Moving Additive Manufacturing from Concept to Production
Yesterday I had the pleasure of joining hundreds of additive manufacturing enthusiasts at the Dassault Systemes’ first-ever Additive Manufacturing Symposium in Chicago, which was part of the larger SCIENCE in the Age of Experience event being held May 15-18. The goal of the event was to bring the world’s leading experts and advocates of additive manufacturing (AM) together to share insights regarding the latest innovations, collaboratively address on-going industry challenges, and generate ideas to accelerate the widespread adoption and advancement of the technology.
The agenda was jam-packed with leaders from industry, government and academia. First up was Derek Luther, an engineer with Adidas, who discussed the role 3D printing played in the creation of the company’s first-ever 3D printed running shoe, the FutureCraft 4D, which features a highly complex lattice structure, shown in the video below here.
The German company partnered with Carbon, a tech company that uses an additive manufacturing process known as Direct Light Synthesis. By moving to additive manufacturing, Luther says the engineers and designers have more design freedom, can iterate quicker due to faster part speeds and now have the ability to engineer every cell of the shoe’s lattice structure per individual customer. The company plans to ship 5,000 of the shoes by end of year with plans to ramp up in 2018.
Next up was John Vickers from NASA’s Marshall Flight Center who emphasized how critical AM is to NASA’s missions, especially the Mars mission. Making the point that’s it’s impossible to bring additional supplies and redundant parts with the astronomical (pun intended) pay load costs for space travel, the ability to create parts through on-board 3D printing is essential to the mission.
Troy Hartwig from the Kansas City National Security Campus (NSC) discussed how AM has greatly increased designers ability to innovate has changed what was possible in design, introducing novel forms and shapes that were never possible before due to the constraints of traditional manufacturing methods. “Breakthroughs come when you stop thinking about design constraints and you can add complexity to your designs without the additional costs normally associated with that.”
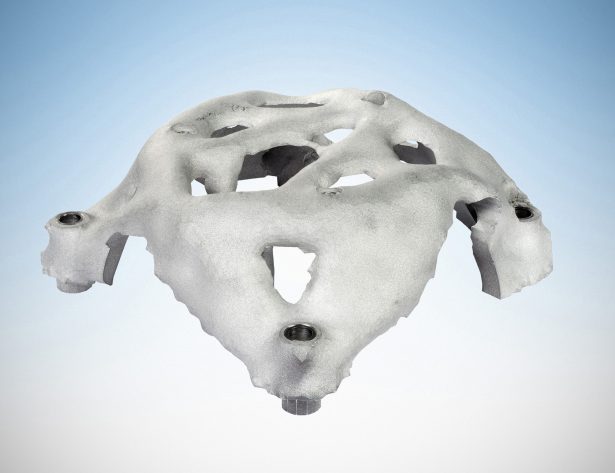
Jerry Feldmiller from Orbital ATK talked on the importance of industry participation in shaping future hardware, software and materials for AM. Feldmiller said his company has been very involved with AM, beta testing the company’s launch vehicle components using AM machines from Statasys, and believes that work has spawned many new areas of research at Orbital. He emphasizes the importance of internal user groups at companies to share important information on AM and to maximize machine use across teams and divisions. Feldmiller also believes that external user groups should be actively developing and sharing best practices for designing for 3D printing and that academia must play a role in STEM-related activities to address the growing skills gap, citing the 2 million jobs that will go unfulfilled over the next decade.
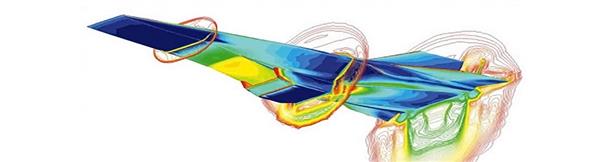
Tim Simpson, a professor at Penn State University, spoke about the challenges and research opportunities for AM. Simpson said that AM has drastically changed the way we approach design. By using AM engineers can design very lightweight components using internal lattice structures, something impossible by traditional manufacturing methods. He used the example of a Titanium 3D-printed hip implant, which can now go from concept to FDA approval in just 14 months. Another advantage is that through use of AM, these implants eventually will be fully customized to each patient’s body.
Jack Rome from The Aerospace Corporation discussed process simulation for developing AM parts for space applications. Most might think of simulation being used to analyze individual components or assemblies of components, however, to validate parts for space applications, the process of AM must also be validated. When designing for AM, material variability must be taken into consideration during the design process. He also emphasized the need for AM industry standards, in additional to the efforts of individual organizations, such as ASME.
Following up on the topic of standardization was Lyle Levine of the National Institute of Standards and Technology (NIST) who spoke on additive manufacturing of metals. One of the reasons Levine believes that metal AM isn’t more prevalent is its inherent complexities. The cooling rates of various alloys vary greatly, making the non-linear behavior of the material more unpredictable. To create metals parts with AM, users must use simulation to “bridge the gap.” His organization is working in a pillared approach to facilitate industry adoption; creating a “knowledge box” of tools to use for AM and an “engineering box” with standards, best practices, validation methods and benchmark tests.
Jack Beuth, a professor at Carnegie Mellon University, discussed the challenges of AM for industry. He said that while not many companies are using AM for production currently, the technology is still making a significant impact on product development. Often companies start with service bureaus and in-house tooling and prototyping as a first step into AM. He used GE as an example of a company spearheading the use of advanced digital manufacturing and AM, in particular. The company is currently using AM for producing many of the subsystems for jet engines. GE estimates that by using AM it can reduce part counts by 800 on its new jet engines and nearly 30 percent of the parts on its new gas turbine engine are being 3D printed.
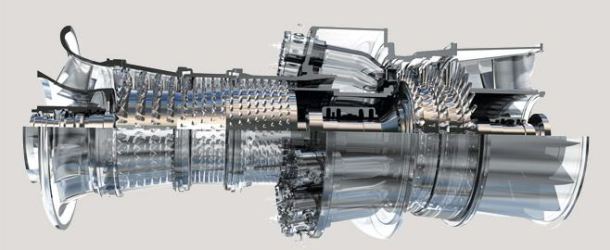
For more information on how the different types of additive manufacturing work, interesting articles and on-demand webinars, check out the new section on the SOLIDWORKS website at https://www.solidworks.com/am.