What’s New in SOLIDWORKS Simulation 2022
Just like SOLIDWORKS® 2022, SOLIDWORKS Simulation 2022 will enable you to work smarter and faster than ever before. Let’s look at my four favorite enhancements in SOLIDWORKS Simulation that you will want to know about.
1. New Linkage Rod Connector
Simulation 2022 delivers a brand new Linkage Rod Connector.
Before I explain what this new connector can do, you need to know that using connectors is a fantastic way to simplify analysis and save you time, without sacrificing accuracy. Connectors allow you to simulate the desired mechanical behavior without having to create the detailed geometry or define contact conditions. Since connectors are virtual, you don’t need to model the physical 3D geometry to represent them. As a result, no mesh nor stress calculation is needed. This saves you a ton of time.
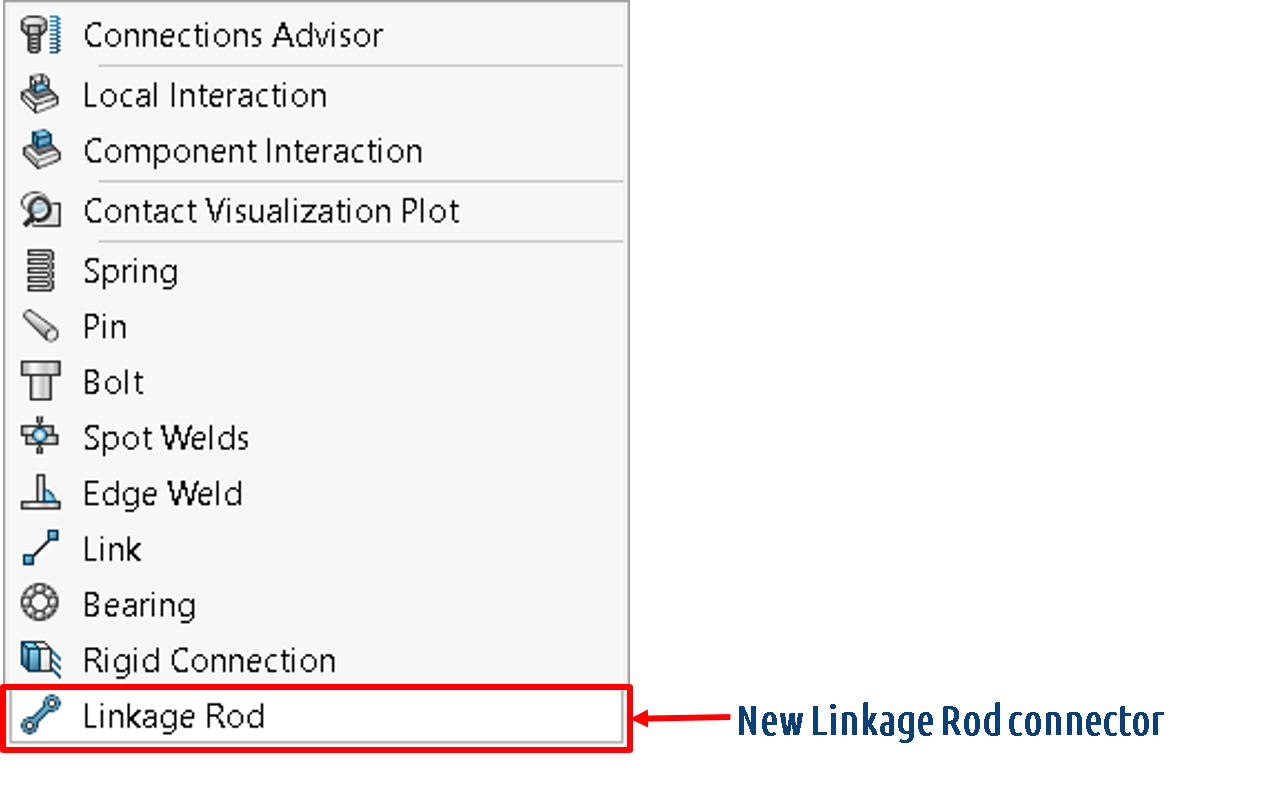
The new Linkage Rod connector enables you to simulate a rigid or flexible behavior between components in an easy yet powerful way. To define this connector, you can choose among cylindrical faces, circular edges, and vertices. The end joints can be set to give a rigid, pivot, or spherical connection. The link connector Cross Sections can be selected and given dimensions, including Solid Circular, Hollow Circular, Solid Rectangular or Hollow Rectangular. The default material for this connector is Alloy Steel but you can select any material from the SOLIDWORKS material library.
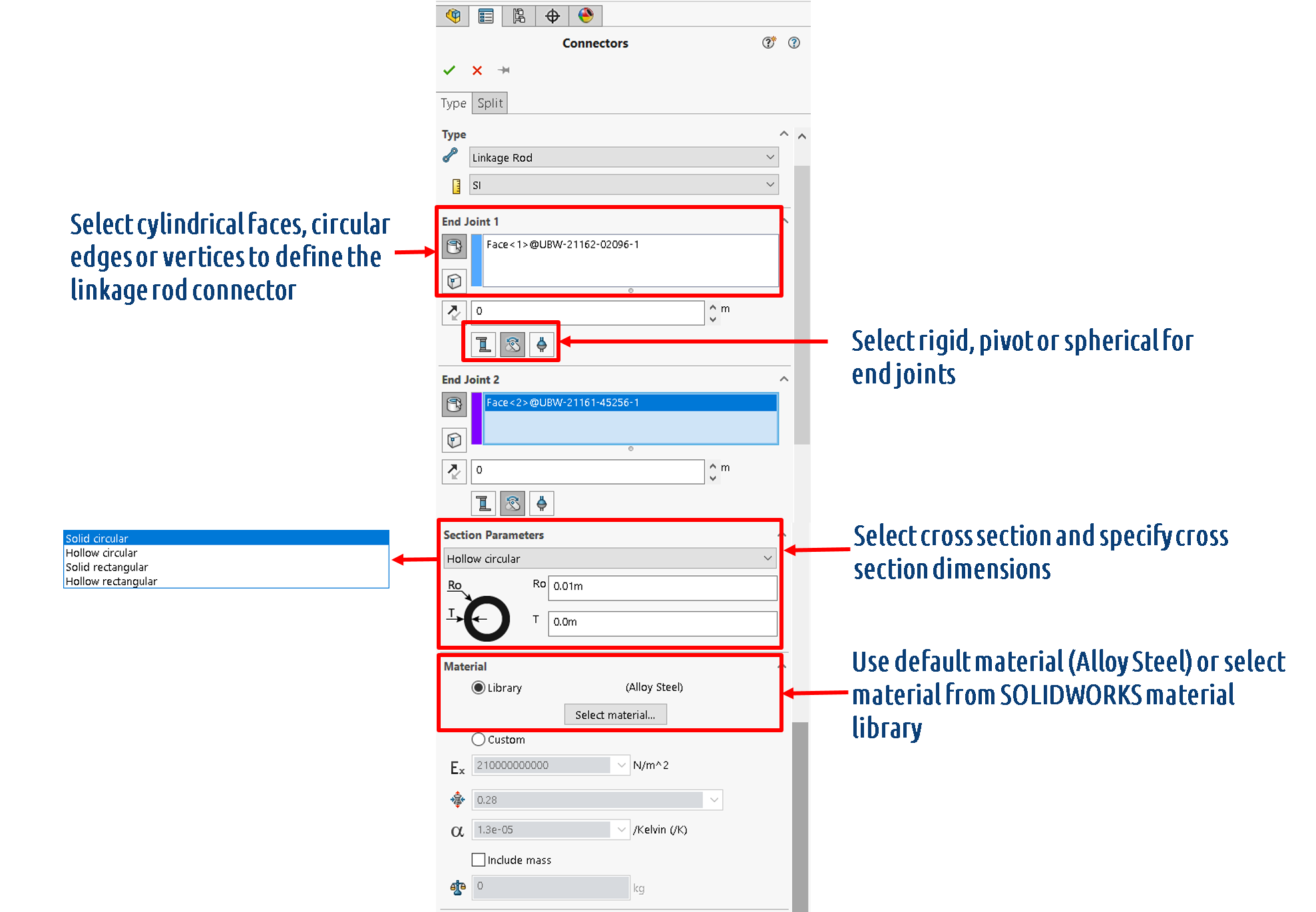
Once your simulation has solved, you can post process Shear Force and Axial Force, Bending moment and Torque for the Linkage Rod connector as shown in Fig 3. How cool is that?
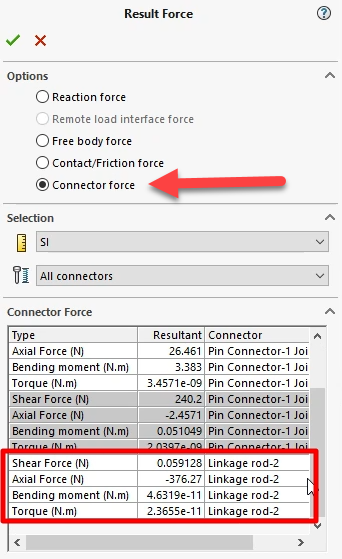
Let’s look at an example to see how the linkage rod connector can save you time. Instead of modeling the two pneumatic pistons on a Resemin Bolter truck (which are not the objects of interest since the high stress concentrations occur in the components above) we use the Linkage Rod connector to represent them. The assembly using the Linkage Rod connector to represent the pneumatic pistons solved in 3:01 minutes (with connector) whereas the assembly where we kept the pneumatic pistons without using connectors solved in 4:30 minutes (without connectors), or a reduction in solve time of 33%.
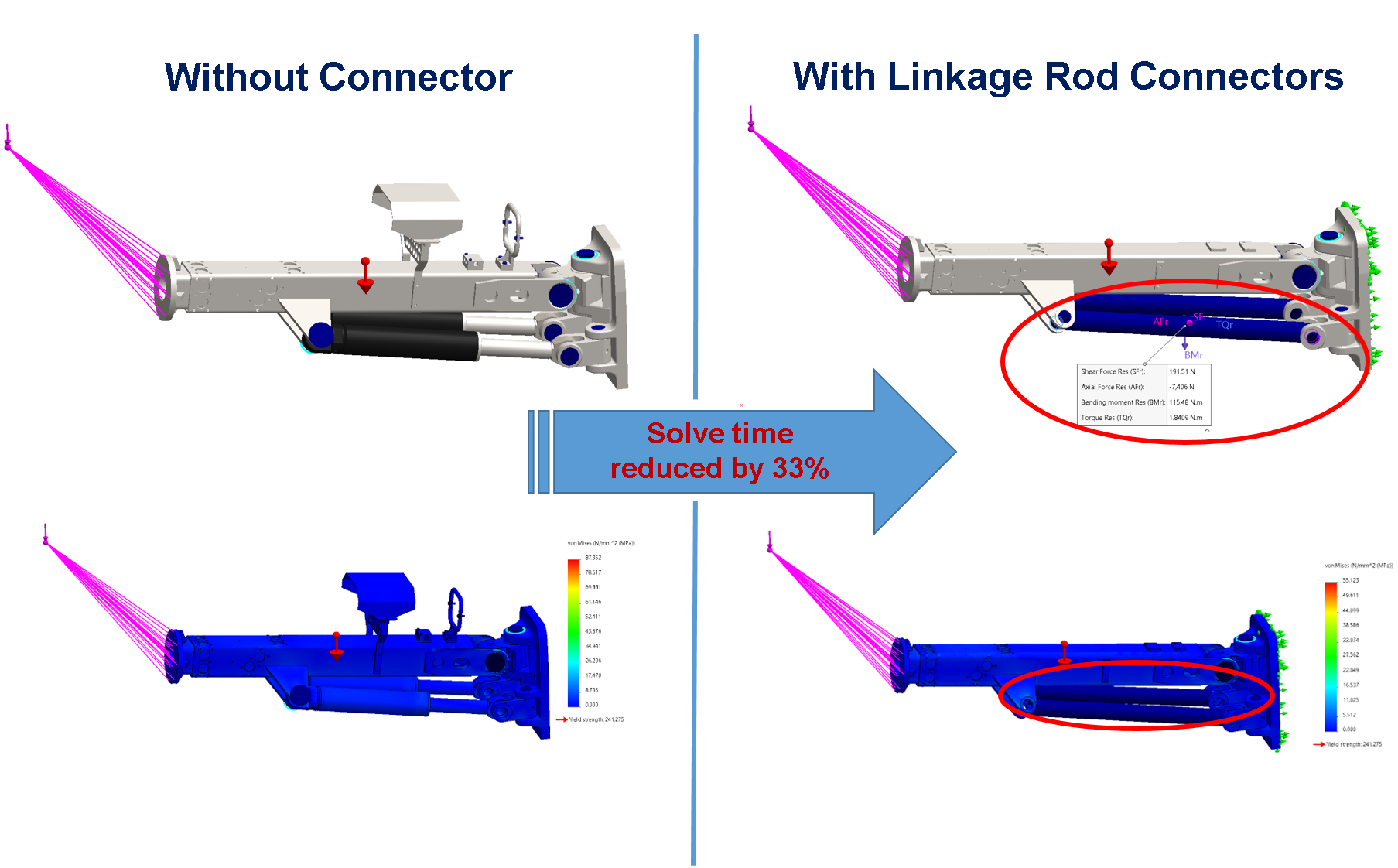
If you have not taken advantage of connectors in SOLIDWORKS Simulation to simplify your analysis and save time, now is a good time to start!
2. Blended Curvature-Based Mesh Is Now the Default
In SOLIDWORKS 2022, Blended Curvature-Based (BCB) is now the default mesher. BCB is a robust mesher that will mesh complex geometries. Some of you may know, BCB was introduced in 2016 and the reason you probably didn’t use BCB is either you didn’t know it existed or perhaps you thought it was too slow. With recent releases of SOLIDWORKS Simulation, BCB has matured and become significantly faster and more robust. Another reason that makes BCB attractive is it uses multithreading and parallel multicore processing to more quickly mesh components. This is especially true for large assemblies.
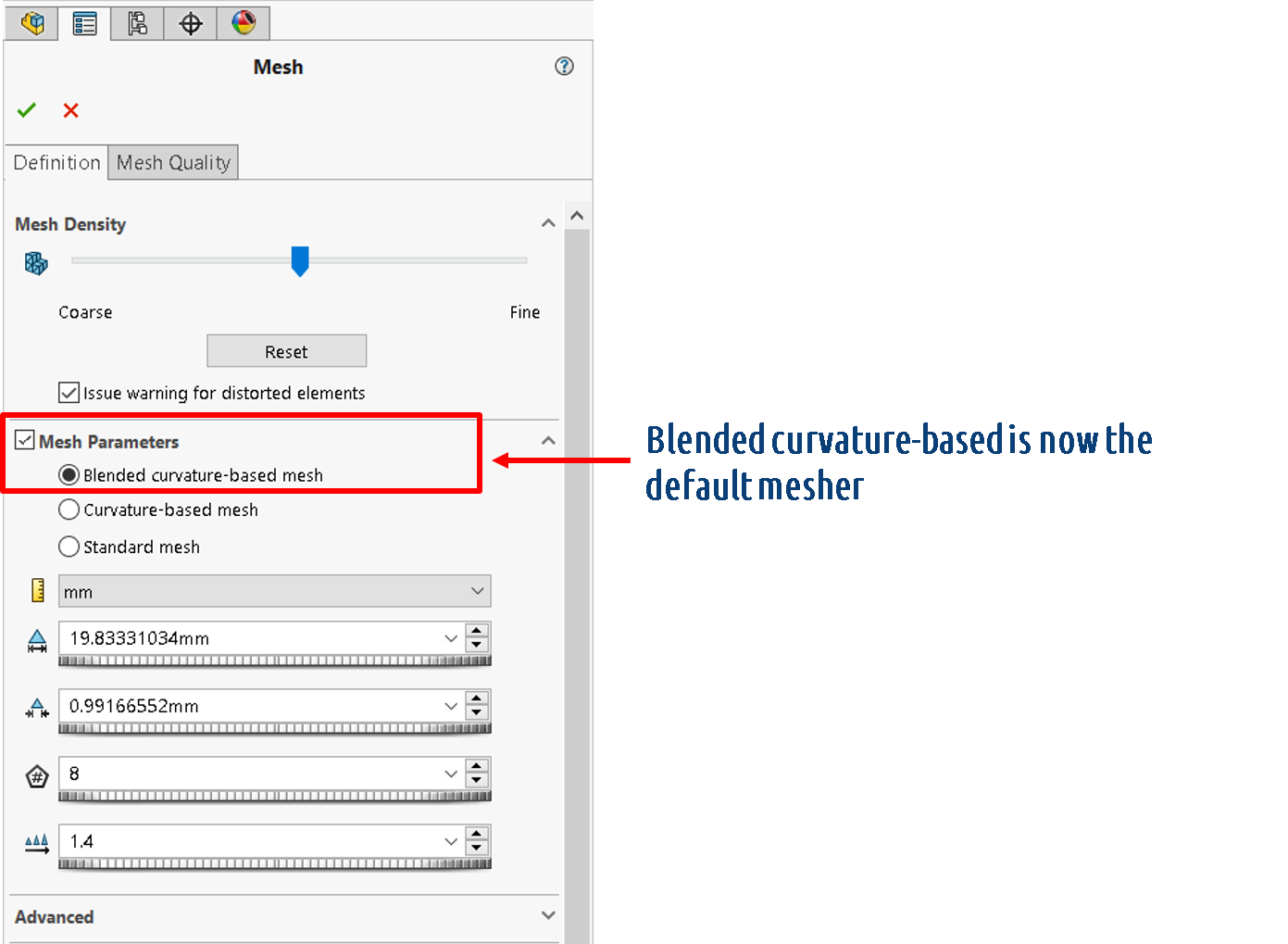
SOLIDWORKS Simulation 2022 also enables you to define BCB mesh size on the components regardless of the global mesh range. You can obtain optimum meshing by applying a coarser mesh size on bodies of least importance. For example, you can input mesh control dimensions that are greater than the Maximum BCB global size. Meshing unimportant bodies with larger element size not only expedites mesh creation but also reduces the data transfer and equation solving time in your simulation process.
3. Enhanced Bonding and Contact
Enhanced Bonding and Contact is a new enhancement that expedites solving time and improves contact accuracy. Our developers removed duplicate degrees of freedom in bonding and contact constraint equations; reduced bonding and contact constraint equations; improved constraint area calculation; re-tuned unit less parameter associated with contact penalty stiffness, and more. As a result, your models with Bonding and Contact interactions will solve considerably faster and the contact results will be more accurate. That’s like having your cake and eating it too! If you start using SOLIDWORKS Simulation 2022, and I recommend you do, you may note that performance improvements are more significant with the iterative solver (FFEPlus).
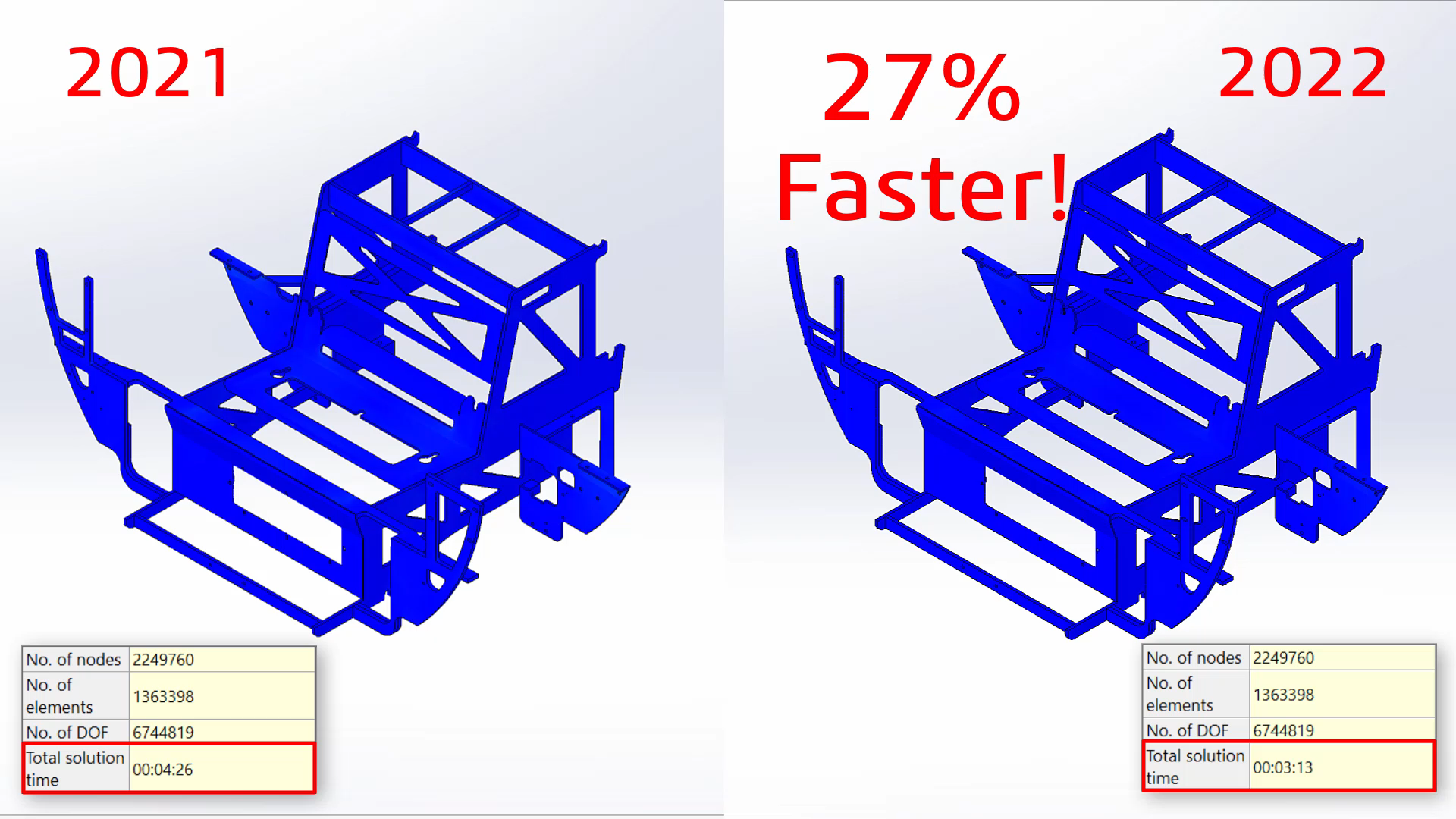
4. Automatic Equation-Solver Selection Extended to Nonlinear, Frequency, and Buckling Analysis
SOLIDWORKS Simulation 2022 includes an enhancement that selects the best equation solver for Nonlinear, Frequency, and Buckling studies. The selection of the best equation solver (Intel Direct Sparse or FFEPlus Iterative) depends on the number of equations, load cases, mesh type, geometric features, contact and connector features, and available system memory. For Frequency and Buckling studies, the automatic solver selection factors in the number of frequencies and modes in addition to the previously mentioned parameters.
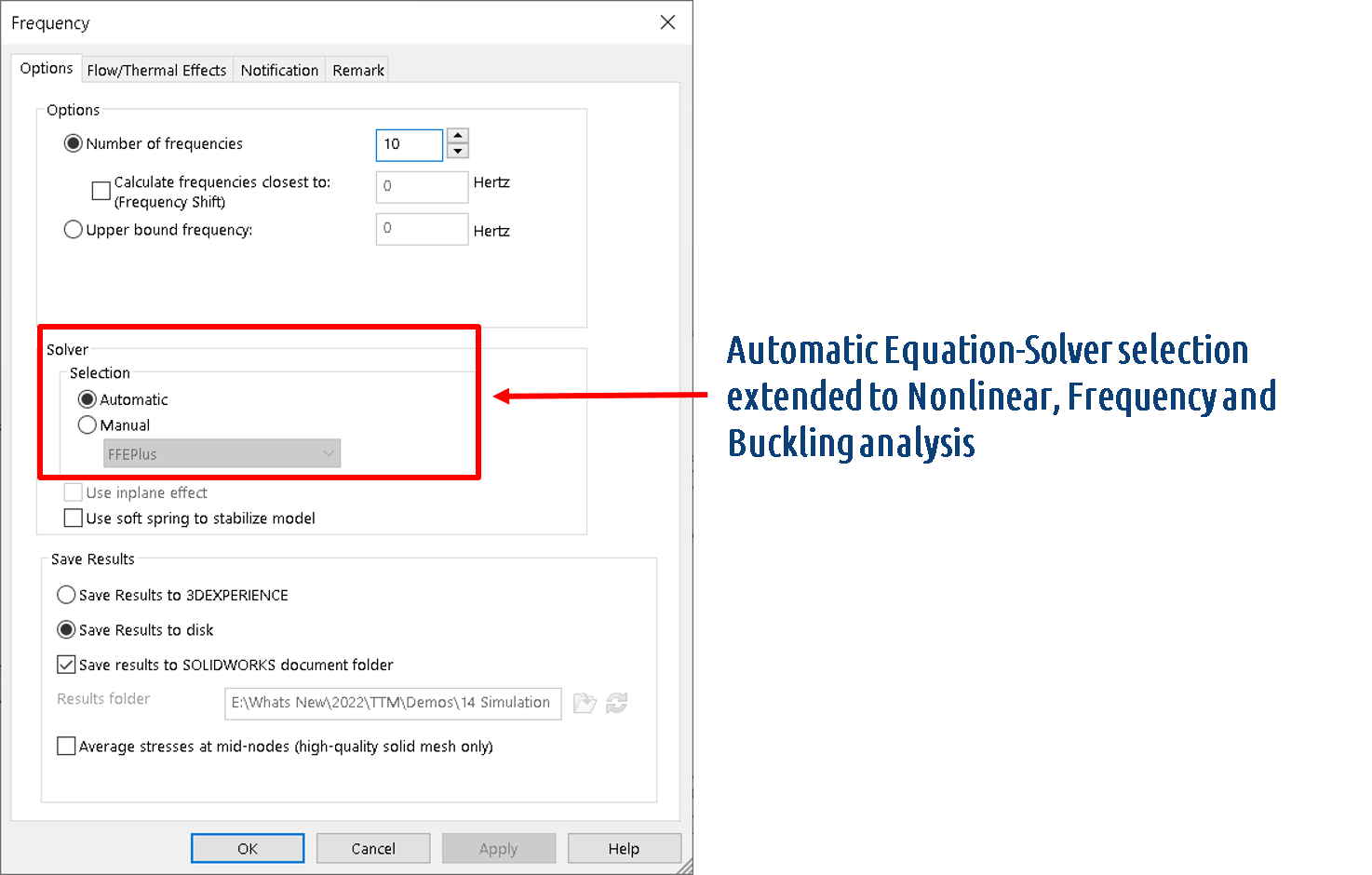
As you can see, SOLIDWORKS Simulation 2022 incorporates some serious productivity enhancements: Linkage Rod connector, Blended-curvature based mesher, Enhanced Bonding, and Contact and Automatic equation solver. We are excited to present them and other enhancements in SOLIDWORKS Simulation 2022. We look forward to hearing how SOLIDWORKS Simulation 2022 lets you work Smarter and Faster than ever before.
If you’d like to learn more about SOLIDWORKS Simulation 2022, please contact your local reseller.