Take High-Tech Products from Design to Manufacturing Faster with SOLIDWORKS
You probably already know that SOLIDWORKS is the industry leader for 3D CAD. But what you may not know is that SOLIDWORKS is much more than just CAD. It’s a full suite of best in class productivity tools that allow you to take your high tech products from concept to manufacturing faster and cheaper than ever before.
For example, did you know that SOLIDWORKS Industrial Designer (SWID) is a design tool that allows you to quickly generate new product concepts in 3D? This enables users to rapidly apply free flowing design ideas before investing in detailed designs with SOLIDWORKS 3D CAD (see Fig. 1 below). Since SOLIDWORKS Industrial Designer is on our 3D EXPERIENCE platform, it allows real time collaboration and feedback from stakeholders which allow users to develop innovative products more quickly.
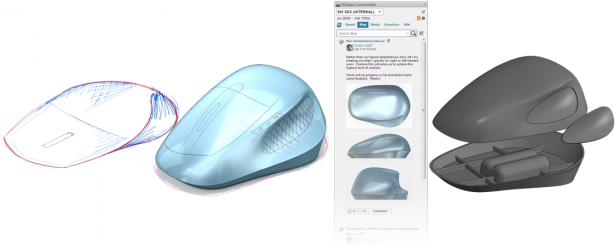
SOLIDWORKS also offers a series of tools for virtual prototyping. By using these tools, you can design products that are smaller, lighter, faster and cheaper because you can dramatically reduce the number of physical prototypes and expedite your time to market.
This toolset includes SOLIDWORKS Simulation which can analyze linear and nonlinear static and transient structural, shock and vibration, fatigue and drop test; SOLIDWORKS Flow Simulation which can simulate compressible and incompressible fluids, Newtonian and non-Newtonian liquids, laminar, turbulent and transitional flows; and SOLIDWORKS Plastics, which can simulate the injection molding plastic process.
SW virtual prototyping tools can tackle the critical thermal issues that arise when designing high tech products. Heat transfer can be solved by using both finite element analysis (FEA) and computational fluid dynamics (CFD). Now, when should you use one solution versus the other?
- SOLIDWORKS Simulation thermal tool is fast and appropriate for analyzing conduction heat transfer and does not require meshing of the fluid volume.
- SOLIDWORKS Flow Simulation thermal tool is accurate for all 3 heat transfer modes: conduction, convection and radiation. It solves for both solid and fluid domains and comes with a library of fans, heat sinks, PCBs and semiconductors.
Fig. 2. shows the Convection Coefficient calculated by SOLIDWORKS Flow Simulation. For this forced convection scenario, the Convection Coefficient is clearly not constant. Flow Simulation is the right tool for Heat Transfer in this case.
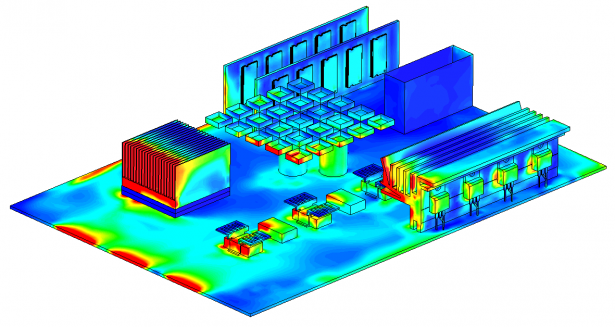
Finally, one more example drawn from the SOLIDWORKS suite of tools is our new SOLIDWORKS PCB product. SOLIDWORKS PCB bridges the gap between electrical and mechanical designs. This newest addition to our productivity toolset is a good example of how SOLIDWORKS is constantly innovating to bring our customers the best in class tools for solving their design challenges. By using SOLIDWORKS PCB, collaboration between mechanical and electrical design is seamless and efficient. As a result, it expedites the design cycle which allows you to bring your High Tech products to market faster and cheaper than ever before.
These are a few examples from the SOLIDWORKS suite of tools. To learn more about how to design high tech products smaller, lighter, faster and cheaper, watch this recorded webinar: “Designing a high-tech device from concept to manufacturing.”
You can also contact me for any questions via email at: Mai.Doan@3ds.com