How Customers are Driving and Fully Leveraging 3D Motion Creator
The latest release of 3D Motion Creator recently dropped and there’s a handful of time-saving enhancements, including some customer requests that will help you get a better feel for how your product will behave in the real world.
3D Motion Creator is a browser-based kinematic and dynamic analysis tool for complex mechanical systems that’s intuitive, highly interactive, immersive; and runs on the cloud-based 3DEXPERIENCE® platform so you can also leverage data management and collaboration capabilities.
In this blog I’ll walk you through what’s new in the R2023x FD03 update, provide some examples of how customers are using the latest features, and show how you too can get the most out of 3D Motion Creator.
For starters, you can speed up model creation by automatically creating markers from axis systems and use sketches to define function values. Let’s have a look at these new enhancements and more below.
- Get Immediate Feedback with Animations While Creating Joints – get a better understanding of joint definitions.
When creating motion joints, you can see the animation of how the parts come together. You can continue to use SOLIDWORKS® mates to define all the joints for motion, but in cases where you need better control for specifying a joint in a specific location or orientation, you can still define motion joints which will show you an animation on how exactly it will be positioned, based on your geometry or marker selections.
This enhancement helps you understand the impacts of your joint definitions so you can identify modeling errors when creating joints.
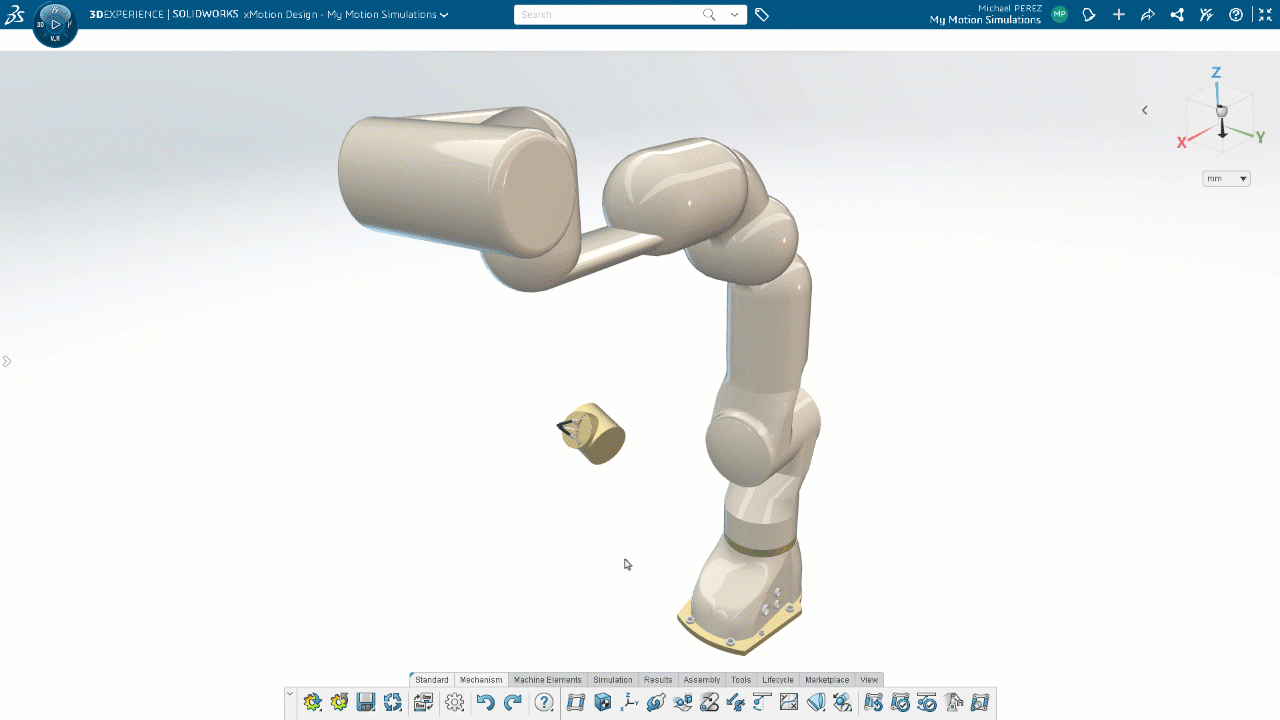
- Set Up Function Definitions from 2D Sketches – define function values more easily.
The latest release features a new “From Sketch” option, which enables you to use a sketch to define a function. This is a nice tool when you have a particular function in mind, but you don’t know how to mathematically create it. So instead of using data points or a spreadsheet for the function input you can use a sketch that’s been created in the SOLIDWORKS 3D Creator role or CATIA Mechanical Designer role as an input.
Simply select the sketch from the pull-down menu in the Function dialog box under Type, and it will automatically generate the function that corresponds to the sketch.
The function selected will be used to set up the driver for the simulation.
This new functionality was driven by customer Webasto, one of the world’s top automotive suppliers, who uses CATIA and 3D Motion Creator. For example, they use sketches to explore how the various drivers on a sunroof mechanism in a convertible should work and what distances the various actuators should move.
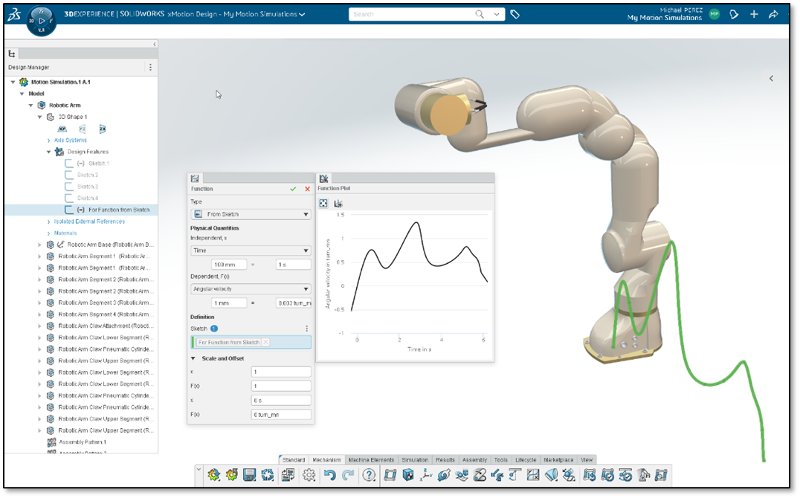
- Generate Markers from Axis Systems in One Click – create markers on the fly.
When you need a joint to be defined at a particular location, a marker can be used to define the right joint location. Axis systems are used to define the joint location and orientation for any product. Axis systems can be converted to markers in the motion mechanism, which can be used downstream in the mechanism to define various motion elements like joints, spring end locations, and the applied load application point.
In 3D Motion Creator you can now generate a marker for multiple components at once. Simply select all the bodies on your model and use the Generate Markers command to create your markers in just one click instead of doing one by one.
This functionality was requested by automotive customers, who for example, deal with complex suspension systems that have a lot of connection points that define the joints. Most of the connection points are defined using axis systems at the right location and orientation. These axis systems are used to define motion joints.
In addition, many customers use the skeleton approach to define mechanisms. Many of their mechanisms are defined using lines and points using an axis system to create the mechanism layout. Once this is finalized, separate 3D geometry is built on top of the skeleton mechanism and then motion combines both these effects.
The big advantage of this approach is that the motion mechanism that uses the skeleton is not disturbed when building the 3D model. You do not have to worry about geometry issues, such as mates breaking when you change or update the geometry.
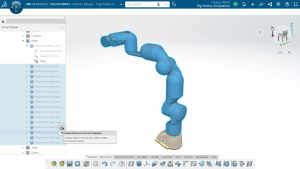
- Import a File to Define Function Data – take advantage of flexible ways to add data and avoid errors.
In the last update we introduced the ability to copy and paste data from external programs like Excel into the Function Definition table that could be used to define functions with data points. Now it’s even easier with the ability to import an Excel file directly into the table to define the functions. This saves time and helps you avoid copy and paste errors when setting up functions by data points.
This is especially useful when you have large amounts of data coming from external tests.
Also, here’s a tip. The first row in the file can be used to define the units of the file. If no units are defined it imports the file in SI units.
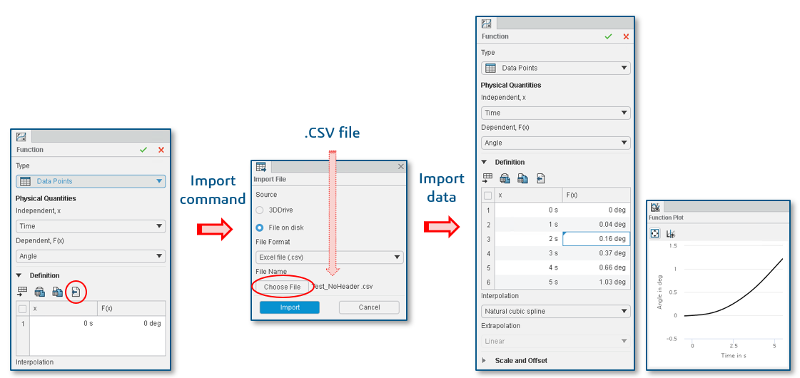
- Mechanism Status Information – see how various changes will affect your mechanism.
You can check your degree of freedom with the new Mechanism State status menu at any time. For example, you can check it after making various modifications to your mechanism to see how it will be affected and to check for redundancies. Redundancies will help you understand why loads are not computed properly in certain motion drivers and joints.
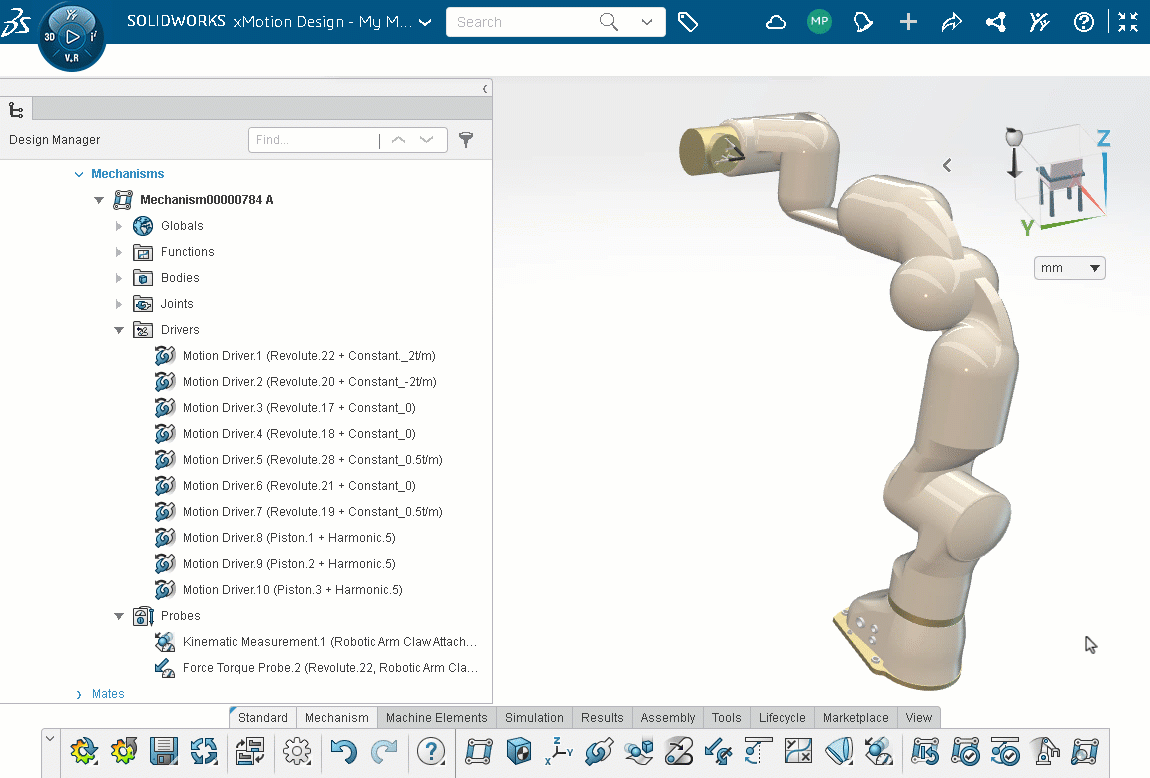
That about sums it up for this round. See my last blog for more updates.
Contact your reseller for a full demo of what’s new. If you haven’t got your hands on it yet, 3D Motion Creator is available now in the 3DEXPERIENCE Works portfolio!