Developing the Community in Kansas in More Ways Than One
There’s a quote by Denzel Washington that applies all too well to many members of the SOLIDWORKS user community:
“At the end of the day, it’s not about what you have or even what you’ve accomplished. It’s about who you’ve lifted up, who you’ve made better. It’s about what you’ve given back.”
This is something Eric Spurgeon, a longtime SOLIDWORKS user, entrepreneur, and leader of the South Central Kansas SOLIDWORKS User Group, understands well. Every day, he helps other people with their projects and develops his own – and he uses SOLIDWORKS to make it happen.
I met Eric after a colleague of mine e-mailed me to tell me she’d met him at SOLIDWORKS World 2019. She told me she’d just met a “new group leader who has a new startup.” My first reaction was: that’s a lot of newness for one human being!
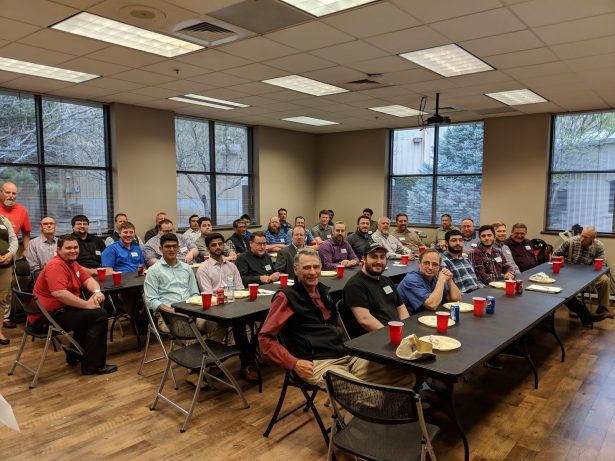
Over the past couple months, having spoken with Eric multiple times – gauging his passions, interests, and, ultimately, what drives him to do the things he does – it all makes sense, however.
Eric’s roots are firmly implanted in the community of Wichita, Kansas, having grown up two hours west in the 200-person town of Mullinville. He still lives in Kansas today. It’s where he runs his engineering consulting business, Tarhun 3D, and it also happens to be the location of his user group.
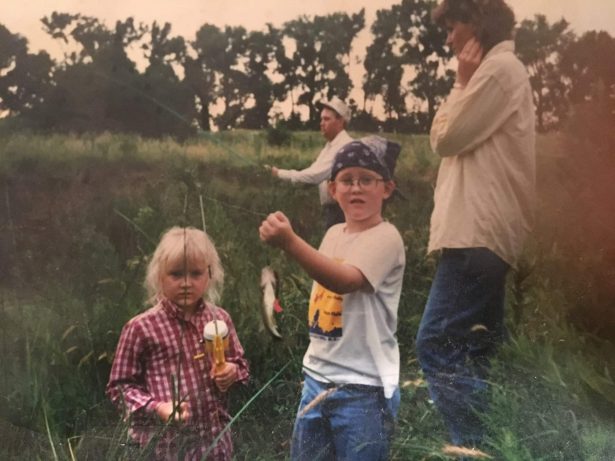
But long before any of that, Eric spent his upbringing growing up on a 2500-acre ranch in the area. He’s a hard worker – in fact, he worked his way all the way through engineering school over at Kansas State University. He graduated in 2014 with B.S. in Mechanical Engineering, but while in school (and prior, as Spurgeon Fence Construction was founded in 2008), he also spent a lot of time working on agricultural fence installations.
This required heavy time expenditure. And the installations themselves? They weren’t easy. They were laborious. Taxing.
“A mile of fence takes 7-10 days with 3-4 people,” Eric told me.
Luckily for many, Eric is an innovator. During his time in engineering school, he learned a great deal about lean manufacturing concepts. Motivated by his own aching muscles and his drive to create, he began to think: “Can these same concepts be applied to the fencing industry?”
The impetus for this thought wasn’t entirely self-serving. Far from it. Having grown up on a ranch and spent time around them all of his life, the urge to create a better fencing solution was informed by his sense of empathy as much as anything else.
“There’s an aging population of ranch owners. They can’t physically install this fencing the way it’s been done traditionally. So they find themselves having to outsource it,” Eric says. “This takes a lot of time and money.”
The system (and many laborers’ backs) felt broken. Worse yet, the problem is compounded by other socioeconomic factors.
“These areas are economically depressed as it is,” Eric continued. “People are leaving, because there just isn’t much industry opportunity.”
Eric was able to go to college because of the very fencing business that inspired these same yearnings for change and improvement. Without it, he says, “college wouldn’t have been an option.” With his experience and his Kansas State education, however, he’s looking to improve not only the industry he’s spent so much time around, but his local community as well.
With the help of a venture capital partner, he’s currently developing a new agricultural fencing solution that solves a lot of the fencing woes he’s witnessed firsthand. Instead of the estimated 7-10 days to install a mile of fence with three or four people, Eric says he’s working on a solution that would only require one day of work with two people.
His patent-pending solution will be “light and easy to install,” Eric shared, with the ability to “collapse down for simple transport and storage.”
Using SOLIDWORKS, Eric’s been aided heavily by the top-down design capabilities. “I designed the product originally as a multi-body sheet metal part, then split it out into an assembly. Adding the mates there allowed me to see dynamic motion of the entire assembly.”
His aim is to save future generations from the “human capital cost,” as he termed it to me, that comes from installing agricultural fencing the way it’s traditionally been done. “Imagine driving a 45 lb. steel pipe into the ground over 1,000 times per day. It’s labor-intensive. It isn’t a good activity for anyone’s body.”
By verifying motion between components in SOLIDWORKS, he’s working to effectively save others from anatomical issues that may result as a byproduct of these potentially harmful repetitive motions done in real life.
With everything he does Eric’s ultimate goal is to help support the innovation ecosystem in the Central Kansas Community. He does this as a user group leader, consulting engineer, and hopefully, agriculture fence revolutionary.