La fabrication additive : du concept à la production
Hier, j’ai eu le plaisir de me joindre à des centaines de passionnés de la fabrication additive lors du tout premier séminaire de fabrication additive de Dassault Systèmes, dans le cadre de l’événement SCIENCE in the Age of Experience qui s’est tenu du 15 au 18 mai. L’objectif de l’événement était de rassembler les experts et représentants du monde de la fabrication additive (FA), afin de partager des connaissances sur les dernières innovations, de répondre ensemble aux défis du secteur et de générer des idées pour accélérer l’adoption et l’avancement de la technologie.
De nombreux leaders du secteur, du gouvernement et du milieu universitaire ont répondu présent. Tout d’abord, Derek Luther, ingénieur chez Adidas, a présenté le rôle de l’impression 3D dans la création de la première chaussure de course imprimée en 3D de la société, la FutureCraft 4D, qui présente une structure en treillis très complexe. Vous pouvez la découvrir dans la vidéo ci-dessous.
La société allemande s’est associée à l’entreprise de technologie Carbon, qui utilise un processus FA nommé Direct Light Synthesis. Grâce à la fabrication additive, Derek Luther indique que les ingénieurs et les concepteurs disposent de plus de liberté dans la conception, peuvent opérer des itérations plus rapidement en raison de l’augmentation de la vitesse d’obtention des pièces, et ont maintenant la capacité de créer chaque cellule de la structure en treillis en fonction des exigences du client. La société prévoit d’expédier 5000 chaussures d’ici la fin de l’année, avec une accélération en 2018.
Quant à John Vickers, du Marshall Flight Center de la NASA, il a souligné le rôle majeur de la FA dans les missions de la NASA, en particulier la mission Mars. Étant donné qu’il est impossible d’emporter des fournitures supplémentaires et des pièces redondantes en raison des coûts astronomiques de la charge utile en navigation spatiale, la possibilité de créer des pièces grâce à l’impression 3D embarquée est essentielle à la mission.
Troy Hartwig de Kansas City National Security Campus (NSC) a expliqué comment la FA a considérablement augmenté la capacité des concepteurs à innover. La technique a changé le champ des possibles en matière de conception, en introduisant des formes nouvelles qui n’étaient pas possibles auparavant, en raison des contraintes liées aux méthodes de fabrication traditionnelles. « Vous découvrez et innovez lorsque vous arrêtez de penser aux contraintes de conception et que vous pouvez ajouter de la complexité à vos conceptions, sans les coûts supplémentaires qui en découlent habituellement. »
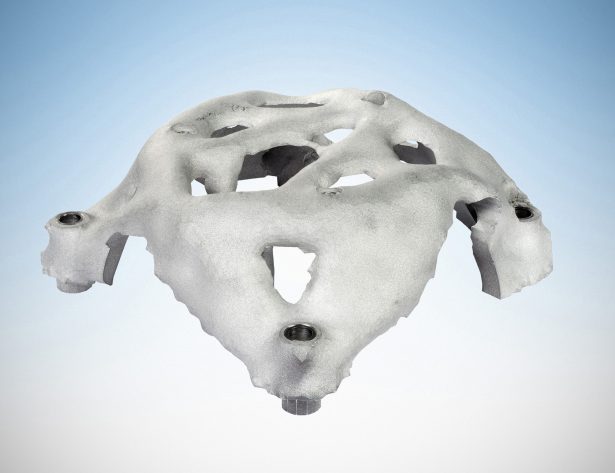
Jerry Feldmiller d’Orbital ATK a souligné l’importance de la participation du secteur dans la conception du matériel, des logiciels et des matériaux de demain pour la fabrication additive. L’entreprise de Jerry Feldmiller s’est beaucoup impliquée dans la fabrication additive, bêta testant des composants de véhicules via des machines FA de Statasys. Il estime que ce travail a mis au jour de nombreux domaines de recherche chez Orbital. Il souligne qu’il est crucial que les groupes d’utilisateurs internes dans les entreprises partagent les informations clés sur la FA et optimisent l’utilisation des machines au sein des équipes et des divisions. Jerry Feldmiller estime également que les groupes d’utilisateurs externes doivent développer et partager activement les pratiques d’excellence de conception pour l’impression 3D. Quant aux universités, elles doivent s’impliquer dans les activités STEM pour combler le fossé croissant en matière de compétences, citant les 2 millions d’emplois qui ne seront pas pourvus lors de la prochaine décennie.
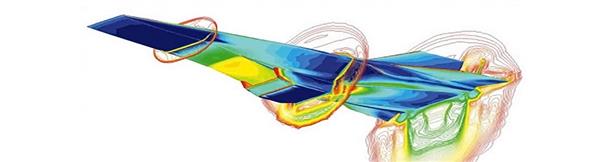
Tim Simpson, professeur à la Penn State University a parlé des défis et des opportunités de recherche en matière de fabrication additive. Il a déclaré que la FA a radicalement changé la façon dont nous abordons la conception. En faisant appel à des ingénieurs FA, on peut concevoir des composants très légers en utilisant des structures internes en treillis, ce qui était impossible avec les méthodes de fabrication traditionnelles. Il a donné l’exemple d’une prothèse de la hanche en titane imprimée en 3D, qui peut désormais passer de la phase de conception à l’approbation de la FDA en seulement 14 mois. De plus, grâce à l’utilisation de la FA, ces prothèses pourront un jour être entièrement personnalisées pour le corps de chaque patient.
Jack Rome de The Aerospace Corporation a mentionné la simulation de processus pour le développement de pièces FA pour des applications spatiales. On pense souvent que la simulation est utilisée pour analyser des composants individuels ou des assemblages de composants. Cependant, pour valider des pièces pour des applications spatiales, le processus FA doit également être validé. Lors de la conception en vue d’une fabrication additive, la variabilité du matériau doit être prise en compte. Il a également souligné la nécessité de normes industrielles FA, en plus des efforts des entreprises individuelles, telles qu’ASME.
Toujours sur le thème de la normalisation, Lyle Levine de la National Institute of Standards and Technology (NIST) s’est concentré sur la fabrication additive des métaux. Selon Lyle Levine, si la FA métallique n’est pas plus répandue, c’est en partie à cause de ses complexités inhérentes. Les vitesses de refroidissement de divers alliages varient considérablement, ce qui rend le comportement non linéaire du matériau plus imprévisible. Pour créer des pièces métalliques avec la FA, les utilisateurs doivent utiliser la simulation pour « combler les écarts ». Son entreprise travaille selon une approche à plusieurs piliers pour faciliter l’adoption par l’industrie, et a créé une « boîte de connaissances » composée d’outils à utiliser pour la FA et une « boîte d’ingénierie » avec des normes, des pratiques d’excellence, des méthodes de validation et des tests d’évaluation.
Jack Beuth, professeur à la Carnegie Mellon University est intervenu sur les défis de la FA pour le secteur. Selon lui, bien que peu de sociétés utilisent actuellement la production FA, la technologie a néanmoins un impact significatif sur le développement de produits. Souvent, les entreprises commencent avec des bureaux de service ainsi que des outils et prototypages internes comme première étape de la fabrication additive. Il a cité GE comme entreprise à l’avant-garde de l’utilisation de la fabrication numérique et de la fabrication additive avancées. La société fait actuellement appel à la FA pour produire de nombreux sous-systèmes pour moteurs à réaction. GE estime qu’en utilisant la FA, il est possible de réduire de 800 le nombre de pièces de ses nouveaux moteurs à réaction. De plus, environ 30 % des pièces de son nouveau moteur à turbine à gaz sont imprimées en 3D.
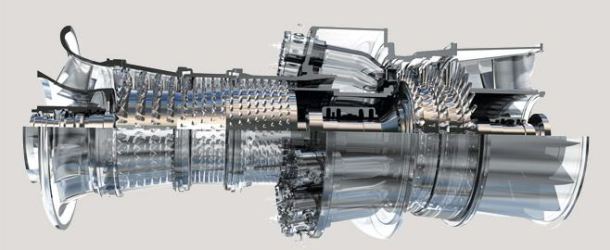
Pour plus d’informations sur le fonctionnement des différents types de fabrication additive, des articles et des webinaires à la demande, consultez la nouvelle section du site Web SOLIDWORKS à l’adresse https://www.solidworks.com/am.