Introducing Fluid Dynamics Engineer
Liquid and gas flows can have profound effects on the performance of designs. The earlier you can understand these effects, the better you can adapt your design to either mitigate or enhance them. For many industries, design is all about maximizing efficient fluid flow for cooling or processing, for others it’s about resisting and controlling the forces generated by the flow.
This means that design engineers need to be able to assess the fluid flow around or inside their products efficiently and accurately—exactly what the new Fluid Dynamics Engineer role delivers. Fluid Dynamics Engineer enables design engineers to carry out high-fidelity internal and external fluid flow and thermal simulations, delivering actionable information to improve a product while designing it.
Access to fast, accurate fluid flow solutions allows a design team to evaluate multiple design alternatives so they can create optimal flow distribution, efficient thermal management, minimal pressure losses, or whatever key flow performance their product requires. Possessing this information early in the design cycle can reduce costs while improving performance and quality.

SOLIDWORKS Designs
Because the role is on the 3DEXPERIENCE® platform, the user benefits from all the platform’s capabilities. For example, there is direct associativity with SOLIDWORKS® data saved on the platform, so any changes in the design are easily updated in the simulation and the results are reflected in the design.
Additionally, the cloud environment leverages cloud resources to solve large problems more quickly than what would be possible in a desktop-only environment. Unique engineering collaboration empowered by the 3DEXPERIENCE platform allows design engineers to create projects, brainstorm on design ideas with their team, and review design and simulation data easily to make informed decisions.
Intelligent Guidance
Setting up a simulation can be complicated and tedious, especially for new users, so Fluid Dynamics Engineer includes an intuitive User Assistant that guides the user through the steps required to set up a simulation.
Each step, or action, is clearly presented with a choice of commands that can be performed to complete the step. As the user works through the process, the simulation setup is continually monitored to provide feedback regarding any missing items or any specific warnings the user should be mindful of.
This guidance is provided via a panel through which the user can access integrated help for additional information if needed as they work through the steps. Experienced users can directly access the commands via the panel, which indicates warnings in any scenario.
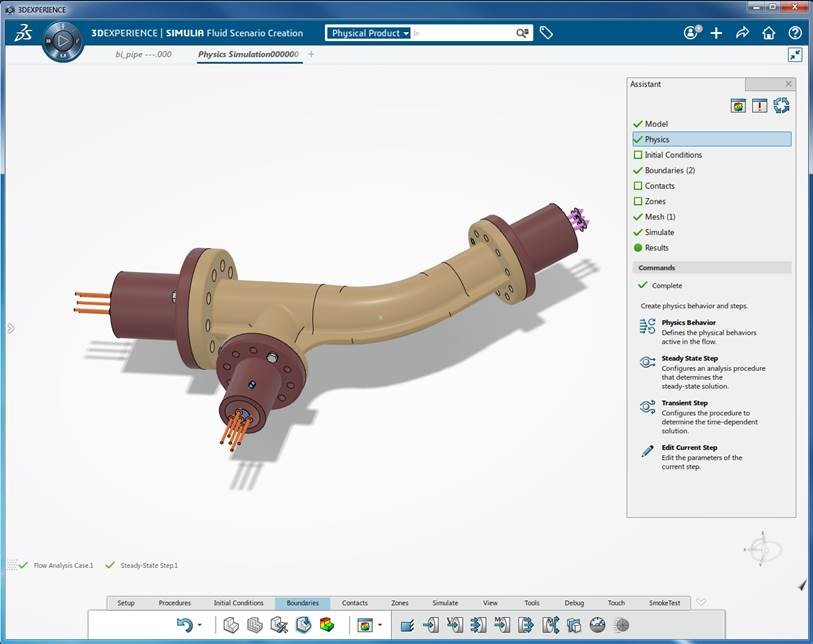
High-Fidelity Flow Simulations
An additional benefit to having the fluids role on the platform is the ability to leverage additional simulation roles for performing structural simulations for thermal-stress testing that enables additional multi-physics capabilities that will be added to future releases of the 3DEXPERIENCE Works portfolio.
The Fluid Dynamics Engineer role provides SOLIDWORKS design engineers the ability to quickly analyze the fluid flow and thermal transfer behaviors of product designs as part of the design iteration process. The guided simulation setup greatly assists the user in gaining proficiency in setting up a fluid simulation with very little domain knowledge.
This role will be a great benefit in the design processes that could benefit from early indication of how a product will perform in a fluid environment. Check out the SIMULIA fluids web page or contact your local reseller for more information.