Design to Manufacture – Introducing NC Shop Floor Programmer
NC Shop Floor Programmer provides full 3-axis machining capabilities, 4- and 5-axis pre-position, and wire EDM into a single role. Toolpath simulation and machine kinematics are standard capabilities included in all DELMIA machining roles.
We developed the NC Shop Floor Programmer for three reasons. Reason number one is for the small machine shop or the single user running SOLIDWORKS® who need to get the most value out of their respective machines tools.
The second reason is for the machinist who needs to create G-code programs on the shop floor for simple parts—maybe a clamp or a tooling fixture—that need to get done quickly rather than wait on engineering.
The third reason is for shop floor personnel who want to review existing NC programs from their manufacturing department before running the job. This capability is highly coveted by those who wish to review multi-axis and Mill-Turn simulations. The new NC Shop Floor Programmer role provides them with this capability without purchasing more expensive multi-axis machining solutions.
What do some of the Shop Floor Machining features look like?
Moving down to the Action Bar, we have three main section tabs used to create toolpath operations.
The Prismatic Machining section tab contains Prismatic Area, providing users with the ability to detect and machine leftover material in corners and channels with a smaller tool. Profile contouring is also included as well as Pocketing, Point to Point, Curve Following, and finally Probing for multi-points, Corners, Slots and Ribs, and Holes or Pins.
The Surface Machining section tab contains Roughing, which can rough-out an entire part. Sweeping allows you to create a finishing or semi-finishing operation to machine a roughed-out part in vertical parallel planes. Z-Level machining operations are finishing or semi-finishing operations that machine the whole part by parallel horizontal planes perpendicular to the tool axis.
Advanced Finishing combines vertical Z-Level passes with horizontal machine passes that are contour-driven. Deburring is an exciting new capability that can automatically detect sharp edges on finished parts and then chamfer these edges. Candidate edges are pre-displayed, allowing users the flexibility to filter any of the selections.
Turning ideas into reality
What is the reason for design and manufacturing? I know that is a broad question, but at its core, I think it is the process of turning an idea or passion into reality. Because no two people are alike, there is always a new idea or passion being brought into the world. By now, most people know that my passion for design and manufacturing started on the farm and in the junkyard. I was lucky that one side of my family had an AGCO dealership, and the other owned a salvage yard.
Early on, I fell in love with how things work and fixing things that were broken. I put my first v8 engine in a car when I was just 14 years old in my grandpa’s driveway. This passion has been with me throughout my entire life, even though I have less time in the shop these days than I would like.
But what if your passion led you to build the largest manufacturer of “build-it-yourself” component car kits? What does that journey look like? What challenges would you face? How do you keep up with all the “new” car builders?
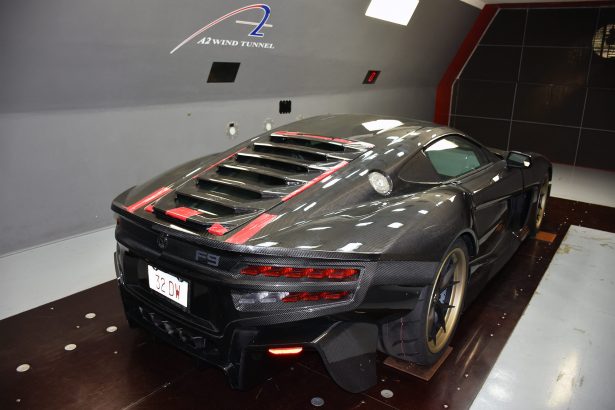
Please tune into Manufacturing Live on Tuesday, December 7th at 11AM ET on YouTube or LinkedIn if you want to know more. We are honored to have Dave Smith from Factory Five who will discuss this journey in more detail and talk about the company’s latest challenge of building a Supercar at 3DEXPERIENCE World 2022. Also, don’t miss on seeing Factory Five’s Supercar in the Live Shop Floor at at 3DEXPERIENCE World 2022 in Atlanta, February 6-9th, 2022. You can register by clicking the link below.