From a Garage to the World: Creating the World’s First Automatic Flight Forming Machine with SOLIDWORKS
Sydney-based mechatronic engineers, Hayel Smair and David Gardner have held a shared passion for robotics since they were young. As veteran contractors in Australia’s flight manufacturing industry, they had been observing gaps in the industry to find ways to introduce robotic innovations into their projects. Working from a garage in the Sydney suburbs, Hayel and David have striven to develop an innovative solution to flight formation aerodynamic design that will transform existing flight manufacturing methods.
Using SOLIDWORKS linear force analysis and powerful simulation tools, the engineers trialed several concepts and designs before finally developed a viable prototype of an 8-axis robot to automate flight formation, which helps to tackle potential inherent problems in aerospace engineering efficiently. The two engineers named their prototype, “RoboHelix,” and started demonstrating it on YouTube in January 2017, which captured the attention of large manufacturers worldwide.
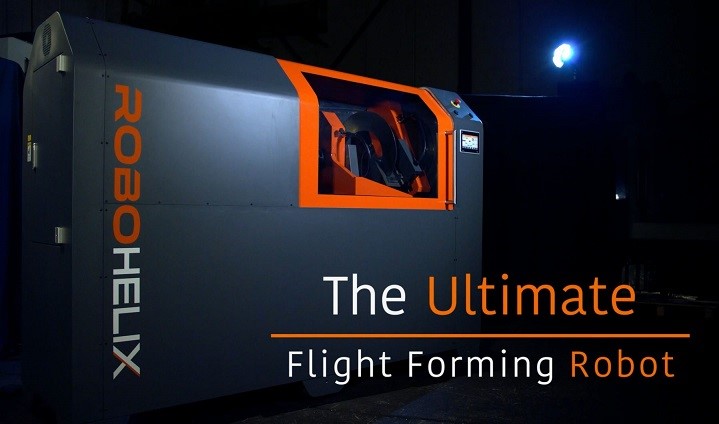
Within just two years, RoboHelix has grown into a global company, exporting to customers based in Europe and the US, thereby mirroring the early success of other renowned companies such as Apple, Hewlett Packard and Amazon…oh and SOLIDWORKS that got their respecitve, if humble, starts in garages.
With SOLIDWORKS, RoboHelix has created a truly innovative method to automate flight formation design and in doing so, they have pioneered new advances in the flexibility of flight formation technology and speed of operation.
Overhauling traditional methods
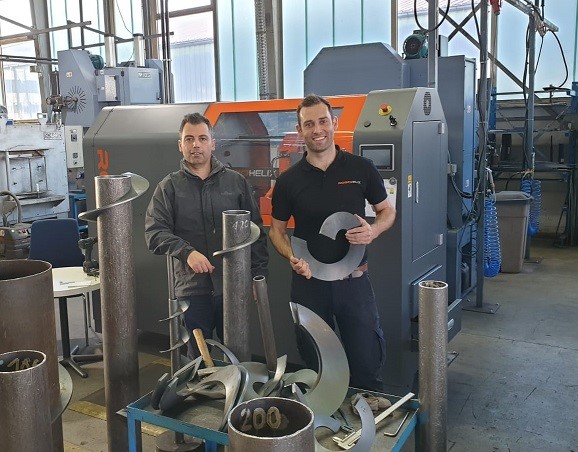
The flight forming process in flight manufacturing is a highly specialized skill. Traditional flight-forming machines used platens, dyes, dye plates that correspond to the pitch and size of the flight. Such dye plates are often bulky to handle and time-consuming to manually tool, adjust and set up, not to mention cost-prohibitive to replace if they are damaged.
In addition, these traditional machines use hydraulics with the operator’s hands only millimeters away from reciprocating jaws exerting forces up to 50 tons. This highly unsafe method has caused multiple injuries across the industry, resulting in calls for higher safety standards in flight-formation machinery.
Noting these deficiencies, Hayel and David started to take a closer look into how a flight is produced from a flat blank to a helical flight. They deduced specific movements that a flight takes when it is transformed in shape from the disc to helical flight, and developed the prototype of RoboHelix to mathematically define these natural movements and reproduce them to form a flight.
The result was RoboHelix, the world’s first automatic flight forming machine, which has captivated the attention of global flight manufacturers with its huge leap in innovation. RoboHelix machines have successfully increased production rate, lowered production cost and enhanced safety in flight formation for several global flight manufacturers around the world.
New advances in enhancing operator safety
Prior to the RoboHelix machine, only traditional technologies in flight formation existed, with no alternative available. With the RoboHelix machine hitting the market, a new innovative solution now exists to solve numerous flight manufacturing problems and importantly, enhance operator safety.
With the RoboHelix machine, the flight formation operation is completely enclosed within the machine, which makes it far safer for the operator during the flight-forming process. With no manual set-up of flight-forming industrial dyes, dye plates, platens, packers or slippers required, human error is minimized during the flight-forming process. In addition, as the necessity of industrial dyes is eliminated, no protective coatings are required for the machine’s high-quality stainless steel components, which further reduces costs.
Utilizing HelixNinja, a blank generation cloud-based SaaS, the RoboHelix machine applies unique mathematical algorithms to calculate, analyse, and mimic the natural helical forming path. At the same time, it can automatically compensate for material elasticity during the flight forming process, thereby doing away with manual human measurements or calculations that would have otherwise required repeated checks and validations.
International recognition and patenting
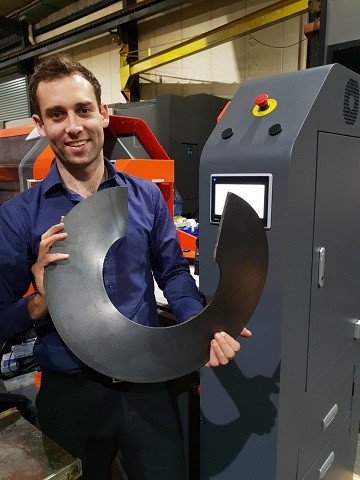
In May 2017 the International Searching Authority (ISA) determined that all 19 claims of the RoboHelix technology are novel and inventive. RoboHelix has proven to increase flight-formation production set-up rates by 45 times on average, decreases power consumption by up to 300 times, removes human error from the manufacturing process and completely eliminates all safety concerns within the forming process.
SOLIDWORKS, a key success factor for RoboHelix’s design innovations
Hayel and David use the features of SOLIDWORKS in the production of RoboHelix machines through a number of ways. First and foremost, the design configuration feature in SOLIDWORK breaks down the machine design into its manufacturing stages, which correspond to production drawings.
Using an 8-axis robotic system requires very high tolerances during movements with very large loads up to 50,000Kg. Numerous parts have critical tolerances and to achieve this precision, the engineers relied on SOLIDWORKS’ 3D capabilities to assemble these tolerances, and FEA simulation to analyze components and optimize the parts for feature design, fit for manufacturing processes and procedures, as well as weight optimization.
Finally, SOLIDWORKS Simulation helps Hayel and David reduce design time by eliminating multiple test models and increases their knowledge of predictive structural behaviours, empowering them to easily and quickly inform their customers of any design constraints.
SOLIDWORKS’ ability to change dimensions, tolerances and processes of the machine parts and models on-the-go, whether in part or assembly mode, has been cited as the key success factor of the RoboHelix machine.
What’s next for RoboHelix?
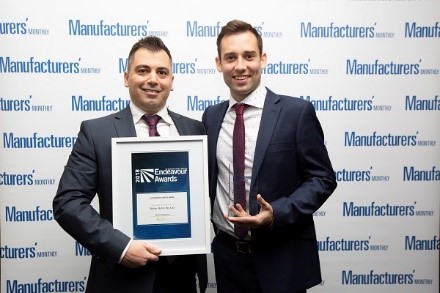
RoboHelix plans to open sales offices in the USA and Europe by end of 2019 to service its growing portfolio of global customers. Currently in the works is enhancement of cloud-based integrated services, including management tools, to provide customers with greater access to production data and metrics, and feedback loops, as well as monitoring, tracking and updating of RoboHelix machine performance on-the-go. The company is also researching into next-generation AI features for seamless equipment communication and process flow within the overall factory operating floor.
For RoboHelix, this is just the start of their journey. Hayel and David are constantly brainstorming with their team of engineers to create new, innovative features in its range of flight formation machines. With SOLIDWORKS, their ideas can go into production faster with precision design, FEA and simulation.
For more information on RoboHelix, please visit their website at www.robohelix.com. RoboHelix worked with CADSPACE, one of Australia’s leading SOLIDWORKS resellers. For more information, visit their website at www.cadspace.com.au.