Origin’s CheckMate for SOLIDWORKS Embraces the Model-Based Enterprise
The evolution of the Model-Based Enterprise (MBE) has gone beyond the concept stage and is being implemented by many companies in the aerospace and automotive industries as well as others. The advantages of doing so are many, not the least of which is the time savings of eliminating 2D drawings and the positive effect of improved collaboration among the many stakeholders involved in bringing a product to the market.
With SOLIDWORKS 3D Model-Based Definition (MBD), the Product Manufacturing Information (PMI) is embedded directly into the solid model as annotations for GD&T along with other relevant specifications to formalize the design intent. This creates a digital thread of all the necessary information to manufacture and manage the product throughout the product life cycle.
Origin’s CheckMate for SOLIDWORKS suite of dimensional metrology software continues that digital thread with applications geared to inspection and manufacturing engineering disciplines, re-using and repurposing the data within models and ensuring traceability of process information to the design intent.
Coordinate Measuring Machine Programming
Coordinate Measuring Machines (CMMs) are still the workhorse of most metrology labs when it comes to inspecting parts of high precision. However, the programming process can be time-consuming and interpretation of GD&T contained in 2D prints can be error-prone.
CheckMate for SOLIDWORKS automatically extracts the GD&T from the annotated model as well as feature information from the geometry to automate the CMM programming process. A time savings of as much as 85 percent can be achieved, and interpretation errors from using 2D drawings are eliminated.
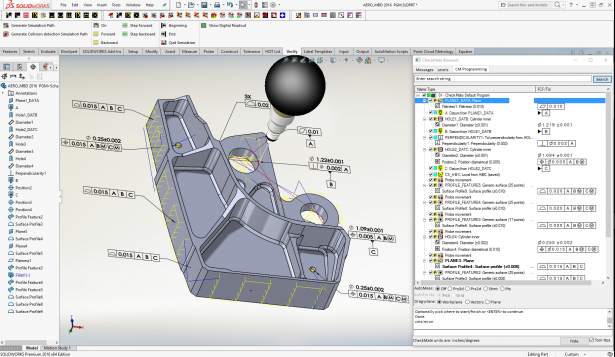
Laser Scanning/Soft Gauging
With enhancements in the technology, the use of Laser Scanning equipment in the dimensional metrology field has become much more prevalent. Color deviation maps provide an instantaneous picture of potential problem areas and non compliancy, but that is often not enough to meet stringent inspection requirements or provide the detailed information to evaluate any corrective action, if needed.
With CheckMate for SOLIDWORKS, a soft gauge is generated from the MBD in the model and used to extract substitute features from the point cloud. In this example, the point cloud was automatically aligned to the solid model and the detailed inspection report generated. The measurement results in the report reconcile the manufactured part to the design intent.
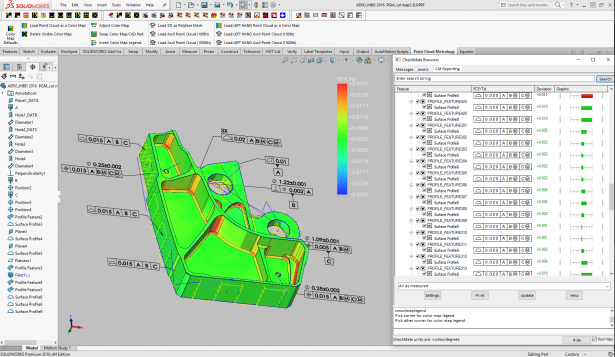
The evolution of the Model-Based Enterprise as characterized by how companies convey product design intent throughout their own company and to their supplier and customer base will bring significant advantages over the processes they now have in place. The end result: better products, shorter time to market and at a reduced cost. Model-Based Definition as implemented by SOLIDWORKS is the first step in this evolution, incorporating the design intent in the 3D solid model forming the digital thread on which applications of multi-disciplines re-use and re-purpose that data.
The integration of SOLIDWORKS MBD in CheckMate for SOLIDWORKS is a prime example of how Origin has moved the product manufacturing information in the model into the inspection and manufacturing engineering environment to further enhance the Model-Based Enterprise for SOLIDWORKS users.