Paul Reed Smith (PRS) Guitars: Commitment to Innovation
As a world premier guitar manufacturer, PRS Guitars are known for creating some of the most amazing, high quality, reliable musical instruments. From Carlos Santana to Dave Navarro, many signature artists endorsed by PRS Guitars would also agree. As a long time guitarist, I have always been fascinated with guitars – not just playing them, but also learning how guitars are created and designed. My personal favorite feature about PRS Guitars has always been there finishes. The color selections for their guitar bodies are hard to overlook, along with their fingerboard inlay designs.
Jon Wasserman, PRS Guitars R&D Project Engineer, recently took time to answer some questions and share some insight on how PRS engineers use SOLIDWORKS to create and design their guitars, along with how SOLIDWORKS has impacted their production process.
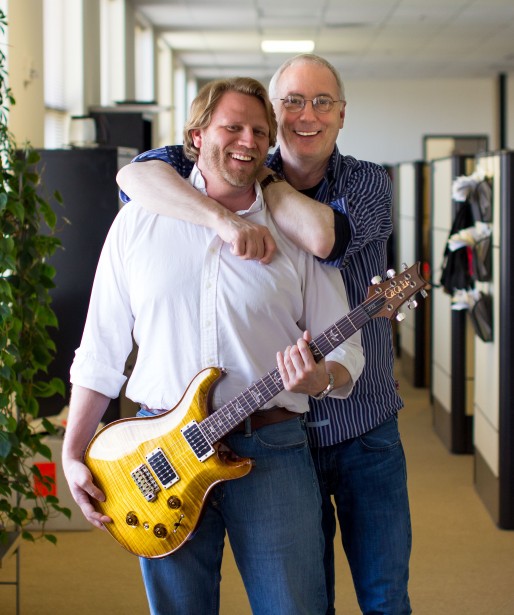
Could you describe your current job role with PRS Guitars?
After our Product Development team, led by PRS Guitars’ working founder, Paul Reed Smith, comes up with an idea for a new guitar or feature, I then am responsible for designing and engineering the new model or component level items to meet their requirements.
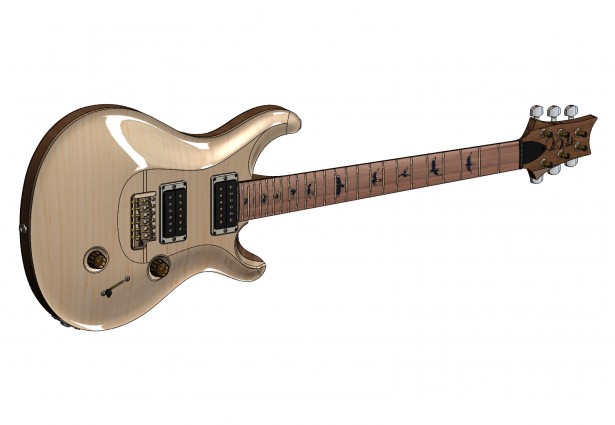
How much of your job requires you or your engineers to use SOLIDWORKS?
About 90% of our design work requires us to use SOLIDWORKS.
What do you mostly use SOLIDWORKS for? Is there anything you don’t use SOLIDWORKS for?
We mostly use it for our new product design work. In addition to our tooling, jigs, and fixtures design work. There are only a couple things we don’t use it for… inlay and more artistic work. We will eventually take that and place it into SOLIDWORKS for the purposes of documentation.
Are all of your products manufactured at your Stevensville, MD headquarters? If you do any overseas manufacturing, have you seen any benefits to using SOLIDWORKS when working with contract manufacturers?
All of our domestic products are made at our Stevensville, MD headquarters. We have an overseas product line, the PRS “SE Line,” that is made in Korea. We also have some component level items used in our domestic products made at overseas facilities. When working with contract manufacturers (component level and SE) we find using SOLIDWORKS has allowed us to better communicate the design intent. Especially for items not easily described through prints. For example, complex guitar shapes/carves.
Are there specific benefits towards the manufacturing process that are really noticeable?
We build a complete virtual prototype prior to starting any work on the shop floor, which allows us to see potential issues with assembly fit and finish prior to final product approval. Also, our tooling and fixture design work has become more seamless. We leverage the “top down” ability of SOLIDWORKS to allow us to speed up that process and reduce errors/re-work. Since using SOLIDWORKS we have been able to speed up the product design lifecycle, reduce re-work, predict failure, and save costs on guitars and their components.
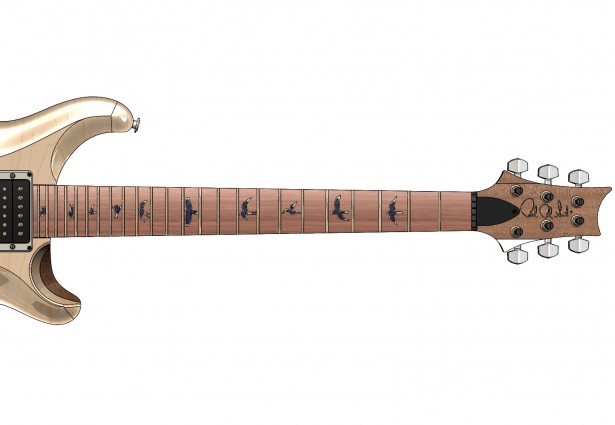
What did you do before using SOLIDWORKS? Were you using a different CAD software system?
We were primarily using our CAM software to do some component level design work and some guitar design.
Can you explain your design process? What steps do team members go through when coming up with a new design?
The idea for a new guitar or feature will come from Paul Smith and our Product Development Team. Then, for a new guitar, we will start with a basic layout of the guitar; contour, neck, bridge, pickups getting the balance and overall look right. We might add a carved shape to the top of the body and build that into a finished guitar body 3D model. We continue to add the features we want until we have a finished design. Sometimes we will start with an existing guitar design and “tweak” its shape and design to get a desired look.
What was the first PRS Guitar or PRS product designed and created with using SolidWorks?
The JA15 was the first designed and created using SOLIDWORKS.
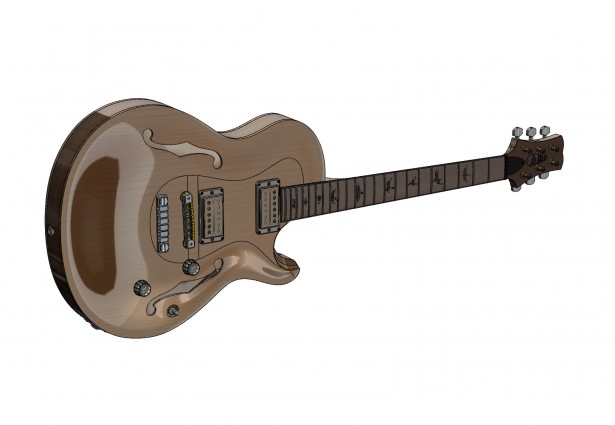
Is your team using SolidWorks to design other products, such as your Archon or DG Custom 30 amplifiers?
We are using SOLIDWORKS in our Acoustic and Amplifier areas. On acoustics we use it for neck design, body design, hardware, jigs and fixtures, and other process equipment. On amplifiers we use it for all sheet metal and assembly design in addition to conceptual work. We are not using to the extent we are in the Electric Guitar area, but we are working on expanding that.
PRS is really known for your finishes. How do the designers come up with wood choices and color selections?
PRS is known for our exquisite figured tone woods and the techniques and colors that our stain artists have developed to enhance the natural grain of the woods. As far as the colors, many of the inspirations stem from elements found in nature. Some colors combinations however, are experimental and fun and other times they start as an internal joke amongst employees and end up becoming trend setting in the market. Our Eriza Verde and Blue Crab Blue are good examples of some internal fun that turned into a very popular color.
Is there a different process for designing hollow body guitars compared to solid bodies?
The process isn’t very different when designing a hollow-body electric versus a solid-body electric. We use pretty much the same process except for the additional work of designing the “hollowed” portions of the guitar. We also rely on our past experience and knowledge blended with modern engineering to get the best acoustic tone from a hollow-body electric guitar without sacrificing the structural integrity and balance.
What was the design inspiration for some of the newer guitars you are making, most notably the Starla and Mira, which differs from what you’ve done in the past?
Two things come to mind here – obviously Market research is # 1 but breaking preconceived rules of who PRS is was also quite important. The Mira & Starla were the start of that and the S2 line will continue to grow the “breaking of the mold.” At the end of the day, integrity is most important so we strive to make the absolute best instrument for the price point. The instruments need to be reliable tools to create music with.
How does designing an artist signature guitar different from your other guitars?
When designing an artist signature guitar, we will usually start with what they like in our instruments or what they are already playing now and combine that with anything they would like to see, that would be specific for their needs. Sometimes it is a minor change to something existing and sometimes it’s a completely new instrument.
Whether you’re a musician, an engineer, or both – I hope you enjoyed learning about the design and creation process of PRS Guitars. From my own perspective – not only was I already a fan of their products prior to writing this blog, but now that I am more educated and have a stronger understanding of the commitment and hard work these engineers put into their craft my appreciation for PRS Guitars has reached a whole new level.
A huge thank you to Jon Wasserman and his engineering team for giving us an inside look on what goes on behind the scenes at PRS Guitars!
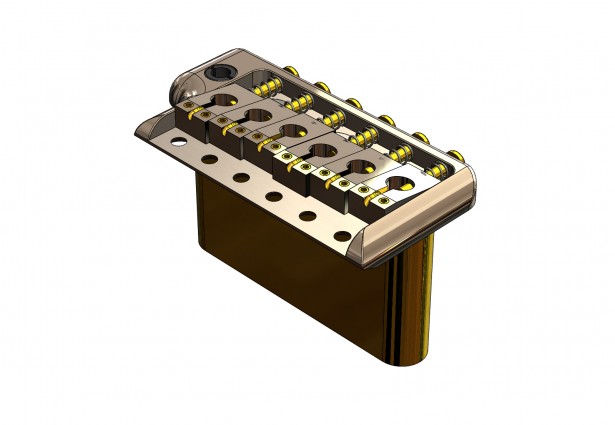
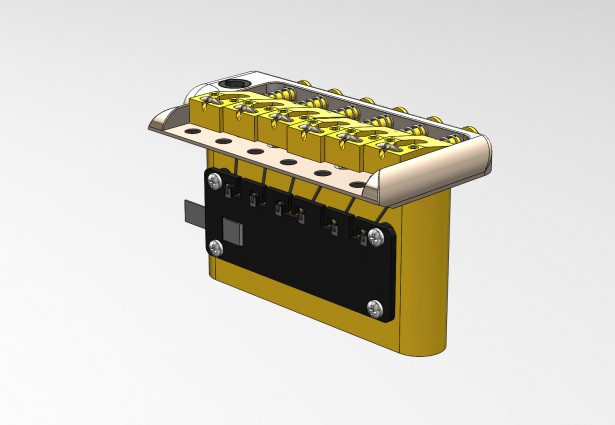
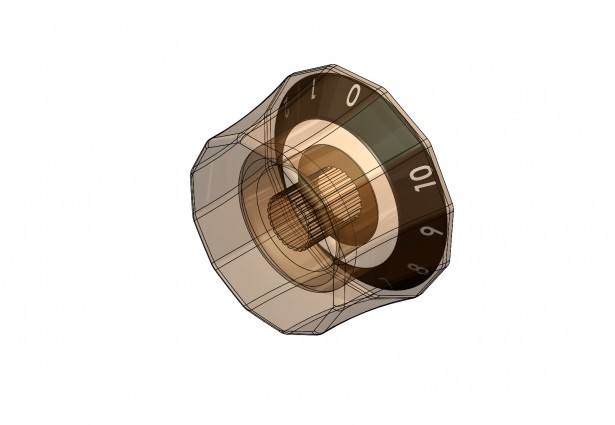