How SOLIDWORKS has changed lives with 3D medical design
In 1975, freshly graduated from university, Dr. Kenneth Woodhead began work as a restorative dental surgeon, setting up his own practice in the United Kingdom.
Dr. Woodhead now has over 40 years of cosmetic and restorative dental experience – working in both private and public service in the UK, New Zealand and Australia. He spoke exclusively to Dassault Systemes about how CAD technology such as SOLIDWORKS revolutionised the dental industry.
In the next decade, engineers will be able to design the best thing possible and then hand it to robots to… https://t.co/t0VrmEi5yr
— SOLIDWORKS Asia Pac (@SolidWorksAPAC) July 22, 2016
“In 1975, CAD in dentistry didn’t exist. Crowns in particular; you took an impression of the mouth and sent it to a laboratory, they poured the impression and cast a model,” he said.
“They had to make a wax dummy, then cast it if the crown was gold or build it up in porcelain powder and fire it in a furnace. If it was a rush job, it might be done in a week; conventionally, it would take a fortnight.”
“CAD revolutionised the dental industry from every perspective: operator, technician and patient.”
SOLIDWORKS designing medical breakthroughs in record time
Once CAD technology was introduced to the process, the transformation was immediate. It became possible to complete crown and ceramic work while the patient waited, and the level of human error was vastly reduced.
“You would simply prep the tooth, removing the desired thickness – between 1 and 3 millimetres depending if it was for anterior or posterior crowns – then use CAD to assess the prepared tooth surface and within half an hour, a machine could mill a ceramic restoration from a single ceramic ingot. It revolutionised the dental industry from every perspective: operator, technician and patient,” Dr. Woodhead told Dassault.
When speaking to Alex Kok, territory technical manager, ANZ, it became clear that the versatility and power SOLIDWORKS offers the medical industry is phenomenal.
“I worked on a project a couple of years ago where a company had to deliver an implant to someone – the victim of a bad accident – a portion of their jaw had to be filled in. What they did, they performed a CT scan of what bone was left and used SOLIDWORKS to design the missing part – the implant for the jaw,” he explained.
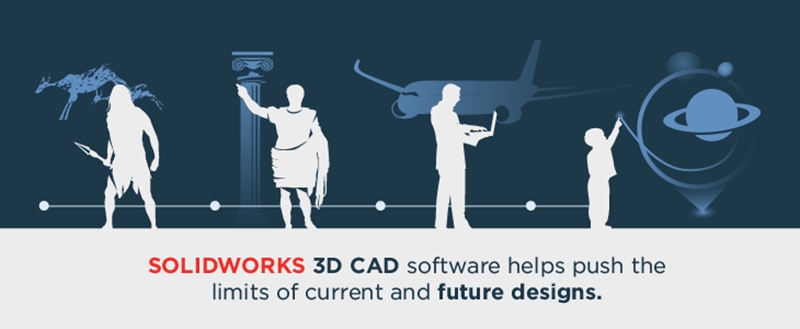
“The benefits; you’re saving time, saving money and implanting something perfectly designed and structured. When you can scan the information, you know it will fit perfectly. You can take data from other machines and push it into SOLIDWORKS.”
CAD showcasing great medical device design
“A powerful product isn’t always difficult to use, and technology has made SOLIDWORKS very accessible.”
SOLIDWORKS provides an exceptionally powerful platform for medical applications, with the software available to designers at any level.
“While there is a benefit to having relevant education that complements the capabilities of the software, gone are the days where a powerful CAD product has to be difficult to use. CAD software such as SOLIDWORKS, in tandem with ever-progressing hardware technology, have made it very accessible to anybody, ” Alex said.
When SOLIDWORKS models utilise the full potential of CAD software, the only limitation of future designs will be the user’s imagination. Thanks to SOLIDWORKS, however, the world can rest assured that the future of dentistry and medicine is in very safe hands.
SOLIDWORKS 3D CAD can help design life-changing prosthetics.
To learn more about SOLIDWORKS and the CAD process, reach out to Dassault Systemes today.