3D Metal Printing Trends, Risks and Opportunities
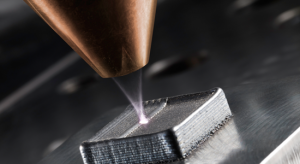
At the 2016 3D Metal Printing Experience Conference held in metro-Detroit on August 19, manufacturers gathered to understand commercial and technical trends as well as best practices in metal additive manufacturing. The 3D Metal Printing Magazine publishers hosted parts makers, operators, printing machine builders, industry analysts and R&D leaders from academia and the Oakridge National Laboratory.
From the insights of the guest speakers and discussions with several technology exhibitors, several significant trends, and opportunities are rapidly evolving. Attendees included those who are already printing metal parts and some who are considering an investment in this technology to disrupt the markets they serve.
Vision
As John Murray, president and CEO of Concept Laser, Inc., stated:
“3D metal printing enables smaller manufacturers to innovate and compete with industry giants.”
Beyond the Hype
The buzz that accompanies any new or rapidly evolving technology can often reach a fever pitch of positive hype. The afternoon panel of speakers reminded companies considering metal additive manufacturing that there are certain risks that come with the rewards in this exciting industry. For example, some of the metal powders in use like aluminum and titanium can be explosive if not handled properly. Secondly, minute contamination in the powders due to people, equipment or environment where the end part may be subjected to significant stresses or shocks in safety or mission critical applications can lead to catastrophic failures.
Best Practices
To prepare for success, the panelists encouraged interested manufacturers to do the following
- Carefully research printing machines and appropriate materials for the application
- Thoroughly plan post processing such as separation where multiple parts are produced in one machine cycle, residual stress reduction, and surface finishing
- Leverage local university additive manufacturing researchers
- Get trained by equipment and material suppliers
- Study and apply safe and clean handling practices. Err on the side of caution and safety.
- Create standard, documented work processes
3D Metal Printing Market Opportunity
The speakers identified several applications in industries where adoption is accelerating.
- Patient-customized implantable devices such as artificial joints and surgical instruments
- Representative prototypes and place-holder metal parts in vehicles to facilitate development testing
- Jigs, fixtures and molds for plastic parts and assemblies for any market
- Metal tooling of many kinds as a replacement for the loss of skilled tool making machinists who are reaching or even well past typical retirement age in many companies
Process Innovation
Many critical applications involving laser melting printing technology are very dependent on consistent density throughout the part and require non-destructive computed tomography (CT) scans to confirm there are no voids or contamination. So, manufacturers were encouraged to investigate printers that monitor the melt pool temperature and size in real-time during the entire printing cycle while capturing the process data to enable 3D visualization like CT software imaging. This style of in-process monitoring enables the parts maker to halt the printing cycle as soon as an anomaly is identified without wasting more time or material to complete the cycle. The audience was also reminded to seek out open printer data access architecture to enable quality assurance based on diagnostic and predictive analytics.
Process Control
Adam Rivard of LAI Int’l emphasized that manufacturers who choose to pursue metal additive manufacturing need to be smart in planning, documenting and then automatically monitoring in these nine business processes to assure safety and quality.
- Feed stock material sourcing and prep
- Contamination control
- Calibration and maintenance of equipment including lasers and sensors
- Equipment and process certification
- Product and process configuration management
- Build design analytics
- Build monitoring and trend analysis
- Technical product data “pedigree” traceability
- Quality and validation of entire build process (Control Plan)
From this observer’s viewpoint, backed by decades of manufacturing experience, what Mr. Rivard described as foundational to ensure thorough planning and execution of the often complicated 3D metal printing processes is a comprehensive enterprise information management system. The product and process planning, material sourcing, setup for production, quality assurance planning and documentation, real-time process monitoring, track-and-trace, analysis and reporting are the main components of a well-integrated enterprise resource planning (ERP) and manufacturing execution system (MES).
High-tech, metal additive manufacturers need process and information automation to ensure their long-term success.