What’s New in SOLIDWORKS Simulation 2025
When it comes to our simulation strategy, the goal is simple: to enable you to get the best results for the least amount of work. SOLIDWORKS Simulation 2025 enables users to simulate more complex scenarios without adding the burden of modeling things explicitly and is designed to accelerate your simulation without costing you anything in terms of accuracy.
Take, for example, the connector and the bonding for contacts enhancements in SOLIDWORKS Simulation 2025, including the pin and weld connectors and the new spring connector, which we call a general spring, which allows you to really look at the behavior of how two components relate to each other. In a very simplistic way, you could say that every component is a spring in that if you push on it, it deflects in the same way that a spring does. Because components are generally not uniform in shape and stiffness, their “spring” behavior is complex in tension, compression and torsion.
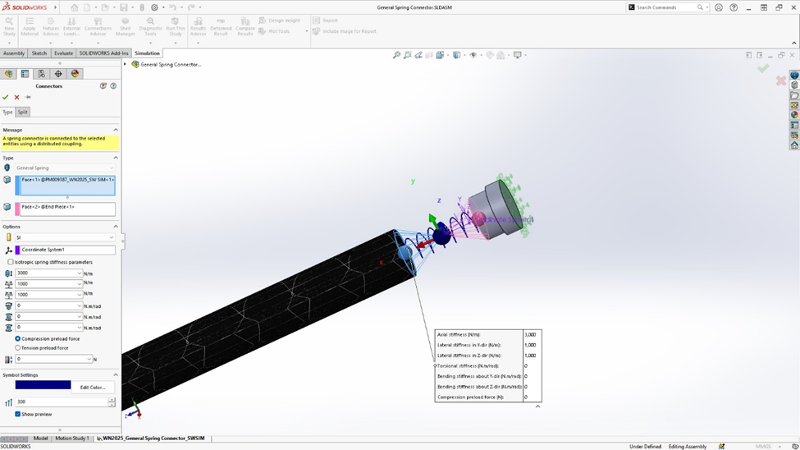
With a general spring, you can, for example, create a spring with a compressive but no torsional stiffness or one with tensile but no compressive stiffness. You can tune this spring to act in a very specific way, which means you don’t have to add a complex connection between two components.
This enables you to concentrate your effort on the components that you need to worry about and not on the components that you’re going to purchase. So, for example, if you’re going to buy a bushing or the bearing from a company, you can review the data sheet and find out what the stiffness is and plug it into a general spring. Therefore, you can focus on the things that you are designing that are being attached to that bushing or bearing, and spend your computational effort on the bits that you are designing and the bits you are making, and not spend it calculating the stiffness of a bearing or a shaft or a bolt, because you can get that from a datasheet and plug those numbers in.
You want to do things early so you can easily change the geometry. You don’t want to spend time adding all the fasteners, bearings and bolts—that’s just painful. So, you use the connectors to accelerate your simulation without costing you anything in terms of accuracy.
Mesh enhancements
Another truism in simulation is that the “mesh is king.” A poor mesh will result in an inaccurate answer. In SOLIDWORKS Simulation 2025, we’ve made a number of enhancements to the mesh that enable you to perform more accurate simulation studies and solve your simulations faster.
For instance, the enhanced node-to-surface bonded interactions improve accuracy for bonding offset defined by a user-defined gap range for bonding. In fact, you can expect improved solution accuracy for all bonding interactions, including solid-solid, shell-shell and solid-shell, that are based on either a draft-quality or high-quality mesh. The studies that support this enhancement include linear static, frequency, buckling, linear dynamics, fatigue, design scenario and pressure vessel.
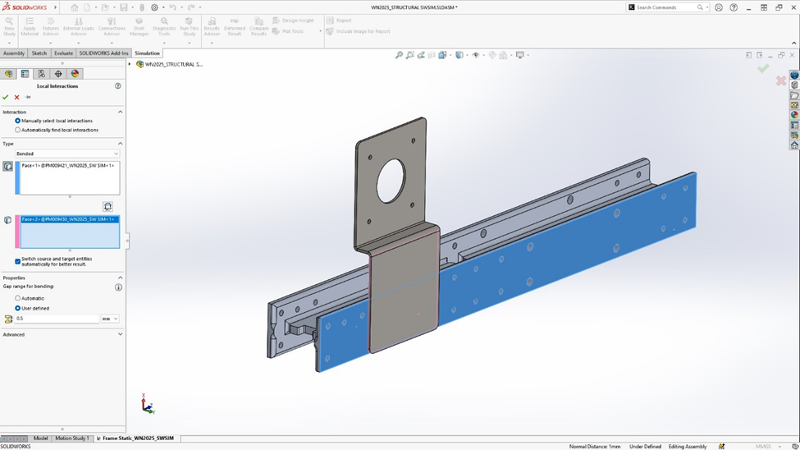
Simulation accuracy is also improved for studies with bonded curved surfaces when the mesh sizes of the source and target surfaces differ.
The algorithm that enforces surface-to-surface bonding integrates geometry correction factors that improve the representation of curved surfaces of cylindrical, spherical, and conical geometries. The integration of surface geometry correction reduces the stress noise at the vicinity of bonded curved surfaces, improving the solution accuracy.
On the structural side of things, we’ve made mesh improvements to improve assembly work when parts are various sizes, including large flat sheets with small bolts and holes, where the mesh needs to work smoothly from fine details to large areas.
This process is now more efficient as you have elements for your mesh where the geometry changes, the loads and restraints are being applied, or the components are coming into contact. Everywhere else, you can really sort of dial back the mesh because nothing’s really changing that much.
SOLIDWORKS Plastics
For plastic simulation where you’re looking at the manufacturing process, enhancements help ensure that your part will fit and function the way you intended. For instance, sink mark functionality has been improved so you can accurately predict sink marks when looking at the aesthetics of a part and make geometry adjustments, so you don’t have sink marks turning up where you have walls of different thicknesses coming together.
You can also more easily identify the cause of warpage in the design and injection process to avoid the plastic warping when it comes out of the mold.
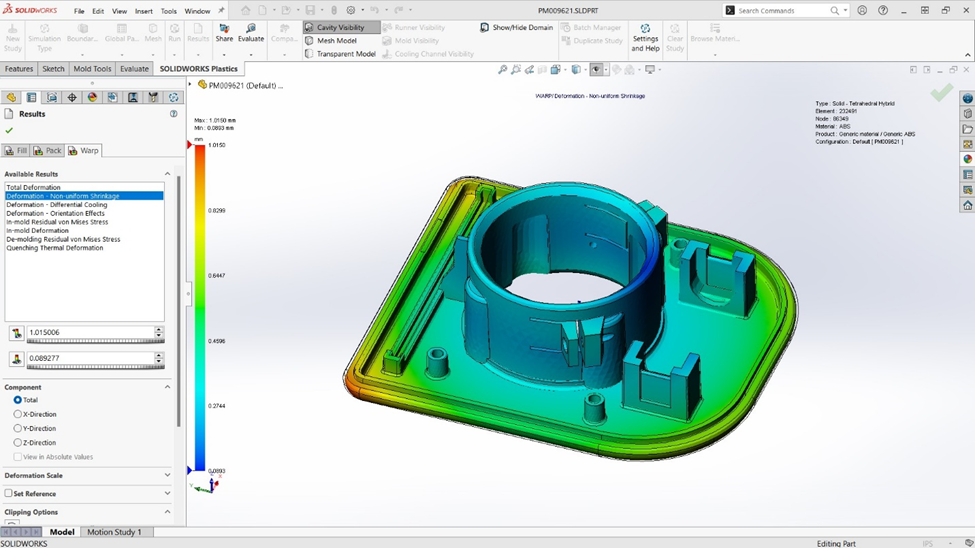
SOLIDWORKS Flow Simulation
The efficiency of SOLIDWORKS Flow Simulation users has been increased due to two key enhancements: improvements in both mesh performance and selections when working with large models. The impact of both of these enhancements is to reduce the overall simulation process, helping you work smarter and make use of different types of geometry, whether it’s a SOLIDWORKS, SDL, or a mesh file.
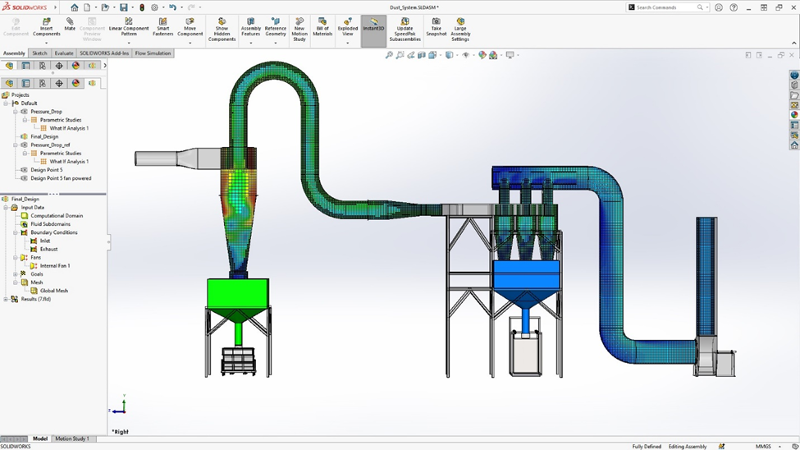
The overall theme for 2025 is all about efficiency and providing new tools to help you solve problems faster by allowing you to make good decisions based on your results and get answers fast.
Check out this PDF for a glimpse of the new enhancements and watch the video below to see them in action.
See what else is new in SOLIDWORKS 2025 to learn about enhancements to design, data management, electrical solutions and more.