Waters Model-Based Definition – A Cultural and Technological Challenge
The story of Model-Based Definition (MBD) at Waters actually began 20 years ago, long before we had SOLIDWORKS. Back then, using a different CAD system, we set out to integrate 3D annotations into our engineering design processes. As part of our overall CAD standards for traditional design, we created guidelines and standards for creating these 3D annotations. These standards outlined the default conditions for dimensions and tolerances and established how to interpret these annotations.
In those days, CAD systems were still primarily wireframe or simple constructive solid geometry (CSG) systems. There was no parametric or feature-based modeling. The models had no embedded intelligence – they were merely a collection of edges and faces. This lack of ‘smarts’ meant that the designer had to create the desired 3D annotations individually and manually, which often required the tedious process of reorienting coordinate systems and views to get the annotations in the correct spacial orientation. Tolerances and feature-specific annotations, such as hole callouts, had to be manually created as well. Additionally, the native CAD system was still required to view this information.
Neutral formats such as STEP or IGES, prevalent at the time, did not support the translation of this MBD information. This meant that downstream consumers had to invest in expensive CAD tools to use this information. The simple truth at the time was that it was still more efficient and productive to create 2D drawings. MBD was an ambitious goal that was doomed to fail, and unfortunately, it did.
Fast forward 20 years and CAD systems are now ‘smart,’ parametric, feature-based systems. Free viewing applications, such as eDrawings or 3D PDF, are readily available. Engineering teams routinely distribute their CAD designs to vendors and other collaborators in 3D. This improved technology led to a drastic change in engineering culture. Project teams are looking for ways to reduce design cycle times and reduce or eliminate errors that result in costly delays in project schedules.
In 2010, Waters made the decision to transition from our legacy CAD system to SOLIDWORKS. We conducted extensive evaluation and feasibility studies and in 2013, SOLIDWORKS was released for production use. This was a watershed moment, not simply because it ushered in a new era of improved CAD tools and product data, but because now, with SOLIDWORKS MBD, our decades-old goal of eliminating traditional 2D drawings – and establishing the 3D engineering models as the full and complete product definition – a single source of truth – could be realized.
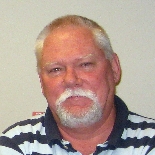
In late 2014, we began to introduce MBD to the organization. My group, Engineering Services, did an extensive evaluation of the technical feasibility of implementing MBD, including DimXpert, which I believe to be the foundation of MBD. This tool eliminates all of the roadblocks we experienced in our earlier attempts with MBD. Working closely with SOLIDWORKS teams, we developed presentations to a wide variety of business units – engineering, manufacturing, operations, inspection, purchasing, and external suppliers. The feedback from these presentations was incredibly positive. The common response from all these groups was that, finally, they would have the ability to view and interrogate a 3D model – no longer limited to 2D representations that could easily be misinterpreted, or in the worst case, be simply incorrect. A final presentation to our senior management team resulted in the endorsement of SOLIDWORKS MBD as a positive and necessary next step in improving our engineering and operations processes.
Beginning in 4Q 2015, SOLIDWORKS MBD will be implemented in a pilot project supporting the design of our latest product line. There will certainly be challenges as the culture adapts to this new technology, but I am certain that Model-Based Definition will be a success at Waters.
To learn more about SOLIDWORKS MBD, check out this page.