Motorcycle Madness: Printing Pressure
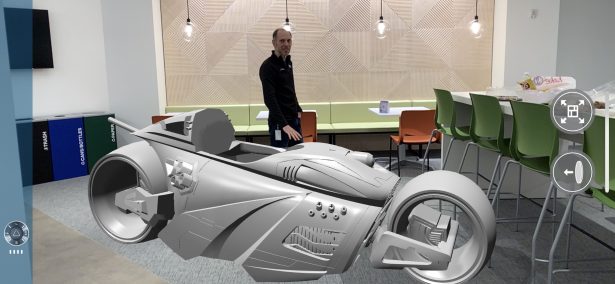
Tucked away in a corner of the warehouse space at DASSAULT SYSTEMES North American headquarters in Waltham, motorcycle parts are piling up. The Magic Wheelchair build team is hard at work, putting in late nights and spending their lunch hours in the 3DEXPERIENCE Lab to bring Ben’s bike to life.
We’re a month away from the reveal, and the team is in a good spot. Most of the foam for the bike’s body is cut and sanded, and the plywood for the frame has been machined. And what a frame! “It could be its own costume,” Annie said, and other team members agree. The bike is going to be 10 feet long and 37 inches wide—quite a big bike.
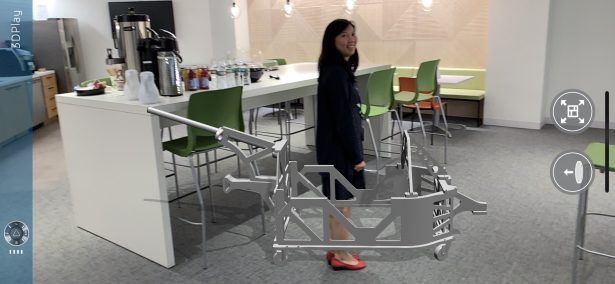
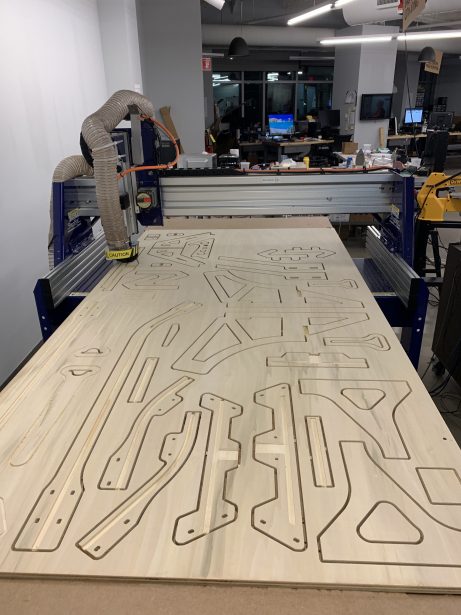
The rear tire is 12 layers of 2-inch foam, and the front tire is 6 layers of 2-inch foam and 2 layers of 3-inch foam. Remember the wheels made for the mini-Max-D? The wheels that were scale replicas of monster truck tires? The rear tire of Ben’s bike dwarfs that.
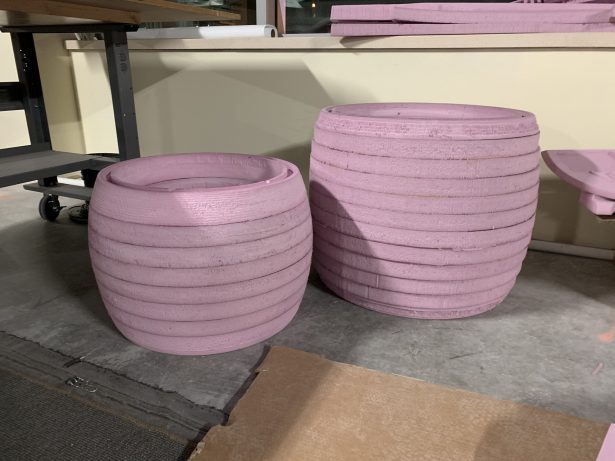
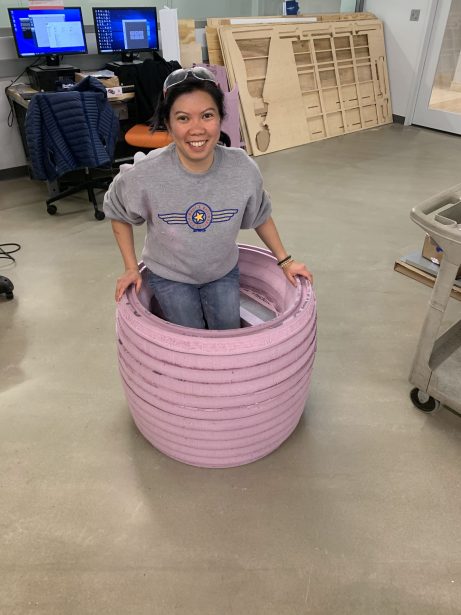
All of the 3D printed details are almost done. 3DEXPERIENCE Lab intern Madhu has been helping the team, watching over prints in the massive Gigabot 3D printer. He’s experimented with the print orientations: when printing one of the faux exhaust panels, Madhu had it lying flat, which led to a lot of supports and more weight. When printing the second exhaust panel for the other side of the bike, he printed it on its side, leading to less support material and therefore less weight. You can see the difference in how the layers came out.
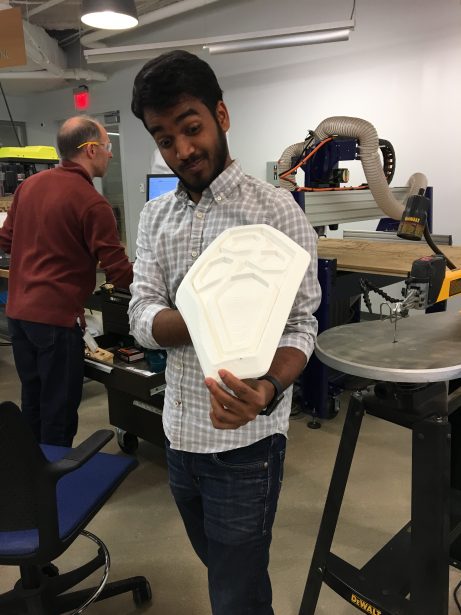
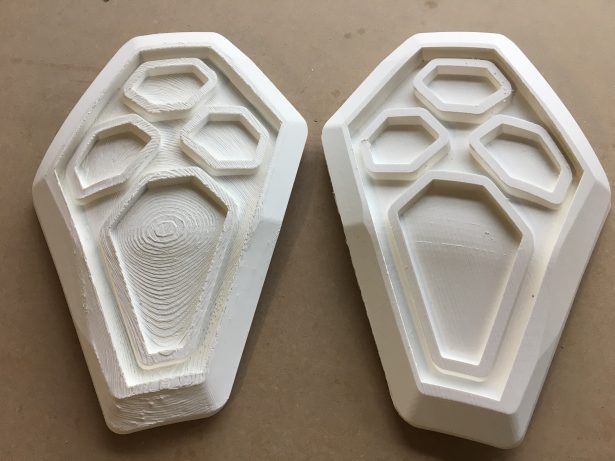
Now Madhu is in the process of 3D printing the channel for the LEDs in the rear wheel. If he has time, he’ll reprint the first exhaust panel, to lessen the weight on Ben’s bike.
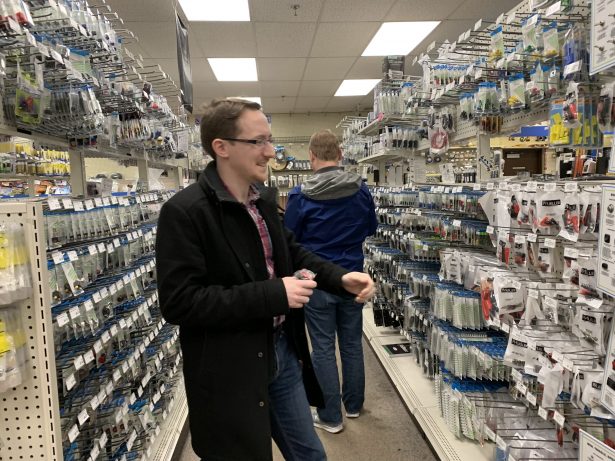
There’s still some questions on electrical: should the team connect Ben’s fun dashboard to the lights along the wheels and body, or should they run on separate currents? Team members David, Nicolas, Chinloo, Gabe, and Stephen took a trip to a local electronics stores to see what kind of electrical doohickeys were available.
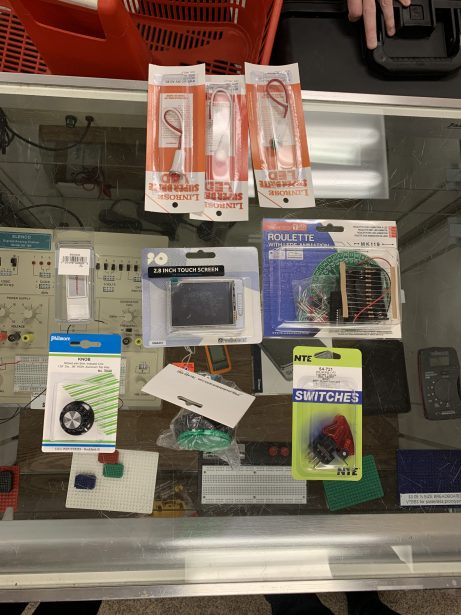
They looked at buttons, switches, knobs, different mechanisms Ben would have fun playing with. They also checked out what types of LEDs and boards were available. “We got ideas of things that would look cool,” explained David.
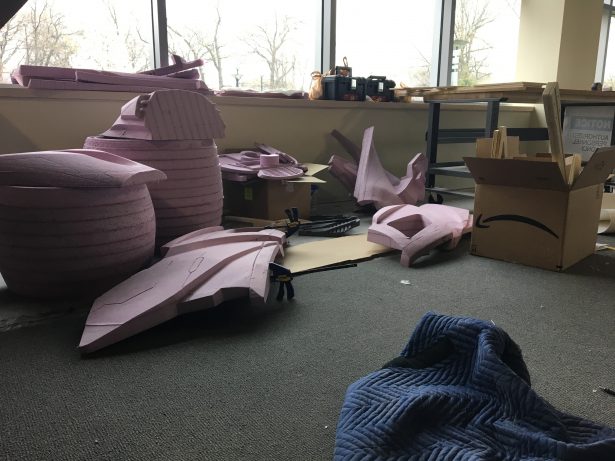
Now it’s time to finish up the machined parts and sanding. Some holes need to be plugged with joint compound, then sanded again. Finally, the team can begin adding hard coat to the foam pieces.
With a month to go before the big reveal, team members are confident they’ll be able to produce one heck of a bike for Ben, and give him a truly special day. We’ll see how the build continues and get revved up for some motorcycle madness!
Help support Magic Wheelchair and amazing kiddos like Ben!
SOLIDWORKS is working hard to make Ben the most incredible costume ever and help the non-profit Magic Wheelchair achieve its goal of providing kids in wheelchairs with epic costumes. SOLIDWORKS is funding Ben’s costume build in its entirety, but we invite all our readers to support Magic Wheelchair in Ben’s name! If you visit his classy.org page, you can donate directly to Magic Wheelchair and help support them and all the lives they touch with their great work. Stay tuned for more updates on this exciting build and get your engines revved for more motorcycle madness!
SOLIDWORKS is partnering with the Magic Wheelchair to create an over-the-top costume for a child in a wheelchair. According to their mission statement, “Magic Wheelchair builds epic costumes for kiddos in wheelchairs — at no cost to families.” Motorcycle Madness is an ongoing series dedicated to updating our readers on the current project’s progress.
Read about our previous build, Keep on (Monster) Truckin’ with Jonah here.