Are simulation tools only for analysts, or can designers use them too?
I often get this question from companies searching to optimize product development, from journalists writing about virtual simulation, or even from colleagues. When I think about it, I have the feeling that this is an old debate, but still a very lively one…
First, the world of product design and product engineering has changed since the 1980s, and so has the profile of users, organizations, and even education. Until recently, university curricula supported specialization as either an analyst or designer. But as I mentioned, fortunately, this has changed. A new generation of engineers is leaving college. If you ask them if they are a “designer” OR an “analyst”, they don’t really understand the question, because they have been educated as “engineers.” The two disciplines are equal in their mind to become “applications for engineering.”
Engineers can leverage their knowledge to design better products using 3D CAD AND simulation tools. Too often we think of designing with 3D CAD as a pure geometric activity. However, it’s most effective when it’s about quality, performance, and finding the best answer to the technical specifications. Therefore, simulation needs to be integral to the product development process.
Next, under the wide umbrella called “simulation”, you will find multiple use cases. With a CAD-embedded simulation solution, not only have finite element analysis (FEA) and computational fluid dynamics (CFD) become mainstream products, but simulation is now a powerful and accessible engineering tool for any product engineer to use. The world of virtual simulation has changed drastically, and this is a fantastic thing – now every engineer involved in product development can benefit from the insights of FEA, CFD, and more. We don’t do simulation for just safety tests in aerospace or the automotive industry anymore. Virtual simulation offers its benefits to a wider audience to design innovative products. Engineers can apply corrective action on the design that is triggered by the simulation results.
I feel this change/evolution is very positive, as simulation is not “hidden” anymore, or done by only a few analysts inside a company or unknown by users. Now, simulation is becoming a true engineering tool that’s highly visible internally and externally. And then you still have specific use cases where an engineer with an analysis background will bring the expertise and experience of advanced simulations as needed, such as crash tests or final validation of the optimized products.
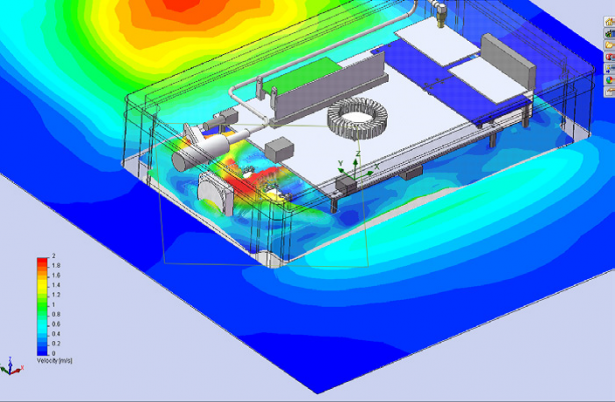
So, who should use simulation? Engineers should. I believe that it is more about the skills of the users and the willingness to use new engineering tools, coupled with intuitive and powerful simulation tools that make for the success of virtual simulation implementation. Skilled engineers with unique engineering tools such as SOLIDWORKS Simulation are empowered to create successful products.
Want to learn more about SOLIDWORKS Simulation? Check out our First Look at Simulation video to see how simulation could improve your own designs and reduce prototypes.