Additive Manufacturing, 3D Printing and Subtractive Manufacturing: What’s the Difference?
This year at SOLIDWORKS World we don’t just have over 200 break-out sessions for you to gain additional insight into design automation, electrical design, simulation or PDM. This year for the first time, we are offering four specially tailored Learning Paths, each with a mini-general session to kick things off, followed by six certified sessions and finishing with a panel discussion. Attend four out of the six sessions for a given path, and you will qualify for a special MySolidWorks Certificate. There will be specific learning paths for the Internet of Things (IoT), Model Based Definition (MBD) and two for Manufacturing – Subtractive and Additive. Not sure what the difference is? Read on…
One thing I have been asked many times when I tell people what I have been working on at SOLIDWORKS is what the meanings of these relatively new terms are. Let’s start with the easiest to differentiate: Additive versus Subtractive.
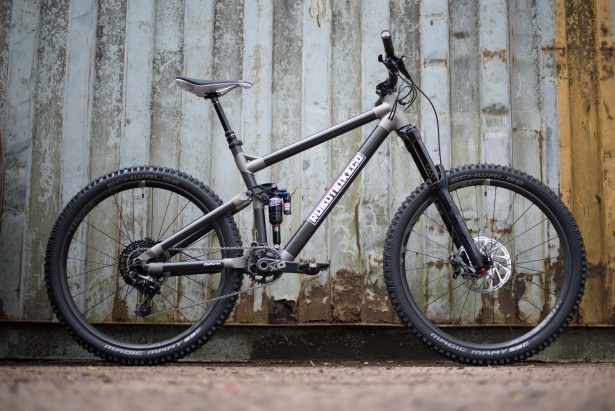
Additive manufacturing (AM) is a relatively new catchall term for the latest techniques for making things, starting with nothing, building up material layer by layer directly from 3D data. It is an industry standard term (ASTM F2792 and ISO TC261) for all techniques that use this process.
There are six or seven types of AM techniques, all of which are quite different but in most cases achieve what was impossible to produce using traditional methods. The reason they can achieve what was previously impossible is they build up parts/component/products/things a layer at a time. Each layer is joined to the last by way of a binder, melting or curing. This offers significant freedoms of the geometry that can be produced as there is no other material in the way. So what are the types of additive manufacturing?
- Material Extrusion – commonly known as FDM or Fused Deposition Modelling pioneered by Stratasys. This takes a filament of material and pulls it through a heated nozzle to the point of melting and is deposited where it is needed. Common analogies are a glue gun or icing a cake. Mmmm…cake.
- Binder Jetting – this is the technology where the term 3D printing came from since it uses inkjet printer heads that selectively bind powder together. Again, one layer at a time with another layer of powder being spread across the top each time. Any powder not touched by the binder is shook, blown or brushed off the finished part.
- Material Jetting – again also uses inkjet technology but this time using material to selectively deposit where needed.
- Powder bed fusion – This is exactly the same as binder jetting, except for instead of a binder to fuse the powder granules together, a laser or electron beam melts them together.
- Directed Energy Deposition – this is similar to FDM but using a metal wire instead of a polymer filament, but can also use a powder fired into place. The powder or wire is then melted and welded onto the previous layer or surface by an electron beam or laser.
- Vat photo-polymerization – as the name suggests starts with a vat or tank or photopolymer (liquid resin that hardens when exposed to a light source). The top layer of liquid is then cured via a light source (DLP) or laser (SLA) and then moves up out of the liquid, or down into the liquid (dependent on the type of machine) for the next layer to be processed.
- Sheet Lamination – This process is the reason why I said at the start “six or seven” types of additive manufacturing processes. I will come back to this one since, I think this is technically subtractive.
With subtractive manufacturing, you start with a block or billet of material bigger than the part you want to make and cut away the block (sometimes layer by layer) until you have the desired shape. This is achieved by milling, drilling or turning, for example. So back to sheet lamination…
Sheet Lamination – This one is, strictly speaking, subtractive but since it builds layer by layer it sometimes slips in as an additive process. It works by having a sheet of paper or plastic (or could be any sheet material in theory which is cut by a laser or scalpel into shape and the next sheet layer is cut to size and shape and stuck down on top of it.
We have established subtractive is very easy to define, while additive is slightly more complex due to the number of different processes but a relatively straightforward concept.
What about 3D printing then? Well, the term is often used interchangeably with additive manufacturing and as mentioned earlier, it comes from binder jetting using 2D printing technology. However, unlike Fused Deposition Modelling (FDM), which was trademarked by Stratasys, the term 3D printing was never protected. Many experts in the field have tried to differentiate 3D Printing from Additive Manufacturing by applying their own definitions. For instance, I have heard people say that 3D printing relates to a one-off item manufactured using an additive process whereas Additive Manufacturing leans more towards items produced as a series production method.
For me though, 3D printing is much easier and quicker to say and when you have to say it and write it and type it as often as I do, 3DP or AM will be just fine!