3D Sculptor: Reverse Engineering and Sub-D Modeling
You can easily and quickly create and share organic and ergonomic 3D models with 3D Sculptor, but did you know that 3D Sculptor’s xShape app can also help you make quick work of reverse engineering, including transforming tessellated geometry, like the mesh geometry output from topology optimization or generative design, into smooth surfaces?
Surfaces from Scanning
3D laser scanning is becoming more popular due to the availability and affordability of handheld 3D scanners. However, the mesh data produced from a 3D scan is typically not the quality required for a final design. Oftentimes surfaces are lumpy and the mesh data is tessellated and has holes where the scanner missed geometry.
In addition, you are usually scanning an object to create a new version of it, or to create a mate or a close match to the one being scanned. In these cases you want to be able to quickly modify the geometry to get the exact shape you need.
Surfaces from Optimization
Similarly, outputs from topology optimization and generative design create geometries that are typically not considered final design shapes: The surfaces produced look like they have been hit with a thousand hammers.
In most cases designers and engineers want to smooth tessellated geometry to create a design that is manufacturable or just more aesthetically pleasing. You need a way to create smooth surfaces quickly. This is where 3D Sculptor’s xShape app comes in. 3D Sculptor makes quick work of smoothing out surfaces, whether from a 3D CAD file or mesh data produced from the aforementioned technologies.
Simply use the shape you have, in any condition, as a reference or template in the background. Smoothing and blending surfaces is a snap, and continuous curvature between the surfaces is built in.
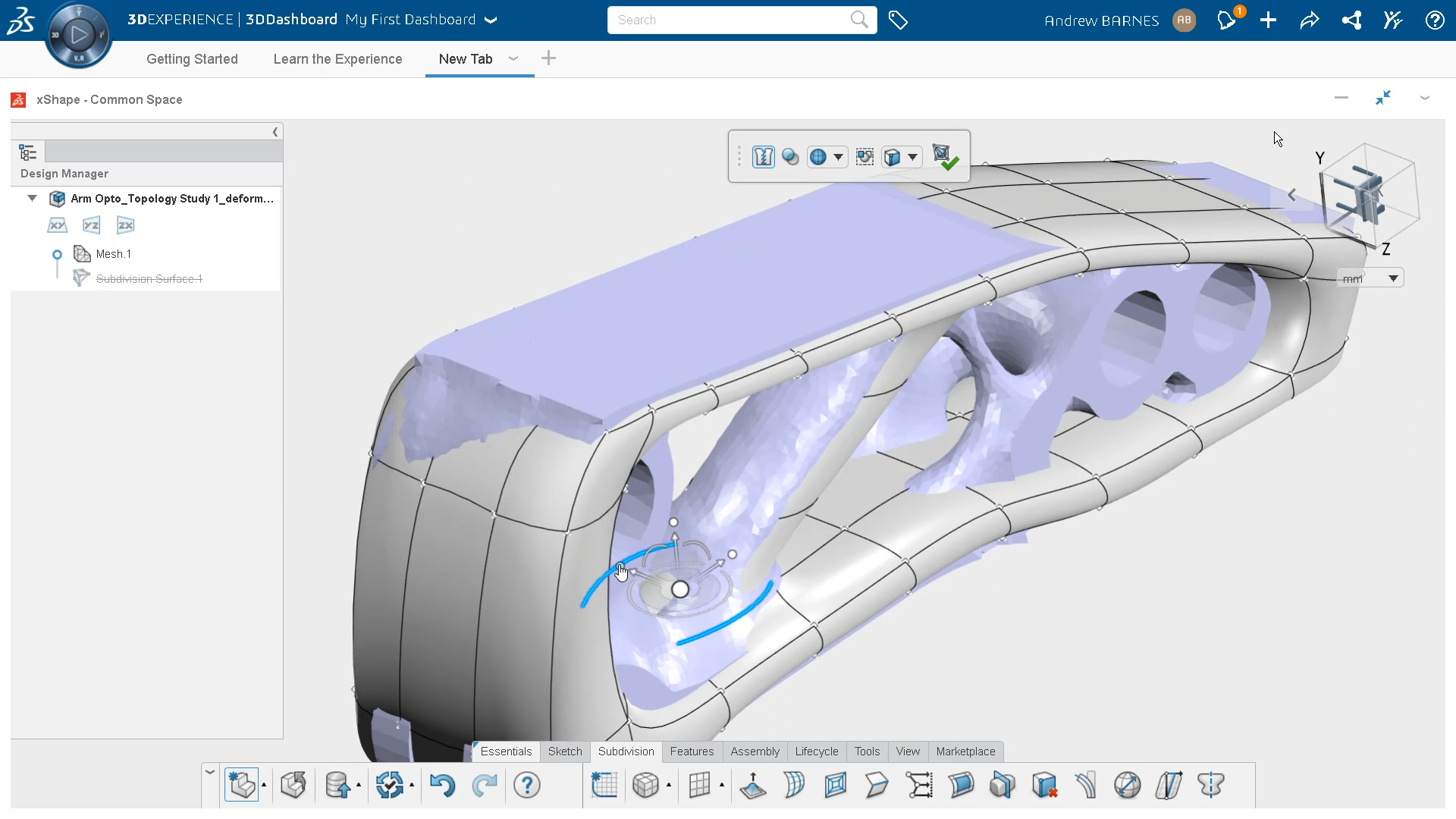
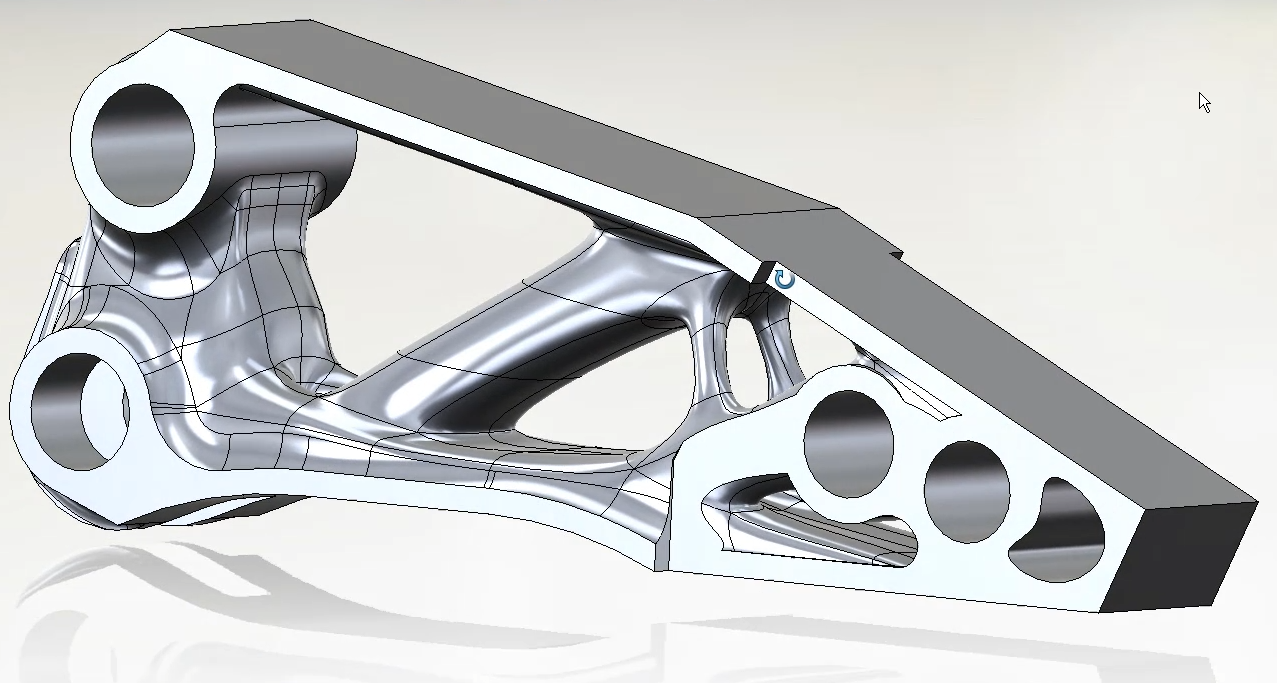
3D Sculptor vs. Parametric Surfacing
3D Sculptor is a lot like clay modeling, but on a computer. Most designers start with a sketch, imported image, or actual 3D model as a reference in the background and design the shape around those types of reference guides.
However, some designers like to draw their designs freehand, with nothing as a reference – whatever comes into their head. As with reverse engineering and smoothing of tessellated mesh with 3D scanning and topology optimization, designers start with a 3D model as a reference.
Basically you sculpt or “skin” a shape around a mesh or model to make it smooth and then modify it as the concept or idea develops. In 3D Sculptor, you can quickly push, pull, scale, crease, and bend your model to get the shape you desire.
Using parametric surface modeling to attain the same result would be extremely difficult and time-consuming. One surface might require creating dozens of control curves, so making even small topology changes, like adding a sharp crease or flattening an area, could be extremely time-consuming and may require starting the design from scratch.
Designs that take only a few minutes to create with 3D Sculptor often took hours to create with traditional parametric surface modeling, and changes that take seconds in 3D Sculptor used to require that a designer start over with parametric surface modelers.
3D Sculptor is so easy and changes are so fast that it is hard to compare with traditional parametric modeling. You must experience it to believe it.
Get Started in no time!
All you need is an internet connection and a web browser. No special hardware required.
If you do reverse engineering, topology optimization, or generative design, you now have a fast way to smooth out surfaces. Remember, changes in a model made with 3D Sculptor can be propagated through to update in SOLIDWORKS® desktop.
Please feel free to make comments below or visit the 3D Sculptor website for more information. If you want to give 3D Sculptor a try, click on the banner below to get set up for your very own seven-day trial of 3DEXPERIENCE Works solutions today.