Learn How to Minimize Design Planning and Increase Flexibility
The world is full of distractions—so many things competing for our attention from so many sources. The biggest challenges when facing these distractions are the design tasks that you don’t like or don’t add value. When you are faced with these unpleasant tasks, it is so easy to check social media or get coffee or if you really want to lose a few hours, check your inbox!
For me, design planning was one of those tasks. As a designer, I just want to jump in and design; this allows me to avoid spending time upfront thinking about the best way to structure my assemblies. It also means that I have even more work to do to fix things down the road.
Make Design Planning Less Cumbersome
Then along came the 3DEXPERIENCE® platform and the SOLIDWORKS® Design Roles. The first app, xDesign, available in the 3D Creator Role, touted something called a single modeling environment. No parts, assemblies, and sub-assemblies to worry about anymore. Everything starts as a “physical product” that can be a part or an assembly. You can create sketches and then turn those into 3D features—or jump straight to 3D with the Parametric Primitives.
You can also bring other physical products into the single modeling environment and mate them into place, just as you would expect in an assembly environment.
On top of that, you can form new sub-assemblies, and if you change your mind, you can dissolve them. What about those features and sketches, I hear you say! Well, they can be selected and turned into their own physical product. Better still, you can dissolve a part back into a series of features.
The Power of Dissolve
In a single modeling environment, you can “dissolve” multiple parts into one part. Or go from one part back to multiple parts. Dissolve essentially breaks a component down into its feature level and removes the selected physical product, moving all features and/or components into the parent component. And Dissolve allows complete restructuring/regrouping of assemblies with no loss of fidelity.
Dissolving a component back down to features is a great way of reusing features and sketches from other physical products. You can use anything you have designed before as a library and bring them in at any point, dissolve it down to features, and reposition or resize the features as you wish, with the added benefit that the original is still safe and secure on the 3DEXPERIENCE platform in the cloud.
This is a lifesaver when deciding if it is best to use a multi-body modeling approach—and then later realize that you really should have created items as separate parts. Either way, you can form components from features, form sub-assemblies from two or more components, and then more sub-assembly levels. If you get any of it wrong, you can simply dissolve the sub-assembly and even dissolve a component back down to features.
Real-world Example 1
Consider a die-cast component. Fairly complex but has very distinct sections to it. If the volume is low, it may well be more cost-effective to machine components and weld or bolt them together instead. Suppose you wanted separate part numbers for each of the machined components with the single modeling environment. In that case, you can simply select the features which make up the component in the design manager (tree) and make it a component. Then only design changes are needed to make it more suitable for the new manufacturing process—no need to start again or do clever things with inserted parts or references as a workaround.
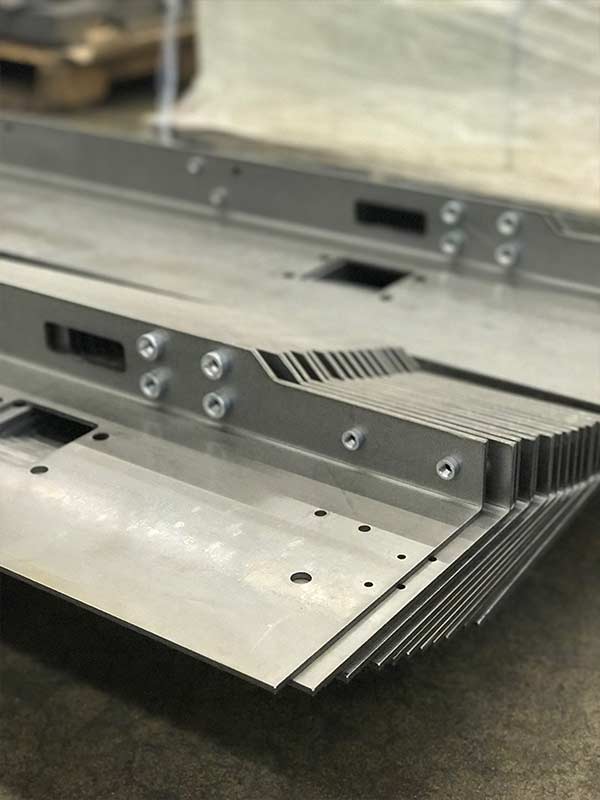
Real-world Example 2
Installing press-fit fasteners, nuts, and studs into sheet metal is a common way to design a sheet metal component. Often, a designer later realizes that inserts need to be added. (The inserts are almost always overlooked at the beginning.) With a single modeling environment, you can simply give the part a name and rename the top level to “assembly.” Then add your fasteners. At the new assembly level, the sheet meet assembly is inseparable. See the screen captures below.
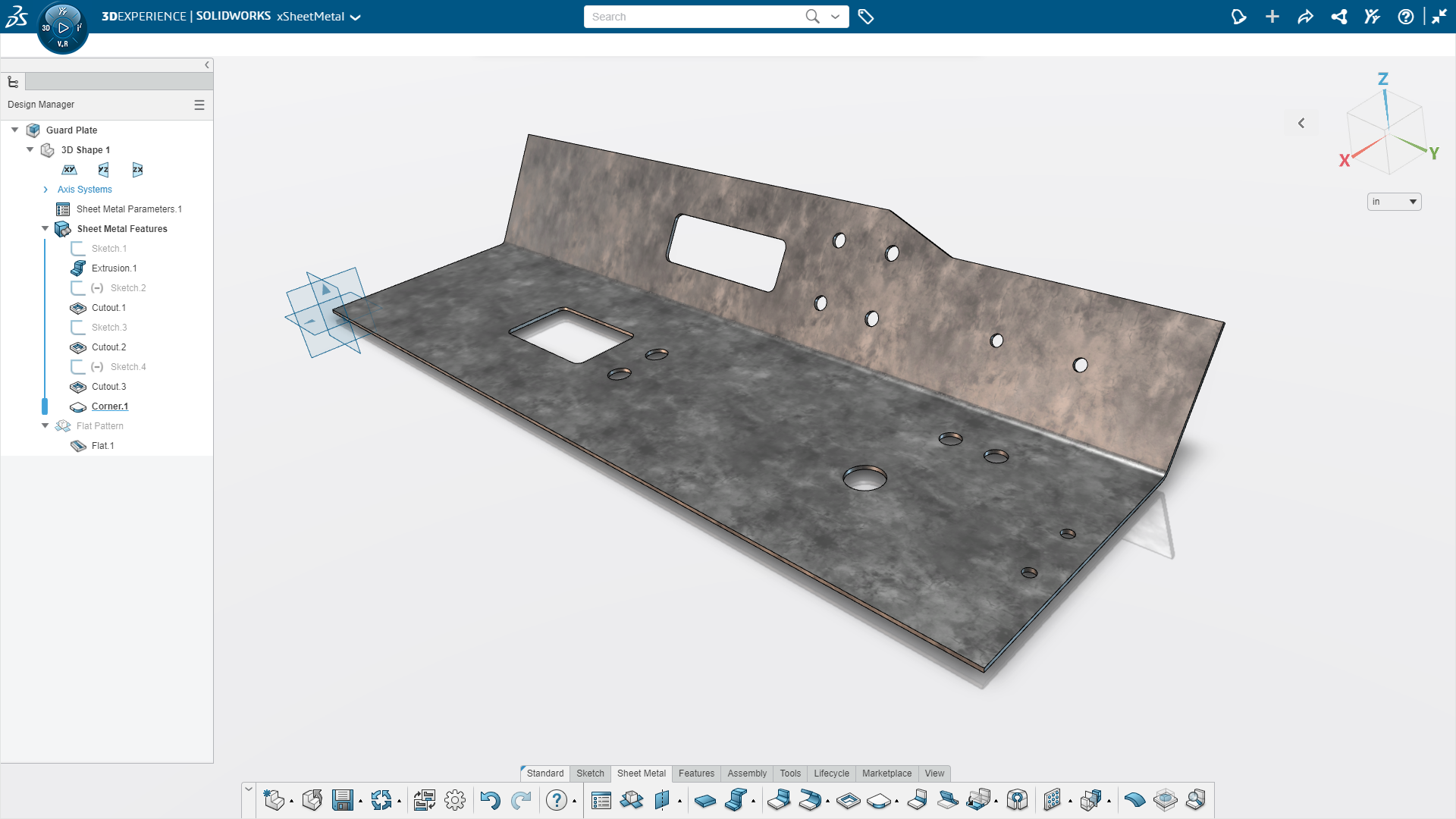
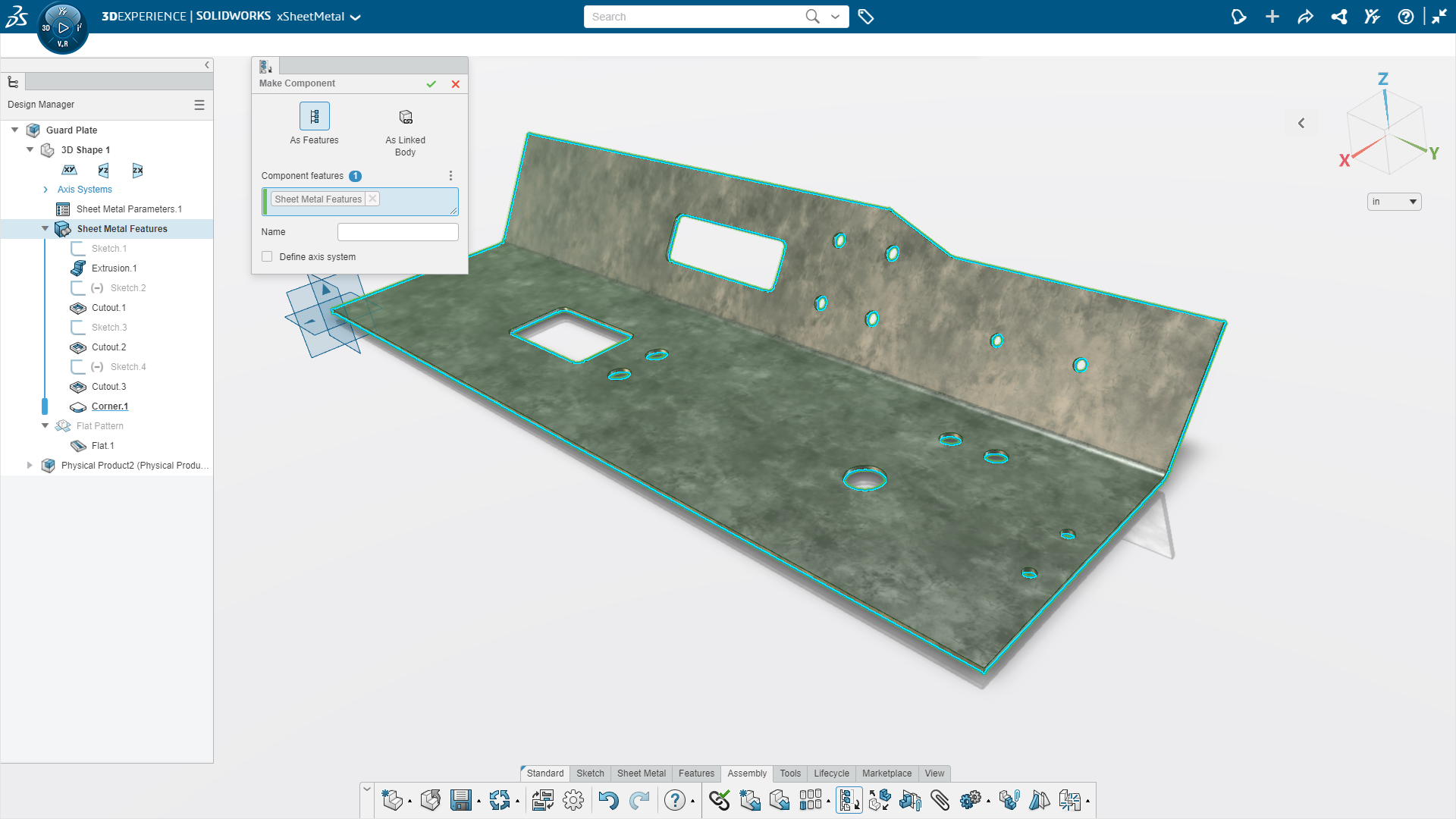
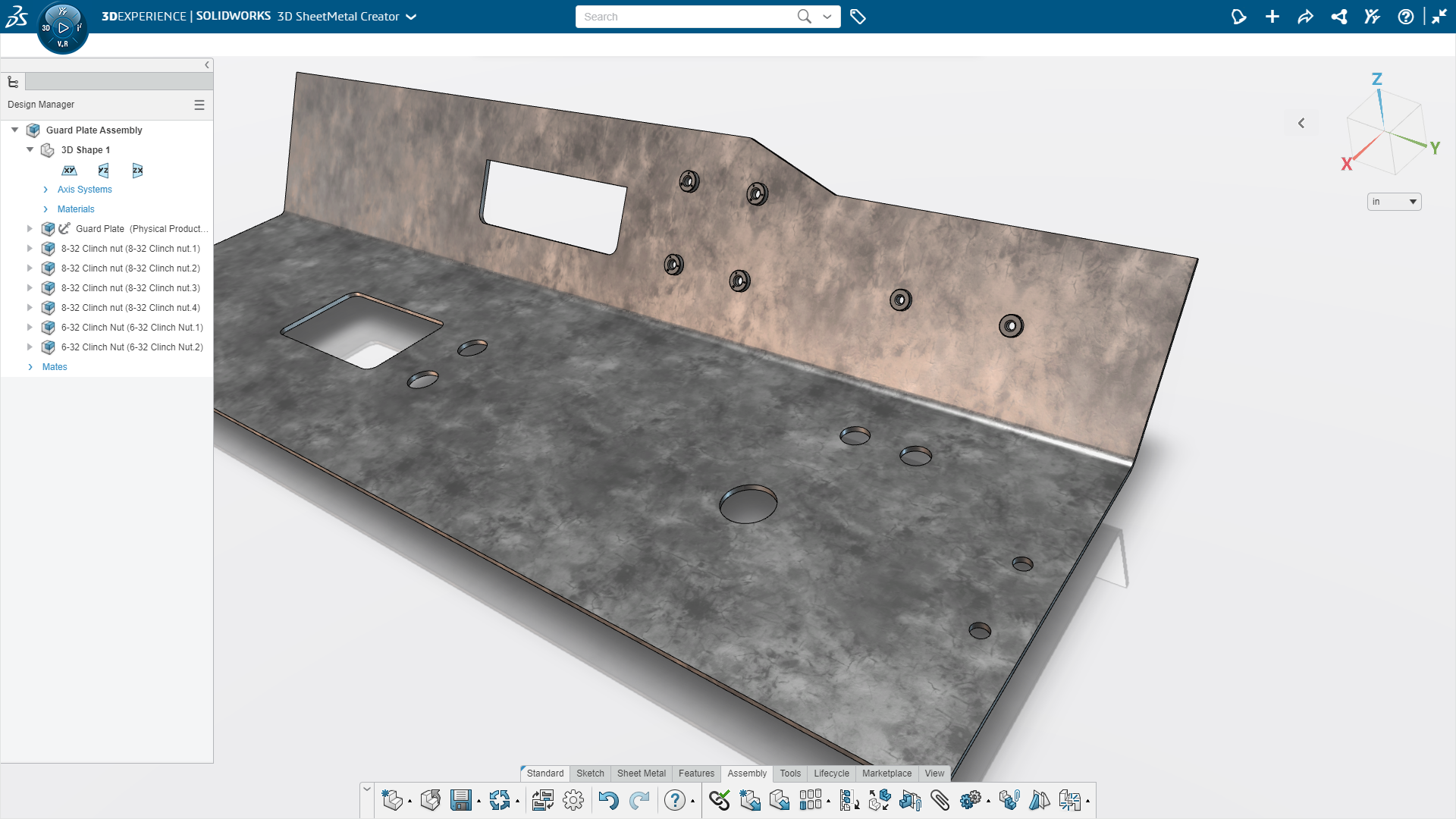
One Place for All
Increased flexibility is one of the hallmarks of the single modeling environment. The software’s design tree enables designers to use sketches, primitives, features, bodies, components, or any combination of these—in 2D or 3D—with all tools, commands, and functionality available from a single, intuitive workspace. Starting design concepts with 2D sketches or primitives gives designers an easy path to quickly generate 3D components.
Plus, all your apps and files are managed on the 3DEXPERIENCE platform in the cloud. Having everything in one place simplifies the use of the tools and associated projects. Communicating with key stakeholders is more manageable since everyone works from the same environment, which all stakeholders can securely access with an internet connection and a web browser.
If you have more questions about the 3DEXPERIENCE design and engineering apps and how they interact with SOLIDWORKS, contact your local reseller.