Drag-and-Drop Ordering Tool Powered by SOLIDWORKS Sell
“How to speed up the ordering process, reduce errors and grow our business?”
Meljac, a high-end electric switch manufacturer in Europe was challenged, facing several major obstacles:
- Due to a large number of complex business rules, distributors were taking mistaken orders that didn’t fit in the switch back enclosure or weren’t even manufacturable.
- As a result, the engineering team had to design Change Orders (CO) and revalidate with customers repeatedly.
- With over 10,000 SKUs, the manufacturer cannot present the full range of products efficiently and effectively.
- Most importantly, the business growth was hampered due to the slow and error-prone ordering process, in spite of four full-time employees assigned to order management already.
Powered by SOLIDWORKS Sell, a reseller developed an online ordering tool for tablet and PC screens as shown in Figure 1. The project was completed in one month using SOLIDWORKS Sell and its APIs. To the manufacturer, it was magic because other contractors quoted at least eight months previously.
Here is a simplified version of the tool to illustrate the workflow. The full-scale system is not revealed publicly to protect Meljac’s intellectual property.
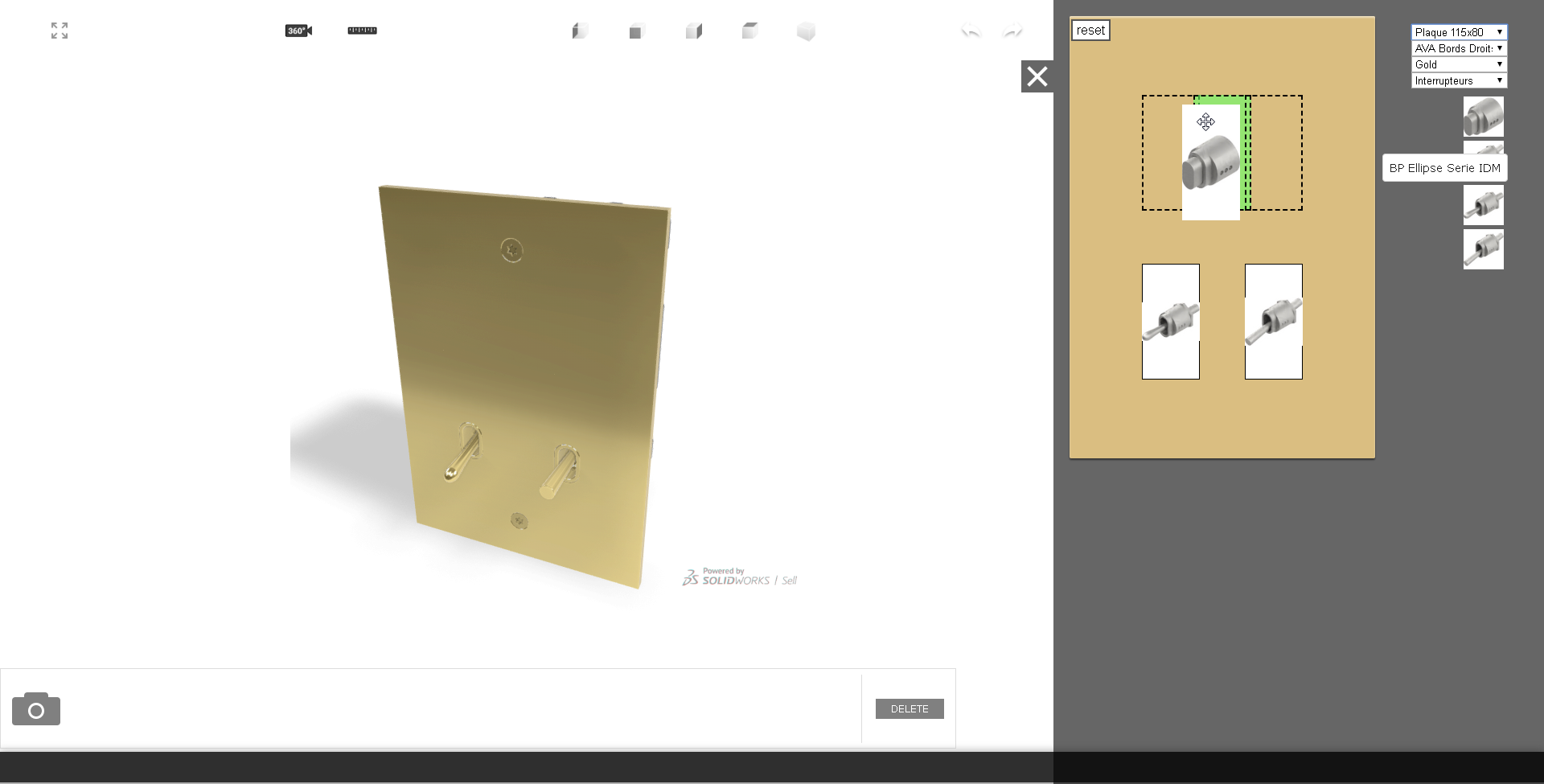
Please expand the panel on the right. Then from the drop-down menus, you can select the plate sizes, trims, materials, and various eligible components. The 3D models update accordingly as you make selections.
Then you can simply drag and drop component icons to the yellow plate simulator. During the drag and drop, the available spots are displayed in dash lines dynamically on the plate. If a valid spot is being approached, then it is colored in green as shown in Figure 1 ready for the drop. If invalid spots are covered, they are colored in red as shown in Figure 2 below.
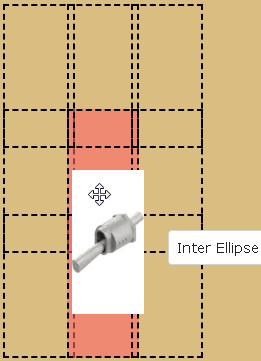
This way, the complex business and design rules are enforced automatically and intuitively to prevent mistaken orders. For example, once a middle spot is taken, the two spots on neither side would allow any other components since no dash lines are presenting as shown in Figure 3. The drop is aborted automatically.
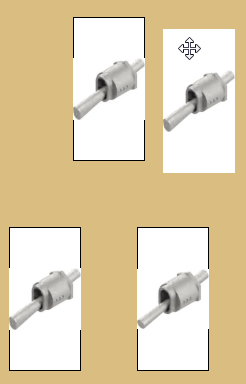
Once the drag and drop is done, the 3D model updates instantly to show the latest configuration. You can also make material choices on a specific component, such as the top button as shown in Figure 4.
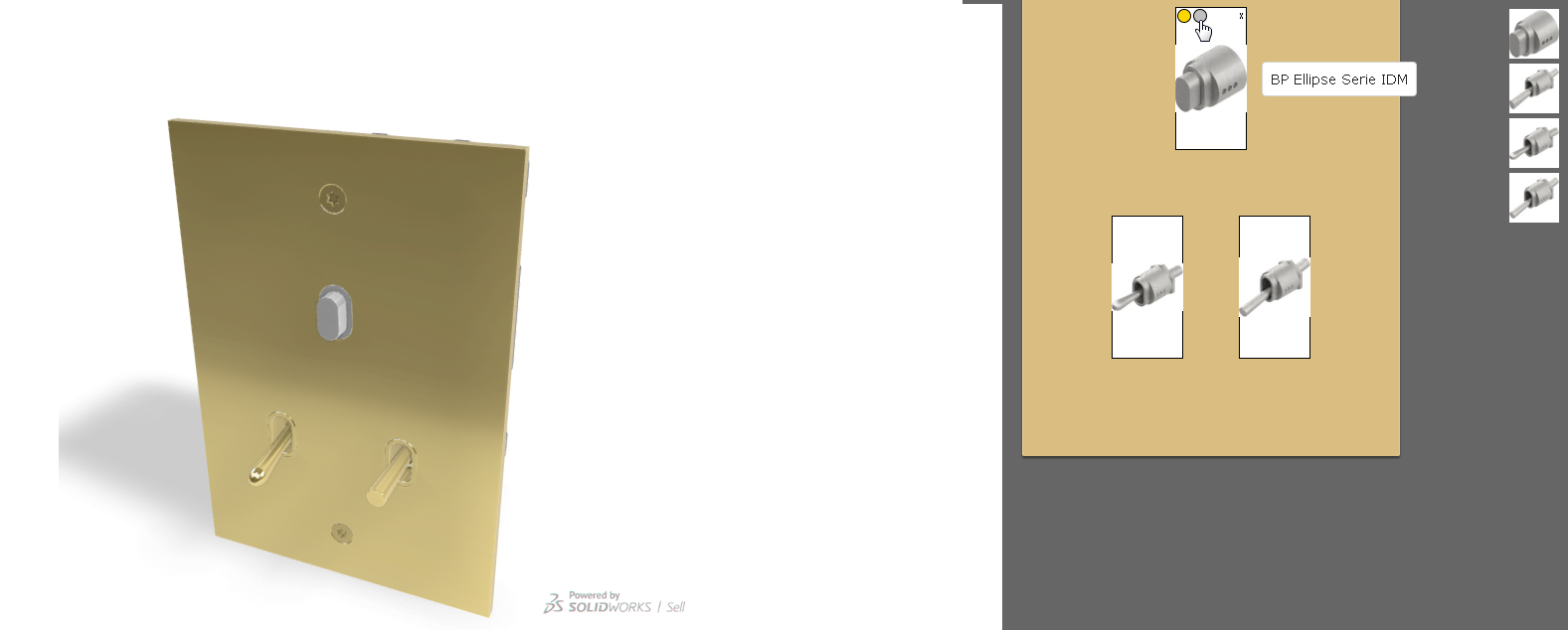
To remove components from a plate, simply click the cross button on each tile or hit the Reset button on the plate simulator as shown in Figure 5.
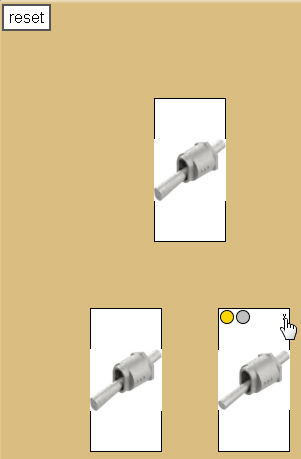
Now the ordering process is much more efficient, accurate and engaging to fuel the business growth. To me, it almost feels like a fun toy, yet it is so practical and productive. This is the power of SOLIDWORKS Sell.
Hope you find it fun. Want a demo for your team? No problem. Just fill out the request form so that we can connect with you.
To know more about SOLIDWORKS Sell, go here or watch this video below to learn the basics of how you can use SOLIDWORKS Sell to enable your customers to personalize products, while keeping the emotional attachment to your brand.