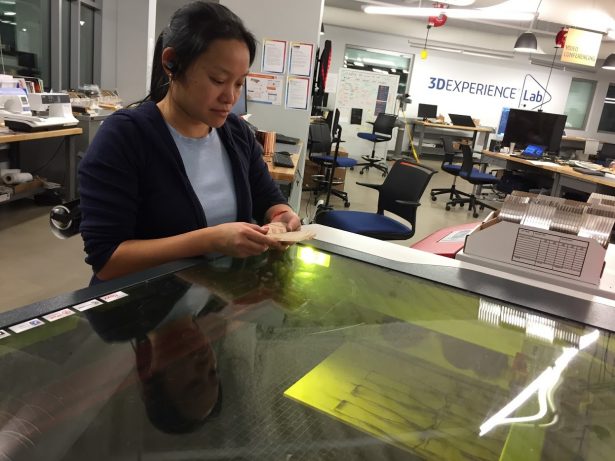
“I learned so much [from working with the machines],” explained Chinloo. “If we ever make anything like this again, it’s going to be in small batches, not 100 at a time.” She had to work around the limitations set by the Epilog laser cutter used to cut the acrylic. And there were many limitations.
One of the biggest issues that came with mass production was the high heat of the laser. Chinloo couldn’t cut as many pieces at one time as she wanted: if she produced too large of a batch, the pieces of acrylic that were cut earlier in the process would begin to cool while the laser was still cutting elsewhere. If pieces cooled while still inside the laser cutter, they would melt back together. Chinloo had to figure out a way to get the pieces out before the cuts cooled.
The machine’s focus distance was also “very touchy,” leading to incomplete cuts and the need for machine recalibration. The traditional laser cutting method of engraving and then cutting wasn’t working with the large amount of pieces. In such a big batch, an acrylic piece that was etched and then cut in the laser cutter would get burnt and smoky. Sal handed me an early acrylic piece cut the traditional way. What I thought were finger smudges around the head were actually smoke stains left from the laser burning the material while it cut.
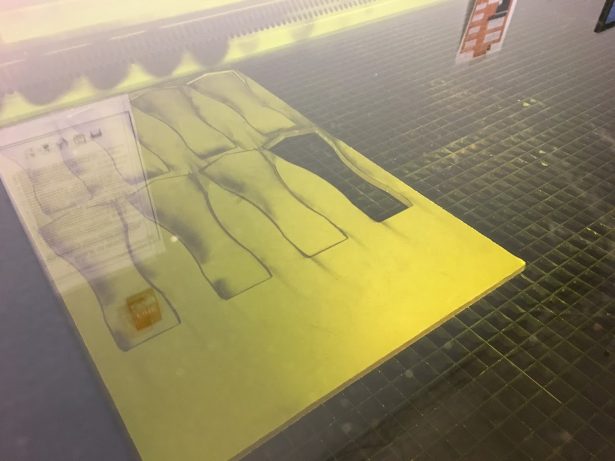
A laser cutter setting that worked one day wouldn’t produce the same output the next day. “[Chinloo] would record the numbers, thinking those were the [reproducible] numbers, and then she would go back again with the same numbers and sometimes it wouldn’t produce the same result,” Annie remembered. Chinloo had to do many, many iterations of the shading on the cube to get the correct engraved depth. According to her, “It was much more of an art than a science.”
In the end, the laser cutting method had to be minimized and reversed: cut the shape of the design out before engraving. After cutting out just eight pieces, Chinloo kept the negative and was able to utilize it as a stencil and use that to align the pieces in the laser cutter and then add the engraving. “That turned out really well,” she said.
Base Jump
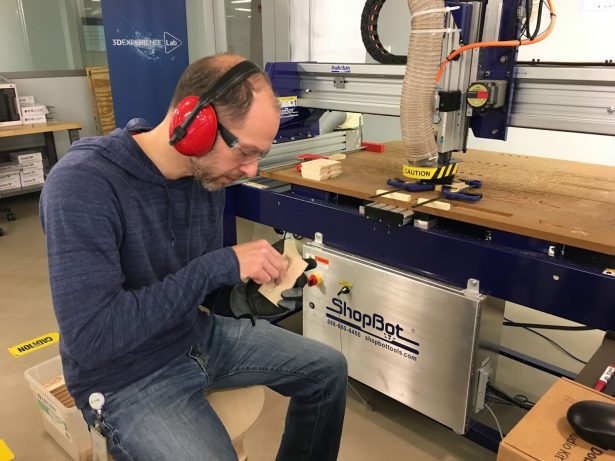
While there are saws available in the 3DEXPERIENCE Lab, Sal hauled the two huge maple boards used for the Cubie bases home and ran the wood through his own table saw to build blanks. He used his own tools to work on the wooden pieces, then took the blanks into the 3DEXPERIENCE Lab for further processing. “It was done in two steps,” said Sal. “The bottom was machined first, all the pockets, and then it flipped over and the contour was machined on the top.” The mistake he made was cutting all the inclines first while at home. Trying to hold the pieces in place while using the CNC machine in the 3DEXPERIENCE Lab turned out to be an interesting challenge.
Sal and Chinloo ended up cobbling together a jig to keep the bases in place while the CNC machine precisely cut out the channels to hold the USB wires. Then, later issues with the USB wires caused Sal to have to redesign and implement the bases again. And then again.
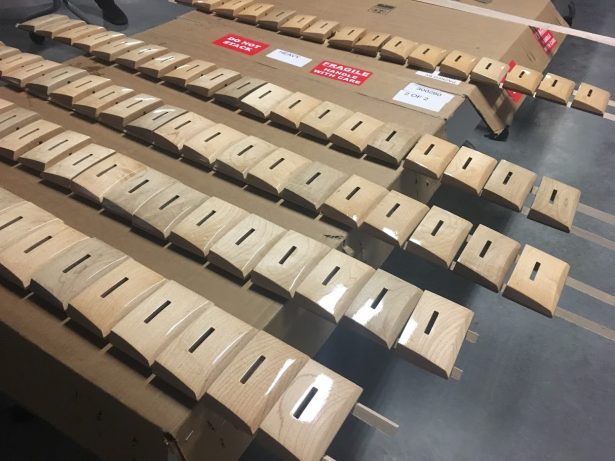
“If I were to do this again, I would pay more attention to the manufacturing processes,” Sal said while twirling a base prototype between his fingers. “So that’s kind of a cool lesson learned. We were just hustling, so focused on the design, and then we were like, ‘We’ll figure out the manufacturing.’ And we did! But still, it wasn’t perfect.
To add more fun to the imperfect process, the bases all had to be hand sanded. Sal brought in his palm sander and belt sander to hasten the operation, but, after testing, the Cubie Team realized they were losing all the edges Sal had worked so hard to cut. So hand sanding it was, the bulk of which was done by Annie. Then came the last step, the finish. Two coats of satin stain looked great on the maple while it was wet, but when dried it looks almost matte—no shine, all dull. So another coat of semi-gloss was added, leaving a smooth, shiny finish. “We’re all very happy with that,” beamed Sal.
Wires, Wires, Everywhere
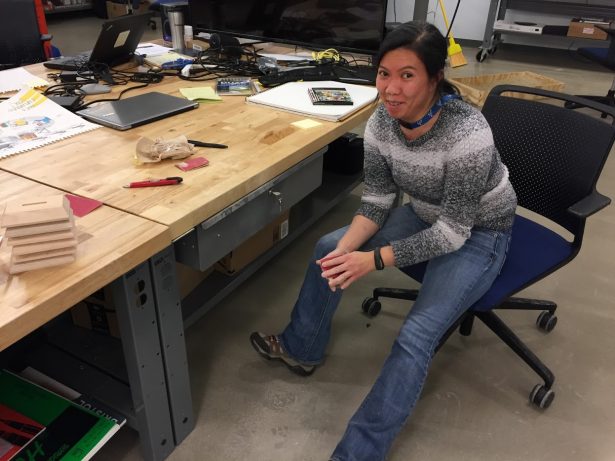
No one wants their power source to corrode, so the Cubie Team decided against their original idea of using batteries to light up the LEDs and instead switched to a USB cord. “We steered away from an AC adapter because we have international employees in India, so we thought let’s stick with the USB to keep it as universal as possible,” Annie said. But then the USB cords they wanted to use, beautiful white cords complete with on-off switches and ready-to-solder exposed wires, took a month to come in. So they had to order a different wire, a thicker wire that Annie needed to strip by hand, leading to the base being redesigned and cut so the new wire would fit.
“The biggest challenge was finding all the materials that would meet the requirements,” she explained. Not only did the original USB cord need to be replaced, the original LEDs were too separated, and most of the LEDs she found to replace it were multicolored and had controllers at the end to change the colors. “Sal didn’t want a nub sticking out of his beautiful base,” Annie laughed. This led to finding a solution by bending the LEDs into submission, which led to another change in the base design. It was starting to get hard to screw the plate into place with the USB wire and the LEDs, so Sal had to go back and open the channel even more.
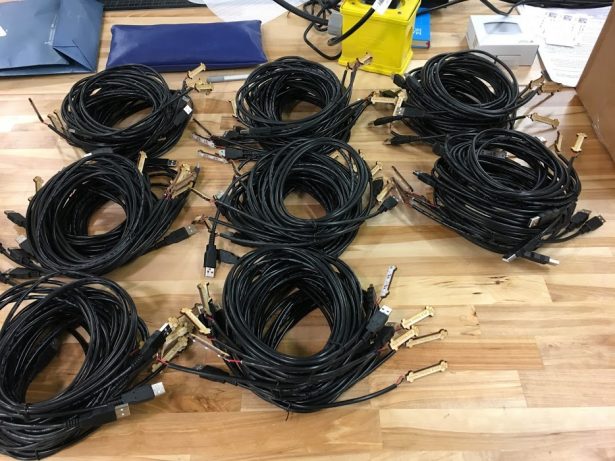
Annie ended up hand stripping 160 wires and soldering all 160 into place. She hand sanded the majority of the bases. Every time she brought a finished base over to Sal, he would laugh: the amount of sawdust covering her, from toe to tip, made her look like she worked in a bakery and plunged herself into a bag of flour. “Her face, her shirt, her hair, it was all over,” recalled Chinloo. But eventually, the sawdust was wiped away and all components of the manufacturing process were completed. It was finally time to put the awards together.
Which led to another problem: putting the awards together.
Reaching That Finish Line
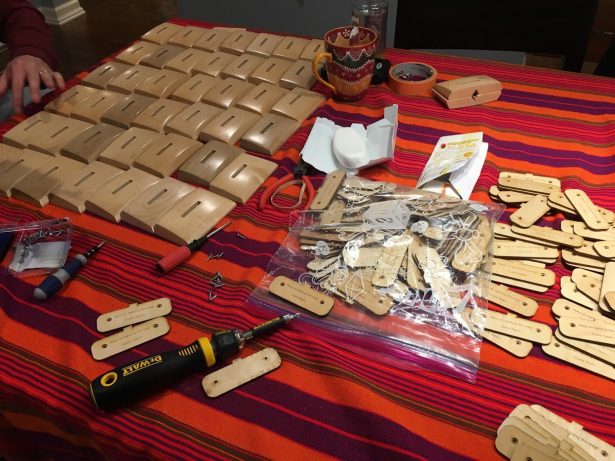
One cold winter Saturday, Annie drove over to Chinloo and Sal’s house (Chinloo and Sal are married) to finish up the Cubies. It was there, sitting at the dining room table with Gatorade and tea at the ready, the Cubie Team realized the bevels they’d designed into the acrylic were not performing. The original design was to use bevels cut into the acrylic and rely on press fit and friction to hold it all in place. That, they discovered with despair, wasn’t working. “So we did the hot glue thing,” Sal said matter-of-factly.
The team cared about the way the Cubies would be held—if someone grabbed one by the acrylic to pick it up, they didn’t want that part sliding out of the base. Thus, the hot glue inside the base contour. There is still friction in place to hold the Cubies together, but the extra hold from the adhesive makes it that much more stable. Sal and Annie spent another afternoon hot gluing the acrylic to the bases, and finally, the Cubies were complete.
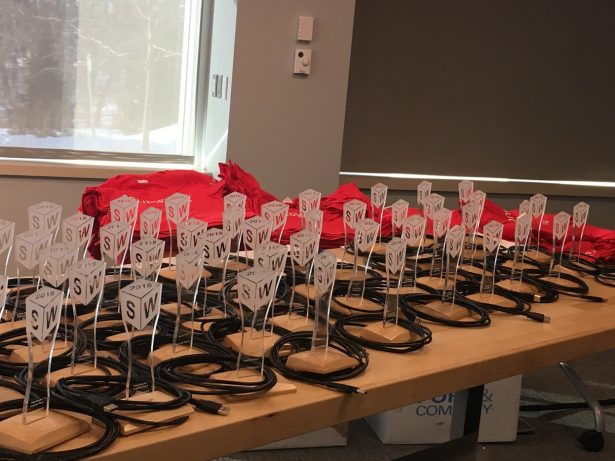
During the award ceremony at the SOLIDWORKS release party, the audience was stunned. They were all still expecting the squishy foam cubes from the previous year, and the crowd broke into applause when the new Cubies were rolled out. “I think [they’re proud that] they received something as special as this,” said Annie, “and [it makes me proud] for us to be the ones to have given that to them.”
Cubie Culture
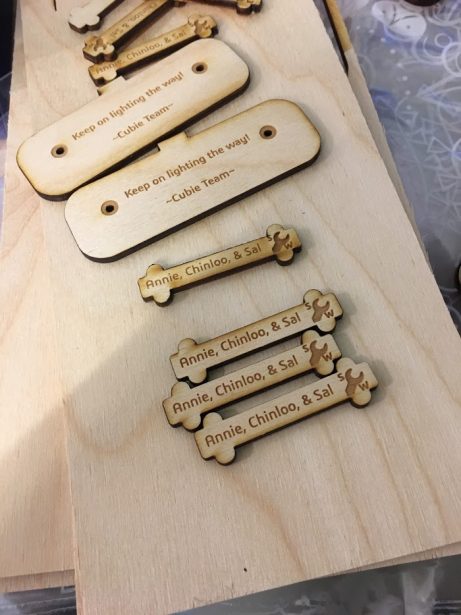
On the bottom of each Cubie base, there is a plate screwed in that covers the worked and reworked channel. Into that plate, the 3DEXPERIENCE Lab laser cutter engraved the following:
Keep on lighting the way!
–Cubie Team–
If you take a screwdriver to the plate, a plate that was screwed in by hand by either Annie, Sal, or Chinloo, and remove it, you’ll find the rest of the USB cord leading into the channel Sal machined inside the base. You’ll also find the strip of LEDs Annie cut attached to the back of a small, dog bone shaped piece of plywood. The plywood holds the LEDs in place and keeps the soldered USB wires attached. Engraved into the back of the plywood are the words “Annie, Chinloo, & Sal,” along with a small picture of a wrench with an “S” on one side and a “W” on the other.
The wrench with the letters? That’s the original SOLIDWORKS logo, over twenty years old now. If you didn’t know the “dog bone,” as the Cubie Team calls it, was there, you’d never think to look for it. You’d never think someone would include a little Easter egg like that. Unless, of course, you work at SOLIDWORKS.
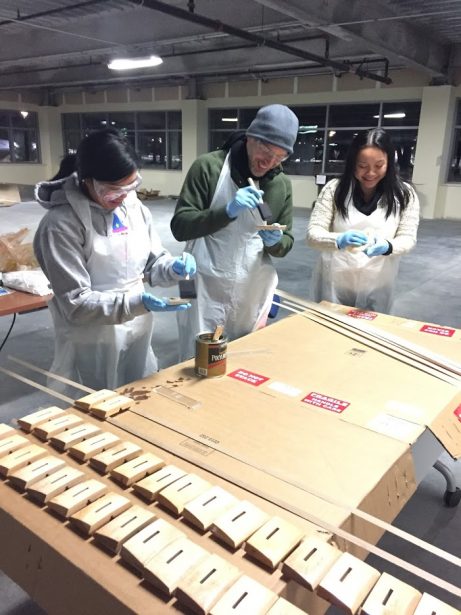
Talking with Annie and Chinloo and Sal, listening to them interact with each other, joke around, laugh with one another, I started to put the pieces together. It’s easy to look at something as pretty and technically impressive as the newest iteration of the Cubie award and think, “That looks nice,” and move on with your life. Just like it’s easy to walk around the DASSAULT SYSTEMES campus and think, “Huh, neat office,” take in the view of the reservoir, and be on your way. But when you look closer, you start to get it. “There’s a culture that’s been at SOLIDWORKS forever,” Sal said, “and it’s a culture that’s alive because of how people behave.”
He’s right; from my desk at a contractor table, I see that culture in action. I see people crossing paths, asking for help and receiving it, complimenting each other, actually caring about what they do and the people they do it with. In the employee lounge while grabbing a cup of coffee, I hear people talking about the improvements they want to make to their projects, or joking about a post a coworker made to Facebook, laughing together and meaning it. When I’ve gotten lost in the mammoth Waltham campus, people have gone out of their way to help me turn myself around. It doesn’t feel like the “I drank the Kool-aid” situation you get with a lot of tech companies, nor does it feel like the type of office where everyone is scrambling to finish their day and just leave already, overworked and miserable. It feels like a large group of people who honest-to-God care about what they do, what they produce, and the people they’re doing all of it with.
“I think we wanted to do this, [to make the Cubies,] to show it’s not just ‘It’s my job, pat on the back,’” Chinloo said. “We wanted to say that it’s more than that. It’s worth our time afterwards to get something cool, so you remember our effort as long as this thing is around.” It was the culture at SOLIDWORKS that led Annie, Chinloo, and Sal to power through and complete this project on top of their other work. There were no skipped meetings, no postponement of other duties so they could spend time in the 3DEXPERIENCE Lab. The Cubie Team did all of their own work and then stayed at the office, sometimes from 8 AM to 9 PM, sometimes slogging over to Waltham over the weekend, to finish the awards to their standards. “I think the motivation, certainly for me, and I think it’s true for the other two ladies…is that we did this so we could help tell people that [the SOLIDWORKS culture] is alive and strong,” said Sal.
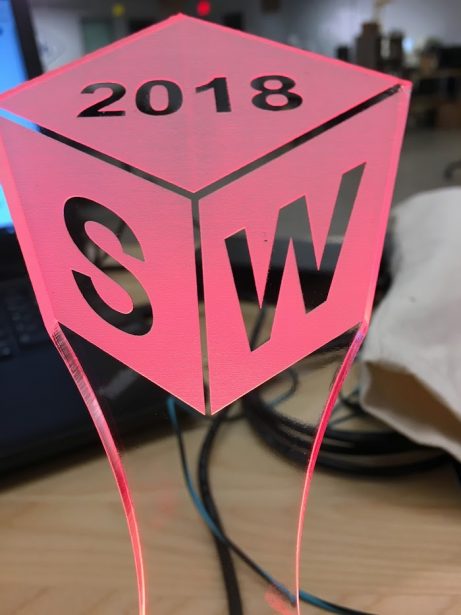
In the morning as I walk to my desk, I pass a lit Cubie sitting on top of a text book, casting its soft red glow onto the four cubicles below it. I don’t know who it belongs to, who the winner is. But I know whoever received it was proud enough to display it like that, shining over all the desks for anyone and everyone to see it as they walk by. I know that person knows that three of their fellow employees, three other members of the SOLIDWORKS community, put their time, sweat, and frustration into making that award for them.
We use the word “community” a lot at SOLIDWORKS, especially in the Education Department where I work. But there’s a difference between saying it and living it. I believe, especially after learning about the Cubie process from Annie, Chinloo, and Sal, that the people at SOLIDWORKS really live it. For each other, for their customers, and for themselves. And that passion for what they do, for the people they spend 40 hours a week with, and the company they work for will keep lighting the way for years to come. The new and improved Cubie design is proof of that.
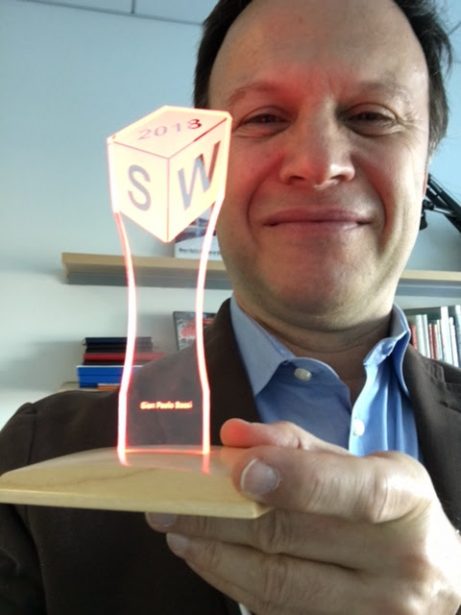
Thank you to Annie Cheung, Chinloo Lama, and Sal Lama for their time and expertise. Also, thank you to Abhishek Bali for bringing the Cubie story to my attention. And for Sal: San Dimas High School Football Rules!