The Benefits of Integrating SOLIDWORKS for Taylor Guitars
Chances are, if you’ve ever found yourself adventuring into an Acoustic Room at your local Guitar Center, you’ve seen a Taylor Guitar. You’ve probably even picked one up along the way and started playing your favorite song – or at least attempted to play it! As a guitar player for almost 20 years now, I had never owned an acoustic guitar up until about four years ago, when I purchased a Taylor Big Baby Guitar. I have been a fan of Taylor Guitars ever since!
Taylor Guitars has established itself as being a leading American guitar manufacturer of premium acoustic and electric guitars. Outstanding playability, flawless craftsmanship, and stunning aesthetics are just a few of the reasons that many of today’s leading musicians such as Taylor Swift, Prince and Zac Brown make Taylor their guitar of choice. Earlier this year, their new 800 Series was honored with a Musikmesse International Press Award (M.I.P.A.) for Best Acoustic Guitar during the 2014 Musikmesse trade show in Frankfurt, Germany.
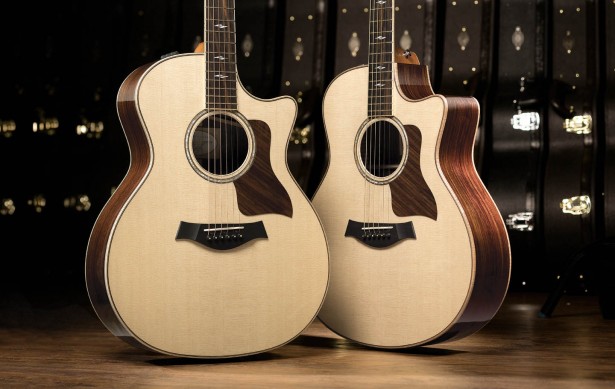
Taylor Guitars Engineer, Peter Hutchison, recently answered some questions to help educate us on how integrating SOLIDWORKS software has helped improve the creation and design process of their products.
Could you describe your current job role with Taylor Guitars?
I am a product development engineer working on everything from new products to tooling and equipment. I am involved in almost every process on the factory floor in one way or another. My biggest role is making sure that production can run smoothly and efficiently.
How much of your job requires you or your engineers to use SOLIDWORKS?
The group I’m part of emphasizes product and part documentation. Typically every part we work with gets modeled to ensure design consistency. This is not to say we have everything modeled, but all new work gets this treatment.
What do you mostly use SOLIDWORKS for? Is there anything you don’t use SOLIDWORKS for?
We use SOLIDWORKS for design of everything we make here. Our history is deeply rooted in a separate CAM program (Mastercam) for machining but because of the compatible nature of the two programs we are able to work with both.
Are all of your products manufactured at your El Cajon, CA headquarters? If you do any overseas manufacturing, have you seen any benefits to using SOLIDWORKS when working with contract manufacturers? Are there specific benefits towards the manufacturing process that are really noticeable?
All of our products are manufactured between our El Cajon plant and our Tecate, Mexico plant. Both facilities are maintained and managed by us (they are only 40 miles apart) and effectively, we are designing everything for both factories. SOLIDWORKS plays a bigger role for us in overseas manufacturing is in specialized components such as our tuning machines and strap buttons. We are able to design the parts here and have them made to spec very easily by transferring a model rather than a complicated drawing.
What did you do before using SOLIDWORKS? Were you using a different CAD software system?
Before SOLIDWORKS it was a dark, cold and lonely world. Well dark anyway; Mastercam uses a default black background. However here at Taylor I was hired on partially because of my SOLIDWORKS experience; I’ve not known this business without it. Personally I picked up using SOLIDWORKS at the university laboratory I worked in. There is great value in proliferating inexpensive student versions of the software where the future engineering minds are incubating.
What benefits have you seen since using SOLIDWORKS?
Time is a valuable thing. In some of the more basic CAD programs, drawing a line can be a chore–much less making an accurate geometric representation of a part. With SOLIDWORKS, I can have relatively complicated parts drawn up very quickly.
Can you explain your design process? What steps do team members go through when coming up with a new design?
We have a couple of different processes we go through, depending on if we are updating an existing process, developing a new process or developing a new product. Typically when we put together a new product, the Master Luthier builds a prototype instrument and tests it out. At that point we take whatever geometry they have created, measured or drawn, and model it following a basic set of process operations we’ve developed.
From that model we develop tooling and production programs for CNC machines. Guitar building is both a subtractive and additive process. We start with large material that has to get cut into pieces, shaped and then glued back together. Part of what we use SOLIDWORKS for is following that whole process through our feature tree to keep track of every cut and glue joint. If something doesn’t line up in the product we can usually find the point in the process where the parts fell out of spec simply by scrolling through the steps in the model.
For other development processes we use SOLIDWORKS as the direct design tool. For example if we are developing a new machine to improve a process, we’ll start with SOLIDWORKS and drive the process from the model.
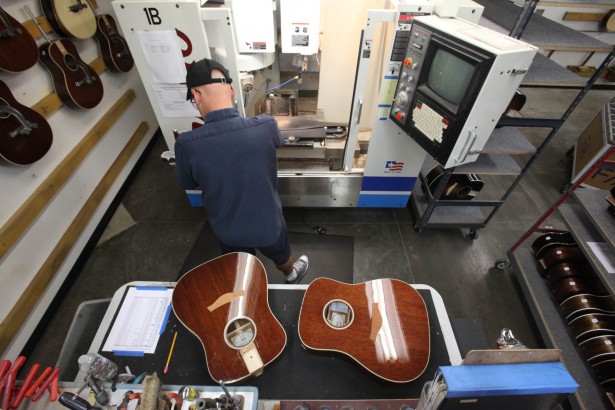
Has using SOLIDWORKS software made it easier to design both your acoustic and electric guitars?
In a word, yes. As I mentioned, the Luthier dreams up the design but most of the geometry they start with is two dimensional (sometimes on a napkin even) we take that and give it depth. We’ve run into situations where what we see on paper is just not possible three dimensionally and that saves time and frustration later because we can address it before the first piece of wood gets processed.
Are there any inherent design challenges you face when designing your acoustic guitars? How has SOLIDWORKS helped address them?
One of the hardest things to predict is where a structure with inconsistent materials will come to rest when put under tension. Spring-loaded design is not an easy challenge to work with, especially when you are trying to perform processes after that state exists. For example, we bend tops and braces into a shape when we glue them, and the result will be something between the shape they were formed in and flat. We can model that, but what we can’t predict precisely is where exactly the real parts will be for the next operation. SOLIDWORKS can get halfway there and that’s further than we can get by guessing.
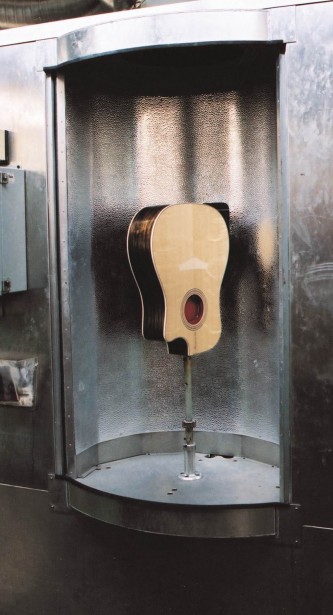
As an owner of one of your Big Baby acoustic guitars, I’m particularly interested in knowing if any part of that model was designed using SOLIDWORKS?
The Big Baby guitar predates Taylor’s use of SOLIDWORKS. You can take pride in saying it was designed “old school.” Since its design, we’ve updated processes for it and made improvements using SOLIDWORKS, and will likely do more in the future.
I would like to thank Peter Hutchison and his engineering team for taking the time to share some insight with us! If you would like to learn more about Taylor Guitars I encourage you to check out their website for more information.