J.A.M.E.S GmbH – Innovation aus dem 3D-Drucker: Additiv hergestellte Elektroniksysteme
Zusammenarbeit als Triebfeder für Innovation. Das ist sicherlich keine neue Erkenntnis, unser Weg dahin jedoch schon. Wie dieser Weg aussieht und wie Zusammenarbeit unser Geschäftsmodell prägt, möchte ich Ihnen in diesem Blogbeitrag näherbringen. Mein Name ist Rolf Baltes und ich war von Anfang an beim Aufbau der J.A.M.E.S GmbH dabei, einem Joint Venture von Hensoldt und Nano Dimension. Kurz zwei Sätze zu diesen beiden Firmen: HENSOLDT mit Sitz in Taufkirchen bei München entwickelt Sensorlösungen für Verteidigungs- und Sicherheitsanwendungen. Das israelische Unternehmen Nano Dimension ist Anbieter von intelligenten Maschinen für additiv gefertigte Elektroniksysteme kurz AME (Additively Manufactured Electronics).
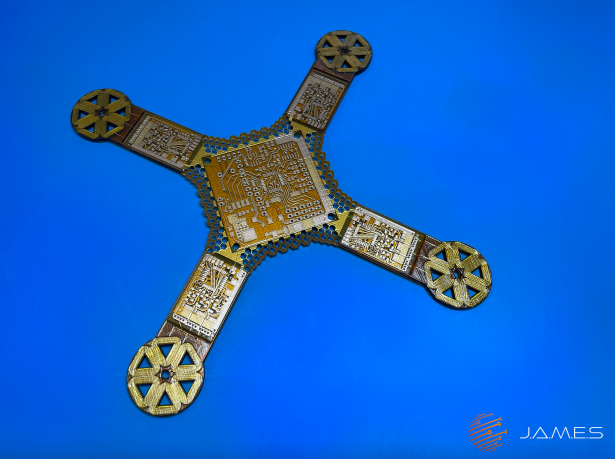
Startup mit Historie
Die Gründung von J.A.M.E.S erfolgte im Juli 2021. Dennoch reicht unsere Geschichte bis ins Jahr 2016 zurück. Damals leaste Hensoldt eine Beta-Maschine des 3D-Druckers DragonFly von Nano Dimension, um erste Erfahrungen mit dieser neuen Technologie zu sammeln. Drei Jahre später kaufte das Unternehmen schließlich das DragonFly 2020 Pro System, und seitdem ist HENSOLDT im Bereich AME aktiv. Als ich – ebenfalls in 2019 –nach meinem Studium zum Mechatronik-Ingenieur und anschließender Promotion bei HENSOLDT startete, war es fast so, als hätte der DragonFly Drucker auf mich gewartet.
Technologie sucht Anwendung
Als HF-Entwickler sollte ich einerseits neue Anwendungen für den 3D-Drucker voranbringen, um mithilfe von AME schneller und kostengünstiger auf Kundenbedürfnisse reagieren zu können. Anderseits sollten wirtschaftliche Perspektiven gefunden werden, wie HENSOLDT künftig von AME profitieren kann. Obwohl es sich damals um eine grundlegend neue Technologie handelte, erkannte HENSOLDT früh ihr Potential als essentielle (zukunftsweisende) Ergänzung zur herkömmlichen Elektronikfertigung. Die Möglichkeit, aus leitfähigem und nicht-leitfähigem Material in Form von Tinten leitfähige und isolierende Strukturen drucken zu können, erweiterte den 3D-Druck somit auf elektrisch funktionale Anwendungen. So entstehen additiv gefertigte Schaltungsträger, wie Kondensatoren, Spulen, Antennen, Filter oder Kühlkörper, um die Abwärme von einem Chip aus dem Bauteil herauszubekommen. Die Anwendbarkeit von AME ist vielfältig. Die entscheidende Frage für HENSOLDT war daher nicht ob, sondern wie lässt sich das Potential additiv gefertigter Elektronikkomponenten und -systeme nachhaltig heben.
Wissen teilen, gemeinsam wachsen
Mit einem relativ kleinen Entwicklerteam war dieses Ziel nicht zu erreichen. Es benötigte ein breiteres Fundament, um aktuelle Problemfelder zu beheben, Schwachstellen herauszufinden und die Ergebnisse in eine sinnvolle Anwendung zu wandeln. Nano Dimension befand sich damals in einer ähnlichen Situation. Obwohl die Kunden frühzeitig positives Feedback gaben, konnten sie die neue Technologie nicht gewinnbringend einsetzen. Sie war schlicht noch nicht reif genug. Schnell wurde klar: Selbst, wenn HENSOLDT und Nano Dimension ihre Ressourcen bündeln, würde dies in absehbarer Zeit nicht ausreichen, die Hürden bei der Entwicklung 3D-gedruckter Elektronik zu überwinden und die Technologie bis zur Produktreife zu bringen.
Schwarmintelligenz nutzen
Das war die Geburtsstunde von J.A.M.E.S (Jetted Additively Manufactured Electronics Sources). Das Joint Venture basiert auf der Idee, eine Community aufzubauen, um mehr Stakeholder einzubinden und so die Weiterentwicklung der AME-Technologie gemeinschaftlich schneller voranzutreiben. Ziel war es, die Lücke zwischen der Industrie als Endanwender, die mit AME ihre Produkte fertigen, und den Druckerherstellern, die als „Process Owner“ ganzheitliche Material-, Prozess- und Serviceleistungen anbieten, zu schließen und deren Zusammenarbeit zu fördern. Auf diese Weise lassen sich Entwicklungen gezielter an die Marktanforderungen ausrichten und Entwicklungszyklen verkürzen, da Reibungsverluste minimiert werden und nicht ins „Leere“ entwickelt wird, und letztlich die Technologie schneller zur Marktreife führen. Neben Endanwendern und Process Ownern möchten wir auch den Bereich Academia für unserer Community begeistern, um ihre Studienergebnisse zu teilen und die Lehre auf AME und die damit verbundenen Chancen hin auszurichten.
Open-Source schafft Unabhängigkeit
Die Arbeit von J.A.M.E.S fokussiert sich dabei auf die Grundlagenforschung, die wir als Open-Source zur Verfügung stellen. An dieser Stelle ist es wichtig zu erwähnen, dass J.A.M.E.S neutral und prozessoffen ist. D.h. wir beschäftigen uns nicht ausschließlich damit, den Prozess von Nano Dimension zur Produktreife zu bringen, sondern wir unterstützen auch andere Druckerhersteller mit deren spezifischen Materialien. Die Community kann den aktuellen Stand der Technologie aufnehmen und in Eigenregie in ihren jeweiligen Bereichen weiterentwickeln. Themen wie Standardisierung oder IPC-Normen werden dagegen gemeinschaftlich von J.A.M.E.S und der Community getrieben. Hat ein Prozess die Marktreife erlangt, wird das Ergebnis des Crowd-Development-Ansatzes im Prozessportfolio auf unserer AME cloudbasierten Plattform veröffentlicht. Über diese Plattform, die später auch als Marktplatz fungieren soll, können Community-Mitglieder mit anderen Experten in Kontakt treten, Designs bzw. Building Blöcke hoch- und runterladen, mehr über die Einsatzmöglichkeiten von AME bspw. durch Design-Tutorials lernen oder Hilfestellung bei der Erstellung eigener Designs erhalten.
Designs absichern
Bei J.A.M.E.S nutzen wir für das Design die CST Studio Suite von Dassault Systèmes. Ich kannte die Software zur Simulation elektromagnetischer Felder bereits aus meiner Promotionszeit und hatte das große Glück, die Anwendung auch bei HENSOLDT vorzufinden. Während dieser Zeit wurde ich zum Power User. Vorteil der CST Studio Suite ist, dass sie nativ 3D-Designs unterstützt und durch die etablierte Anwendung im Elektronikbereich mit gängigen ECAD-Standardformaten kompatibel ist. Durch diese sehr einfache Integration von ECAD-Daten konnten wir unseren Designaufwand deutlich reduzieren. Ein weiteres Plus ist natürlich die Möglichkeit der Simulation. Da das 3D-Modell vollständig digital entwickelt wird, lassen sich Fehler oder Schwachstellen frühzeitig identifizieren. Auf diese Weise überprüfen wir zum Beispiel die Performanz von Druckern, indem wir Messergebnisse mit Simulationsergebnissen vergleichen. Aktuell haben wir in einem Projekt einen diskreten Filter aus Kondensatoren und Spulen aufgebaut. Diese beiden Bauteile wurden zuerst einzelnen simuliert und im Anschluss zu einem Filter verschaltet und dieser erneut simuliert. In einem anderen Projekt haben wir eine RF Synthesizer Platine in 3D entwickelt. Das Ergebnis war ein funktionaler Würfel mit dreidimensionaler Leitungsführung anstelle einer zweidimensionalen Platine – als Demonstrator zur 3D heterogenen Integration.
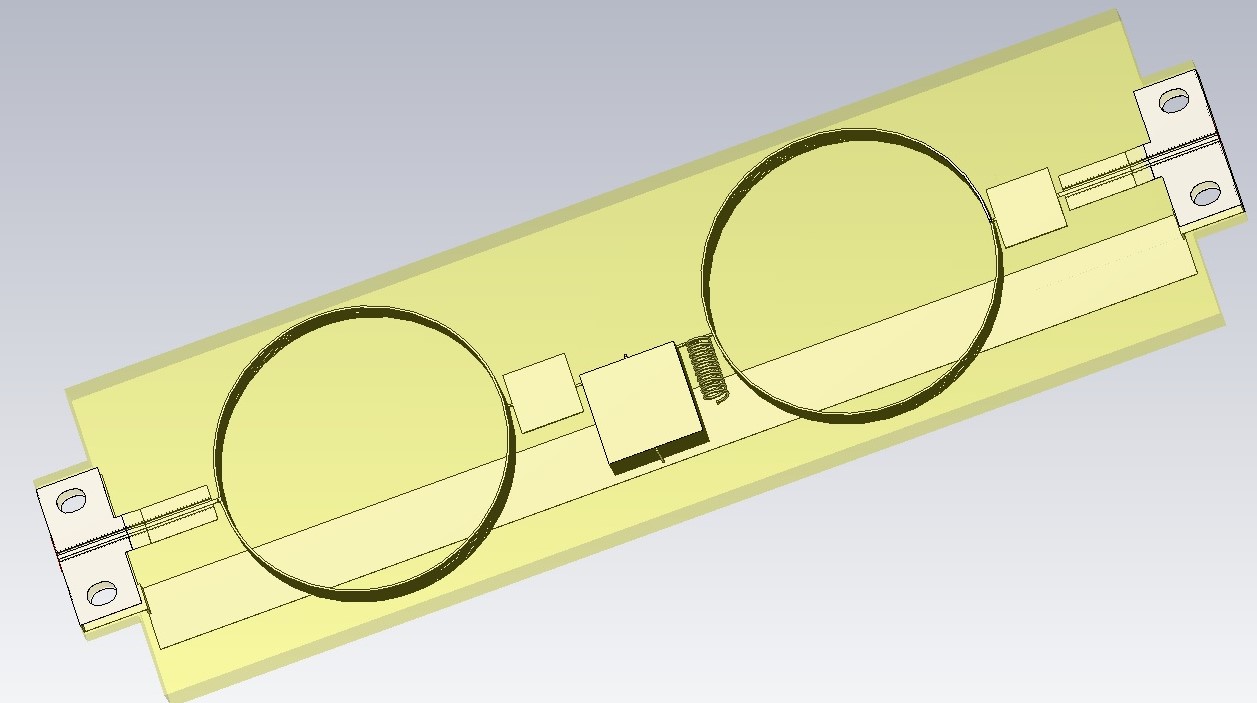
Disziplinen verschmelzen
Komplexer wird es, wenn neben den Anforderungen an die elektronische Funktionalität, auch Anforderungen an die mechanische Stabilität erfüllt werden müssen. Bspw. wenn es darum geht, einen Schaltungsträger mitsamt Gehäuse in einer einzelnen Struktur zu realisieren. Für das mechanische Design nutzen wir unter anderem die 3D-CAD-Lösung SOLIDWORKS von Dassault Systèmes. Die Datenübertragung zwischen den beiden Anwendungen erfolgt über ODB++ bzw. DXF, derzeit noch mit vielen manuellen Import/Export-Schritten. Mehr Funktionen in den ECAD- und MCAD-Tools wären daher wünschenswert, um den kompletten Design-Prozess abdecken zu können.
Neue Horizonte entdecken
Das Fehlen der nötigen Entwicklungstools, ist sicher auch der Tatsache geschuldet, dass der globale Markt für dreidimensionale Elektronik noch recht überschaubar ist. Unsere größte Herausforderung liegt daher im Aufbau der Community. Denn wir sehen J.A.M.E.S und unsere Community als einen entscheidenden Baustein, um das Wachstum des Marktes zu beschleunigen. Es gibt zwar viele Communities und Plattformen für sowohl Elektronik als auch 3D-Druck, aber die Kombination ist bis jetzt einzigartig. Das ist unsere Chance!
Geschäftsmodell monetarisieren
Sie fragen sich jetzt sicher, welches Geschäftsmodell J.A.M.E.S verfolgt. Neben dem Aufbau der Community, die erste Version der Plattform wurde im Juli 2022 gelauncht und die ersten Partner sind angebunden, werden wir im zweiten Schritt auch Consulting- und Projektmanagement-Services sowohl für die Industrie, als auch für die Druckerhersteller anbieten. Unternehmen, die unsere Plattform als Marktplatz nutzen und darüber 3D-Drucker, Designs oder Komponenten anbieten oder einkaufen möchten, werden wir zudem Marketingmöglichkeiten bieten, um ihre Sichtbarkeit zu erhöhen und Informationsmaterial für ihre Kunden bereitzustellen.
Blick nach vorne
Die AME-Technologie in die Breite zu tragen und für jedermann zugänglich zu machen. Das ist unsere Vision. Die CST Studio Suite ist dabei ein sehr wichtiges Tool, mit dem sich der Designaufwand deutlich reduzieren lässt. Ich möchte mich bei Dassault Systèmes und dem Fachhändler MB CAD bedanken, dass sie unserem Startup von Anfang an mit Rat und Tat zur Seite stehen und aktuell die Einführung der 3DEXPERIENCE Plattform bei J.A.M.E.S begleiten. Eine Zusammenarbeit, die zu neuen Innovationen führen wird.
Bildmaterial
Copyright Bilder: ©J.A.M.E.S GmbH
Autor
Dr.-Ing. Rolf Baltes
RF Design Engineer
J.A.M.E.S GmbH
Willy-Messerschmitt-Straße 3, 82024 Taufkirchen, Deutschland
E-Mail: contact@j-ames.com
Weitere Informationen
j-ames.com | Twitter | LinkedIn
Weitere interessante Referenzberichte:
- Endlich Emissionsfrei – Mit ARTHUR BUS und 3DEXPERIENCE Works auf dem Weg zum nachhaltigen Nahverkehr
- JAS GmbH: CAD-Stücklisten perfekt organisieren mit 3DEXPERIENCE
- Up in the Air – Emmisionsfreier Gondelverkehr mit der Ottobahn AG und 3DEXPERIENCE Works