Quadcopter Project Brings SOLIDWORKS Mechanical Conceptual to the Skies
At the recent SIMULIA Community Conference in Providence, RI, we shared how we transformed a design process with the Dassault Systèmes 3DEXPERIENCE Platform and the power of simulation to solve a real problem in the developing world. SOLIDWORKS Mechanical Conceptual was used in the early stage of the design.
Many of us don’t realize that over one billion people lack regular access to roads. This disconnection to the outside world has a huge impact on transportation, economy, education and most critically health care. The team at SIMULIA was inspired by a Ted Talk by Andreas Raptopoulous of Matternet and we asked ourselves, “Could we redesign an existing drone quadcopter to help deliver medical supplies leveraging the 3DEXPERIENCE Platform?”
To answer this question, we set the following design goals:
- The quadcopter would have to carry a half-kilogram payload,
- for at least 30 minutes,
- for less than one dollar per flight.
The SIMULIA team used the new integrated design and simulation apps on the 3DEXPERIENCE Platform including SOLIDWORKS Mechanical Conceptual (SWMC) and Product Design Simulation (PDS) from SIMULIA and powered by the Abaqus solver. The design task was split into three phases:
- Conceptual design
- Detailed design
- Design for manufacturing
Concept Design
All design challenges have multiple variables that must be taken into account when moving towards an optimal solution. We determined that an optimized rotor/motor/battery design was the number one driver of the optimal quadcopter design to maximize life and flight time while minimizing the overall mass. A new set of rotors was designed to optimize lift, and using a potential flow code to analyze a series of rotor/motor combinations. We applied the analytic and decision support tools within the 3DEXPERIENCEPlatform to effectively weigh the tradeoffs between each of the rotor/motor/battery combinations against the mission duration, cost, and maneuverability before deciding upon a final configuration. We then used a 3D printer to rapidly create a physical prototype of the optimized rotor ready for flight tests.
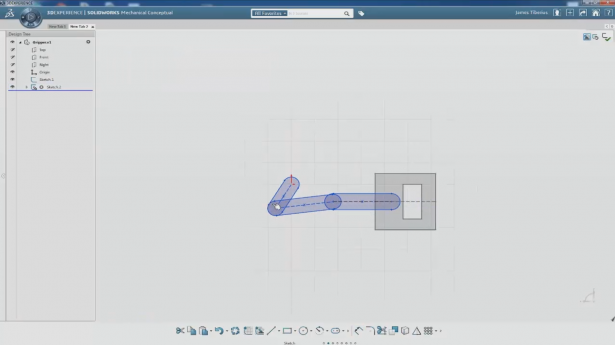
The commercial quadcopter had to be retro-fitted with a gripper/release mechanism for the delivery of the medical supplies. SWMC enabled us to quickly try out a number of design solutions. With its built-in 2D kinematic modelling capabilities, we quickly zeroed in to the correct concept that met the operational requirements. The 3D model was easily created from the initial 2D sketch and ran through a further set of structural tests. With PDS, we rapidly ensured that the designs met the required strength goals. In PDS, the component stresses and displacements were analyzed to validate that the gripper could endure its operating environment. Once the design was modified to meet the stress requirements, the components were printed in 3D.
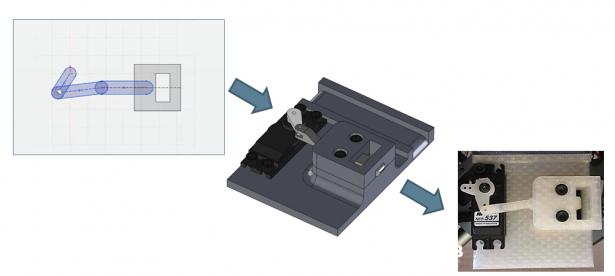
Detailed Design
As the revamped quadcopter design was being fleshed out, we moved into the detailed design phase. The next task was to guarantee that the rotor arms could bear operational loads (with the increase in weight) and that the quadcopter was durable enough to withstand a number of flights and even the occasional crash. We used a “Design of Experiment” approach to set up various quadcopter configurations for drop test to ensure performance of the quadcopter frame and landing gear during take-off and possible crash landings. These static loading analyses, drop analyses, and fatigue evaluations showed that the quadcopter was now efficient and durable.
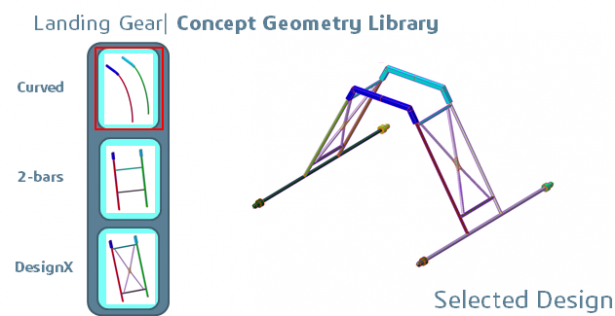
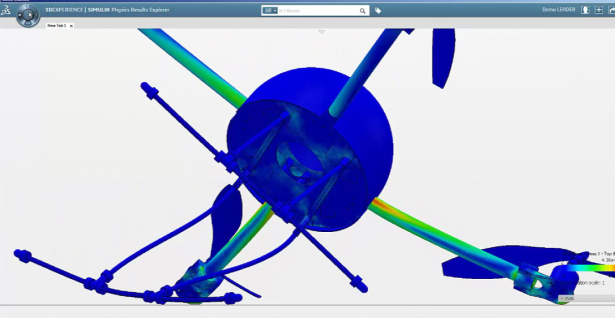
Design for Manufacturing
The last design task was to make sure that the new components were ready for manufacture. It’s not enough to imagine, develop, verify, and validate a great design; we also had to build it! The original arm bracket had not been optimized for load bearing performance, so a topology optimization was carried out to minimize flexibility while enforcing a mold ability constraint. After modifying the existing design, we increased the stiffness to ensure manufacturability.
Into The Real World
This design project was not just another virtual flight project. We built and tested the quadcopter verifying the new design and it worked as expected. The re-designed quadcopter was then brought on stage at the SIMULIA Community Conference. We were able to have it take off, release the medical supplies, and land successfully in front of the more than 700 people in the audience.
Using the 3DEXPERIENCE Platform, including SWMC and PDS, we took a product through the conceptual, detailed, and design for manufacturing phases and connected each step of the product design phase within one single platform.
To learn more about this project, watch the below video and go here (registration required): https://swym.3ds.com/#media:87564
To learn more about SWMC, go here: https://www.solidworks.com/sw/products/3dexperience/solidworks-mechanical-conceptual-overview.htm
To learn more about PDS, go here: https://www.solidworks.com/sw/products/3dexperience/simulia-structual-validation.htm
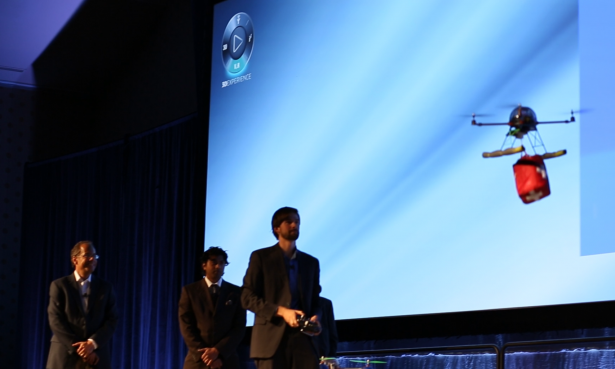
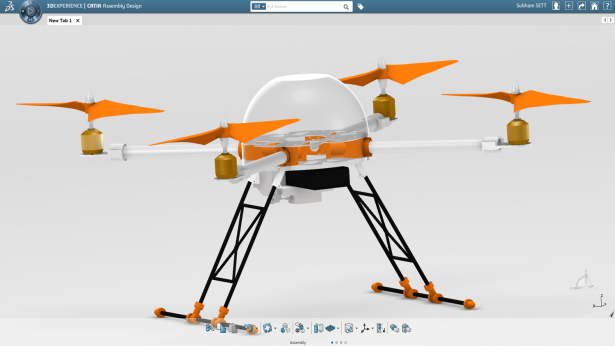