SOLIDWORKS is Helping Build the World’s Fastest Steam Locomotive: Part 2
This blog post continues the journey of a group of dedicated train enthusiasts who make up the Pennsylvania Railroad (PRR) T1 Steam Locomotive Trust as they embark on a mission to build the world’s fastest steam locomotive with a little help from SOLIDWORKS. If you missed Part 1, you can catch up here.
The Search for a Foundry Begins
Finding a foundry capable and willing to take on such a large complicated part was a challenge in and of itself. When starting the process, the PRR T1 Trust wanted to stay close to Pennsylvania for casting the first components, but also wanted to include several highly qualified foundries outside of the region. A Request for Proposal was created which included the material specifications and SOLIDWORKS model as well as quality control requirements. With the help of the group’s membership more than 60 foundries were located and requests submitted. Several foundries responded with quotes and the PRR T1 Trust began the selection process.
When selecting a foundry, items such as capabilities, time frame for task completion, number of years in business, price and customer satisfaction were all considered. As the process to find a foundry moved forward, Beaver Valley Alloy Foundry in Monaca, PA, became the front-runner. It had been in business nearly 100 years and was more than capable at pouring the large and intricate driver castings. Beaver Valley was very interested in the 5550 project and we quickly saw it was going to be the right partner.
The foundry selection process took nearly four months to complete and the Trust was very thorough and particular. The principals at the Trust felt that they had only one chance to do it right. Many people have donated money to the 5550 project, and choosing the best foundry possible was just one more opportunity for the Trust to demonstrate its ability to be a good steward of the funds given for the T1.
The next step in the driver casting process involved the creation of a wooden pattern. Liberty Pattern in Youngstown, OH, was selected by Beaver Valley Alloy to make the pattern. Liberty Pattern has been making wood patterns for the foundry industry since 1917, they have seen it all.
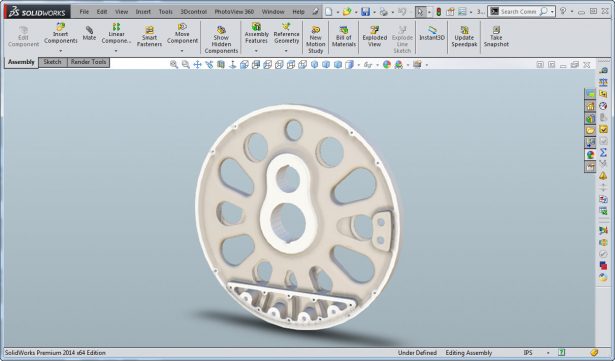
The team at Liberty pattern studied the SOLIDWORKS model of the #4 wheel set provided by the Trust (image above). It is well worth mentioning that the pattern shop’s owner stated that the Trust’s SOLIDWORKS model was some of the best work of this type that he had ever seen. Liberty Pattern then went about converting the Trust’s 3D SOLIDWORKS model into a casting pattern. It was decided to make the counter weight as a dry-fit so that ¾ of the pattern could be used for all eight drivers. This will save a tremendous amount of money in the future. The first pattern being made can be used for four of the T1’s wheels. Then, with a new section fit into place, the same pattern can be used again for the remaining four wheels.
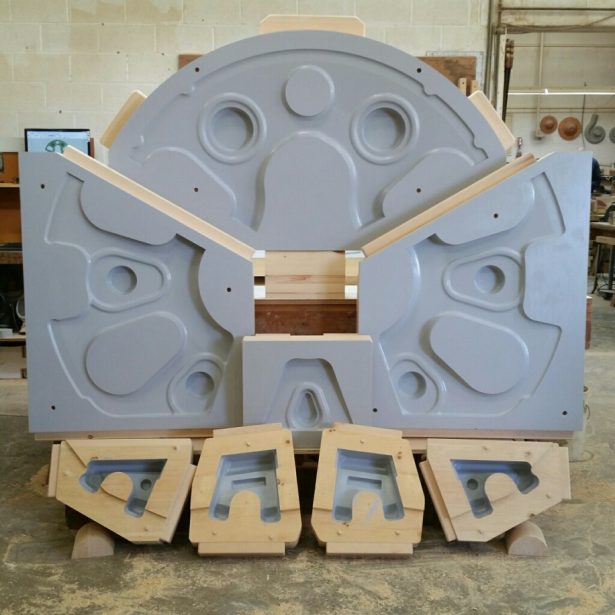
Liberty Pattern was able to use the Trust’s SOLIDWORKS model to design core boxes (shown above) that were used to form the sand cores that preserve the internal cavities of the cast wheel. This is a very complicated and precise art. Once all the cope (outside surface of wheel), drag (inside surface of wheel) and core boxes (inside cavities) were complete, they were mounted on large 96 x 96-inch boards and sent to the foundry to start the casting process.
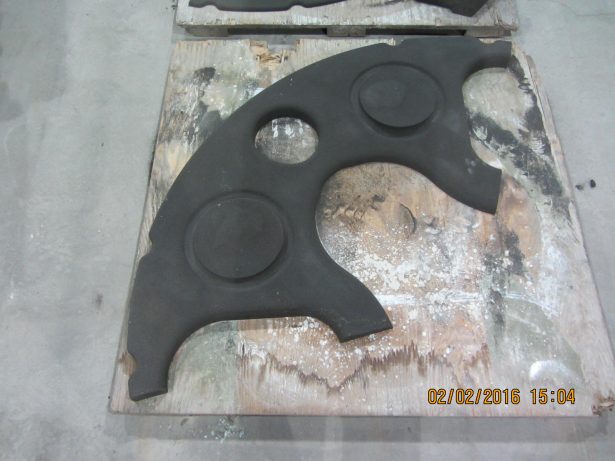
The steel wheel center casting weighs nearly 2,500 pounds and measures 6 feet in diameter. The application of the four-inch thick steel tire brings the total wheel diameter to 80 inches.
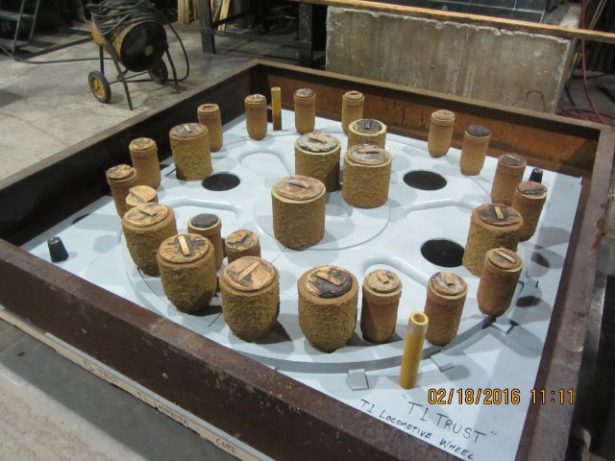
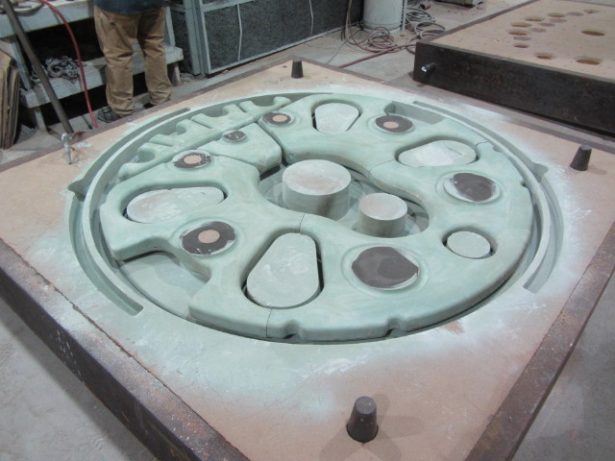
Fashioned using General Steel Castings’ Nickel Steel, the Boxpok drivers were really the “magic carpet” of their day. Through old-fashioned detective work, the PRR T1 Trust was able to identify the chemical and material properties for General Steel Castings’ Nickel Streel. However the exact heat treating process remained a trade secret and a mystery, until now. Working with Beaver Valley Alloy and a national materials testing laboratory, The PRR T1 Trust was able to use 21st Century technology to successfully replicate General Steel Castings’ Nickel Steel. In bringing back this extinct class of steel, and using the steel to cast the Boxpok driver, the Trust is now closer to its ultimate goal, a fully operational T1 locomotive.
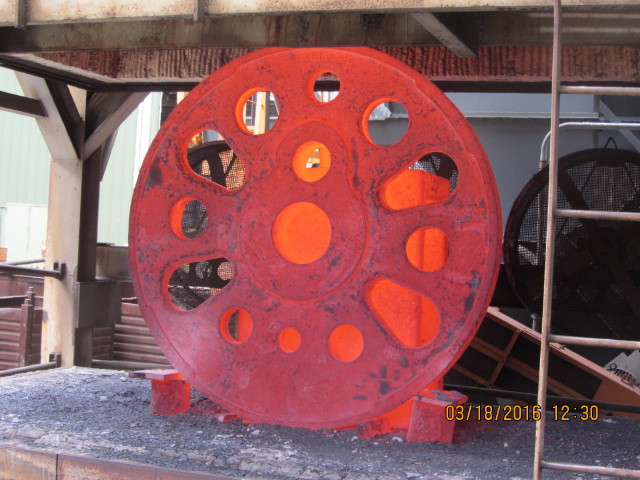
Over the next few years, engineering work will continue and simulation testing will be conducted. More components will be built, and the PRR T1 Trust will proceed with its fundraising efforts. It will be through the support of volunteers, railfan donors, foundations, grant makers, corporate donations, and legacy giving that PRR T1 5550 will ultimately come to life in steam.
Opportunities to donate to the cause can be found in the Fundraising portion of the Trust’s website. These opportunities include Driver Sponsorship, and the sponsorship of other parts, archival drawing sponsorship, regular monthly giving, one-time donations, and membership in the exclusive PRR T1 Trust Founders Club.
For further information about TheT1 Trust and PRR T1 5550, please visit the Trust’s website. There you’ll find the latest news about the group’s progress and a Frequently Asked Questions section. To keep supporters up-to-date, The T1 Trust offers an e-newsletter, the “T1 Trail Blazer,” click here for a free subscription. The T1 Trust also maintains an active and entertaining Facebook page. If you would like to contact The T1 Trust, please send an email to info@t1trust.com. All aboard!