Additive Fertigung – vom Konzept zur Herstellung
Im Mai hatte ich das Vergnügen, Hunderte von Fans der additiven Fertigung auf dem allerersten Additive Manufacturing Symposium von Dassault Systèmes in Chicago zu treffen, das im Rahmen von SCIENCE in the Age of Experience vom 15. bis 18. Mai stattfand. Hier sollten sich die weltweit besten Experten und Fürsprecher der additiven Fertigung treffen, um Erkenntnisse zu den neuesten Innovationen auszutauschen, gemeinsam aktuelle Herausforderungen in der Branche zu erörtern und Ideen zu generieren, um die weitere Verbreitung und Förderung der Technologie zu beschleunigen.
Die Tagesordnung war mit Führungspersönlichkeiten aus Industrie, Regierung und Wissenschaft gespickt. Zuerst erläuterte Derek Luther, Ingenieur bei Adidas, die Rolle des 3D-Drucks bei der Schaffung des allerersten 3D-gedruckten Laufschuhs FutureCraft4D, dessen extrem komplexe Gitterstruktur im Video unten gezeigt wird.
Die deutsche Firma arbeitete mit Carbon zusammen, einem High-Tech-Unternehmen, das den additiven Fertigungsprozess Direct Light Synthesis einsetzt. Der Wechsel zur additiven Fertigung gibt den Ingenieuren und Konstrukteuren mehr Freiheiten beim Entwurf und höhere Teilgeschwindigkeiten beschleunigen Iterationen. Darüber hinaus kann jetzt jede Zelle des Netzmusters genau auf den einzelnen Kunden abgestimmt werden. Das Unternehmen plant, bis Jahresende 5.000 Schuhe zu versenden, 2018 sollen es noch mehr werden.
Als nächstes sprach John Vickers vom Marshall Flight Center der NASA, der erklärte, welche bedeutende Rolle die additive Fertigung bei NASA-Missionen spielt – insbesondere bei der zum Mars. Aufgrund der im Wortsinne astronomischen Lagerungskosten können bei einer Raummission unmöglich alle Ersatzteile mitgenommen werden – es geht also unterwegs nichts ohne den 3D-Druck.
Troy Hartwig vom Kansas City National Security Campus (NSC) erläuterte, wie Konstrukteure dank additiver Fertigung besser innovieren können und dadurch die Konstruktion viel mehr Möglichkeiten bietet, beispielsweise neue Formen, die aufgrund der Beschränkungen traditioneller Fertigungsverfahren bisher nicht möglich waren. „Der Durchbruch kommt, wenn nicht mehr über Zwangsbedingungen der Konstruktion nachgedacht wird, sondern der Entwurf komplexer werden kann, ohne dass damit auch gleich die Kosten steigen.“
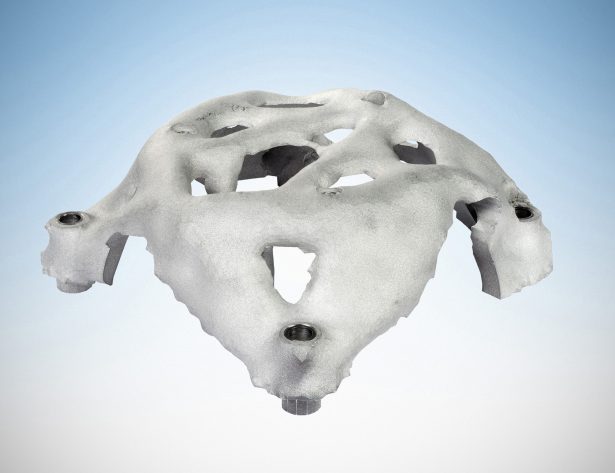
Jerry Feldmiller von Orbital ATK sprach über die Bedeutung der Beteiligung der Industrie an der Entwicklung zukünftiger Hardware, Software und Materialien für die additive Fertigung. Feldmiller sagte, dass sein Unternehmen die additive Fertigung umfangreich einsetze: Die Komponenten des Trägerfahrzeugs seines Unternehmens werden mithilfe additiver Fertigungsmaschinen von Statasys getestet, und er ist davon überzeugt, dass sich daraus für Orbital viele neue Forschungsbereiche ergeben haben. Er betonte die Bedeutung der internen Nutzergruppen in Unternehmen, die wichtige Informationen zum Thema additive Fertigung austauschen und die Maschinennutzung team- und abteilungsübergreifend maximieren. Feldmiller glaubt auch, dass externe Nutzergruppen aktiv an der Entwicklung und dem Austausch von bewährten Vorgehensweisen für den Entwurf von 3D-Drucken beteiligt werden sollten und dass Hochschulen eine Rolle bei den MINT-bezogenen Aktivitäten spielen müssten, um die wachsende Lücke in den Fertigkeiten zu überbrücken. In den nächsten 10 Jahren würden sonst 2 Millionen Stellen nicht besetzt werden können.
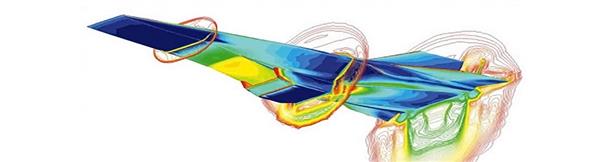
Tim Simpson, Professor an der Penn State Universität, sprach über die Herausforderungen und Chancen der additiven Fertigung. Simpson sagte, dass die additive Fertigung unsere Herangehensweise an die Konstruktion grundlegend verändert hat. Dank der additiven Fertigung können Ingenieure extrem leichte Komponenten mit internen Gitterstrukturen entwickeln. Dies wäre mit herkömmlichen Fertigungsmethoden unmöglich. Als Beispiel erwähnte er ein mit 3D-Druck erzeugtes Hüftimplantat aus Titan, das es in lediglich 14 Monaten vom Konzept bis zur FDA-Genehmigung geschafft hat. Außerdem können diese Teile dank additiver Fertigung exakt auf den Körper jedes einzelnen Patienten abgestimmt werden.
Jack Rome von The Aerospace Corporation sprach über die Prozesssimulation bei der Entwicklung von additiv gefertigten Teilen in Raumfahrtanwendungen. Bei der Validierung von Teilen für die Raumfahrt müssen nicht nur einzelne Komponenten oder Baugruppen von Komponenten analysiert werden, sondern auch der Prozess der additiven Fertigung selbst. Außerdem muss bei der Konstruktion für die additive Fertigung auch die Materialvariabilität bedacht werden. Er betonte außerdem, dass neben den Bemühungen einzelner Gruppen wie der ASME auch Branchenstandards für die additive Fertigung notwendig seien.
Im Anschluss an das Thema der Standardisierung sprach Lyle Levine vom National Institute of Standards and Technology (NIST), über die additive Fertigung von Metallen. Levine ist der Ansicht, dass die additive Fertigung von Metallen deshalb so selten vorkommt, weil sie sehr komplex ist. Die Abkühlgeschwindigkeiten verschiedener Legierungen unterscheiden sich sehr, was das nicht-lineare Verhalten des Materials noch unberechenbarer macht. Damit Metallteile additiv gefertigt werden können, müssen die Nutzer die „Lücke“ mit Simulationen füllen. Seine Organisation arbeitet an verschiedenen Säulen, um die Akzeptanz in der Branche zu steigern. Dabei sind eine „Knowledge Box“ mit Werkzeugen für die additive Fertigung und eine „Engineering Box“ mit Standards, bewährten Vorgehensweisen, Validierungsmethoden und Benchmark-Tests entstanden.
Jack Beuth, Professor an der Carnegie Mellon University, sprach über die Herausforderungen der additiven Fertigung in der Industrie. Obwohl momentan nur wenige Unternehmen die additive Fertigung tatsächlich nutzen, hat die Technologie doch große Auswirkungen auf die Produktentwicklung. In vielen Unternehmen sind Servicebüros sowie interne Werkzeuge und Prototyping die ersten Schritte in Richtung additiver Fertigung. Am Beispiel von GE erklärte er, wie ein Unternehmen den Einsatz der erweiterten digitalen Fertigung und insbesondere der additiven Fertigung vorantreiben kann. Das Unternehmen nutzt die additive Fertigung momentan zur Fertigung zahlreicher Subsysteme für Düsentriebwerke. GE schätzt, dass die Zahl der Teile seiner neuen Düsentriebwerke dank additiver Fertigung um 800 sinken wird und fast 30 Prozent der Teile der neuen Gasturbine 3D-gedruckt sein werden.
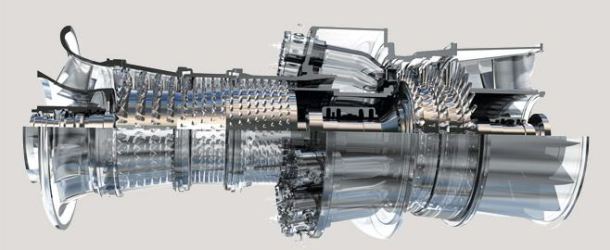
Weitere Informationen darüber, wie die verschiedenen Arten von additiver Fertigung funktionieren, interessante Artikel und abrufbare Webinare finden Sie im neuen Abschnitt der SOLIDWORKS Website unter https://www.solidworks.com/am.
Autorin: Barbara Schmitz, Senior Brand Introduction Manager bei Dassault Systèmes SOLIDWORKS – zum Originalartikel gelangen Sie hier.