Simulating Fatigue Failure: It’s Like 1,000 Punches from My Grandmother!
When creating a product, every designer has a handful of questions in mind: Will my design withstand the warranty period for which it has been designed? Can I ensure that there are no warranty costs to the company? On the other hand is it over designed? Will it last far more than the life time that it is supposed to work?
To answer these questions, we often rely on prototype testing, manual calculations or previous experience. However, all these have their own pros and cons. To start, prototype testing is expensive; we might then look to manual calculation as an alternative. The downside is that manual calculation is best used in simple products only. Lastly, we’ll turn to experience, which, unfortunately, is not scalable. The best way is to have a well-established process which uses a software and can detect Fatigue failures.
Typical Failures due to Fatigue or repetitive loading can be seen in the below images:
So what is Fatigue failure? The analogy that I would like to share is using these images:
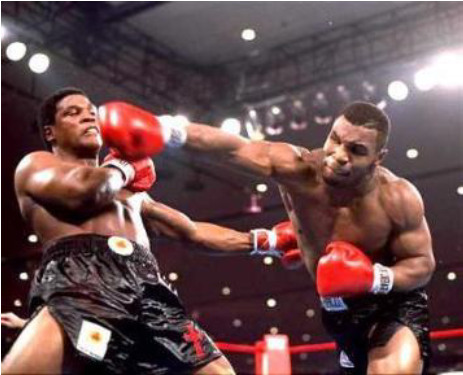
BUT…
Fatigue failure is similar to my grandmother giving 10000 Punches!
This phenomenon of fatigue failure can be simulated using Finite Element Analysis technology. Instead of creating prototypes, we can use software and simulate the phenomenon virtually. This will help us understand the product’s life cycle. I understand the fact that Life estimation software is expensive, however, DASSAULT SYSTEMES SOLIDWORKS has come up with a module called as SOLIDWORKS Simulation Standard which will cater to the Designers and help them predict product Life at a very competitive price. This should save huge warranty related costs and avoid unnecessary over designs.
Here’s a quick description of how it works. The normal static stress analysis has to be completed on the product where in the user applies loads, boundary conditions and provides a good idea of the location where the stress concentration is higher.
Fatigue failure is expected when this particular load repeat huge number of times. Some common examples are crank shafts, which are subjected to repetitive compressive and tensile loads, a simple door knob, which is subject to repetive opening and closing…and many more such scenarios, like being punched in the face 1000 times by my grandmother.
Now from the software point of view, once the user has the stresses from a static analysis, one creates a fatigue study and enters the number of times this particular load is expected to come. The Warranty time period can be used to find the number of times the part would be subjected to loading. The only other thing the user need to select is the Stress Vs Number of cycles (S-N) curve.
This particular curve is present for most of the materials in our Material database. If not, then Simulation Standard also has the option to calculate this curve based on ASME standards. The software will compare the stress levels with the S-N curve and give us the Life that is consumed and available life. That’s it, we know the life of the component without manufacturing it!
Here are a few examples of results:
Check out the following video on how it works in SOLIDWORKS Simulation: