Simplify the Material Selection Process When 3D Printing Plastic Parts
Of the 114,000 thousand plastics recognized by the Society of Plastics Engineers, roughly 600 are used in 3D printing processes. 3D printing materials are often referred to by their traditional names like ABS, nylon, polypropolene, etc., but be aware that many 3D-printed materials only mimic true thermoplastics. For example, a 3D-printed part in ABS-like material will have similar, but not identical, properties to a molded ABS part.
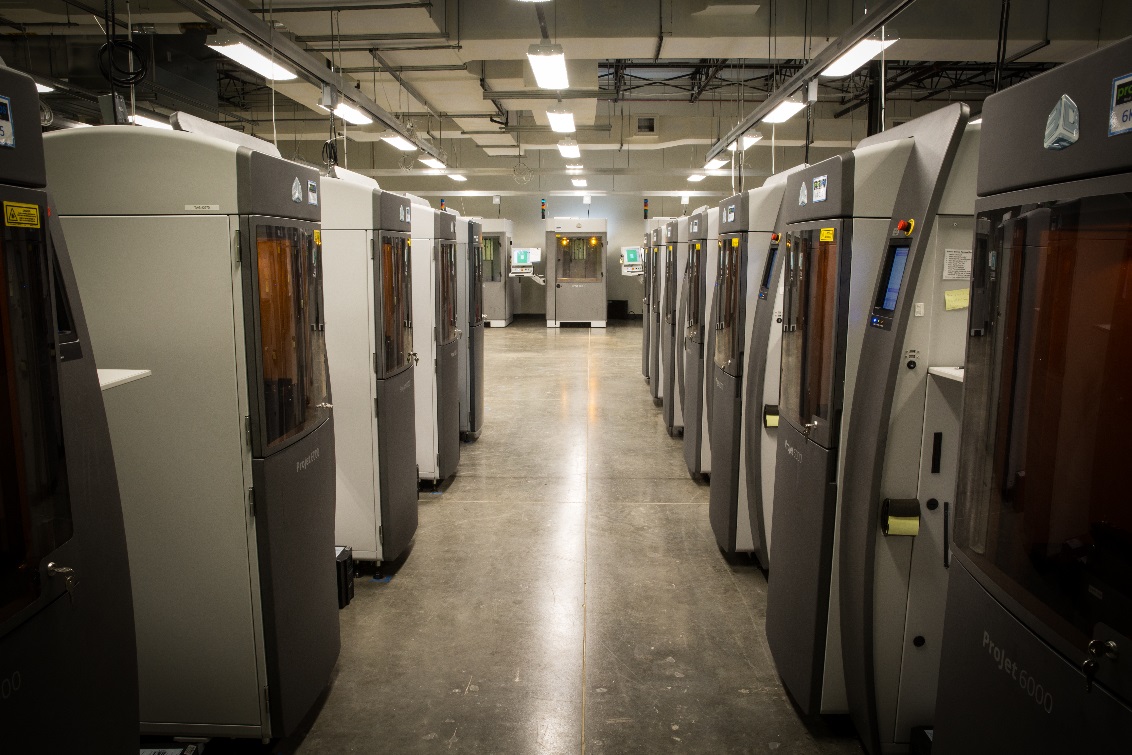
In this post, we’ll cover common 3D printing materials used to prototype plastic part designs. Although not an exhaustive analysis, these guidelines should help you narrow down your material options so that you only need to hunt down a couple data sheets for side-by-side comparison.
Polycarbonate-Like Materials
Accura 5530 material is transparent in color, temperature tolerant, and water resistant. It’s also resistant to automotive fluids making it suitable for under-the-hood and electrical applications. Secondary operations are required to achieve transparency and the final part will still retain a slight amber hue.
Accura 60 supports fine details while providing good stiffness in parts. Common applications include durable prototypes for automotive, consumer electronics and lighting components, as well as medical instruments. Accura 60 has a high tensile strength and modulus making this a good choice to replace polycarbonate (PC) when heat resistance is not critical.
ABS-Like Materials
RenShape 7820 has high strength and good dimensional stability. The material is black and commonly used in automotive parts, consumer packaging, electrical housings and toys due to its impact resistance and ease of secondary finishing that provides the appearance of production quality.
Somos Watershed XC 11122 is strong, durable, water-resistant material. It’s nearly colorless and mimics a clear engineered-grade plastic. Watershed’s high clarity makes it a perfect material for prototyping lenses, flow-visualization models and micro-fluidic parts. Post-build polishing will be required to get the material completely clear.
Polypropylene-Like Materials
Xtreme White 200 is comparable to both a polypropylene and ABS thermoplastic in that it offers strength and durability, lending itself well to application that require snap-fit features. Note that Xtreme White 200 has relatively low heat deflection.
DSM Somos 9120 is translucent in appearance, providing excellent resolution, and fine detail. You may want to consider Somos 9120 for parts with thin walls or small holes. The material is also one of the more flexible SL materials. Potential applications include automotive components, electrical housings, and medical devices.
Nylon Materials
PA 850 is similar to molded Nylon 11. This tough bioplastic is an excellent choice for parts requiring a living hinge and offers one of the highest elongation break thresholds in the nylon family. It produces a smooth surface finish, and good part detail. Another nice benefit is its superb chemical resistance and low water absorption—great for functional prototyping.
ALM PA 650 is Nylon 12, so it’s both stiff and tough. It presents a slightly rougher surface than other nylons, but offers high impact and temperature resistance, is very durable, and remains stable under a range of environmental conditions. It also has a low coefficient of friction, making it suitable for many types of gears and bearings.
Elastomers
A new development in 3D printing is the use of elastomeric materials, which has coincided with the introduction technology capable of 3D printing parts with multiple material properties such as colors and durometers. 3D-printed elastomeric parts may not have the durability to be used in end-use applications, but they can be a valuable development tool since you can produce low-volumes of parts without investing thousands into tooling in the prototyping phase.
Agilus 30 is a digital photopolymer used in the PolyJet 3D printing process. It’s unique in that it can take on multiple properties such as durometers and colors. And, it can combine those properties into a single build. This technology is frequently leveraged for overmold prototyping as well as finding the optimal durometer for an elastomeric part design.
Powder-based thermoplastic urethanes are also relatively new to the scene. The material is used in SLS machines and offers abrasion and tear resistance making it suitable for functional prototyping. The SLS TPU we offer at Proto Labs has a durometer of 70A, but additional durometers are on the market.
3D Printing Materials Decision Tree
Now that we have that out of the way. This chart will also serve as a nice quick-reference, so you can easily find the materials that align with your application’s requirements.
Conclusion
Among the smooth thermoset resins, durable nylons, and flexible elastomers, there is a 3D printing material out there that aligns with your product development requirements. Even though materials do not exactly match the characteristics of those used in traditional production methods like injection molding, they’re more than suitable for prototyping whether that be for form and fit or functional testing, and in some cases end-use parts.
If you want a more comprehensive look at 3D printing materials—both plastics and metals—I recommend reading through our 3D printing materials white paper. It includes a more detailed analysis of mechanical properties and is a great reference to sort through your 3D printing material options.