Keep On (Monster) Truckin’: Detailing the Max-D
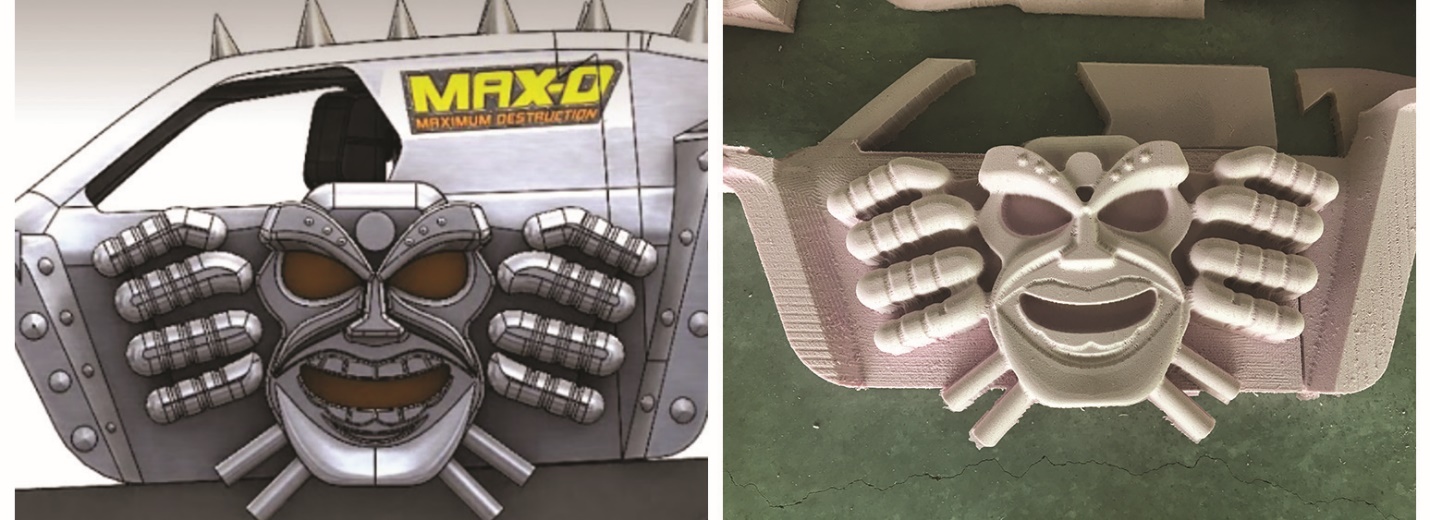
“The devil’s in the details,” or so goes the old phrase. For members of the SOLIDWORKS Magic Wheelchair build team, however, Maximum Destruction is in the details. Taking pieces of pink and black foam and transforming them into a perfect replica of an intricate monster truck is no small feat. Sub teams have been working together to create the details that will bring Jonah’s costume to life.
Magic Wheelchair suggests teams build a cardboard mock-up of the costume being built, and a PVC mock-up of the child’s wheelchair, so any issues can be worked out before production. It’s a great idea, but with barely a month to create their mini-Max-D, the SOLIDWORKS team forwent the cardboard and instead stuck with what they know best: CAD. “We’ve made a lot of progress in the short time,” said Annie Cheung. “And a lot of [the progress] has benefited from the fact that we’ve done more virtual prototyping in SOLIDWORKS to see what the problems are…SOLIDWORKS is helping us to cut down a lot of trial and error.” Using SOLIDWORKS, the build team was able to go straight from design to production.
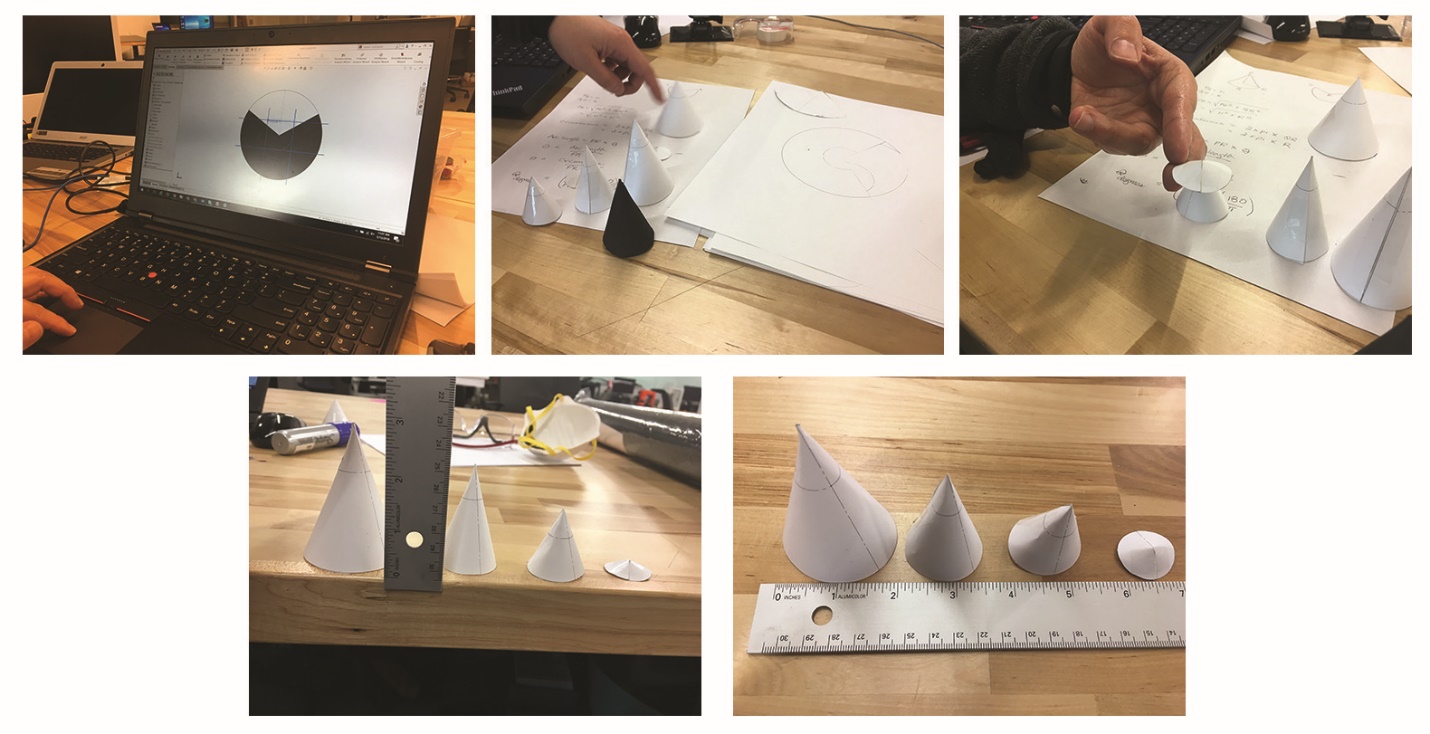
As the detail work on the mini-Max-D comes closer to fruition, the discussion over bought vs. printed became more pertinent. For pieces like the mechanism that connects the costume’s tires to the motor that will move them, do you spend money on specific, hard to find ball bearings, or just print them in the lab? Do you use the connecting PVC pipes that are already bought and try to finagle those to work with the chassis design and casters, or cut out the middle man and print custom connecting parts? Do you purchase Styrofoam cones to imitates spikes and rivets, or do you cut already purchased foam to save on time and testing? As the deadline draws near, more and more custom parts are being fabricated.
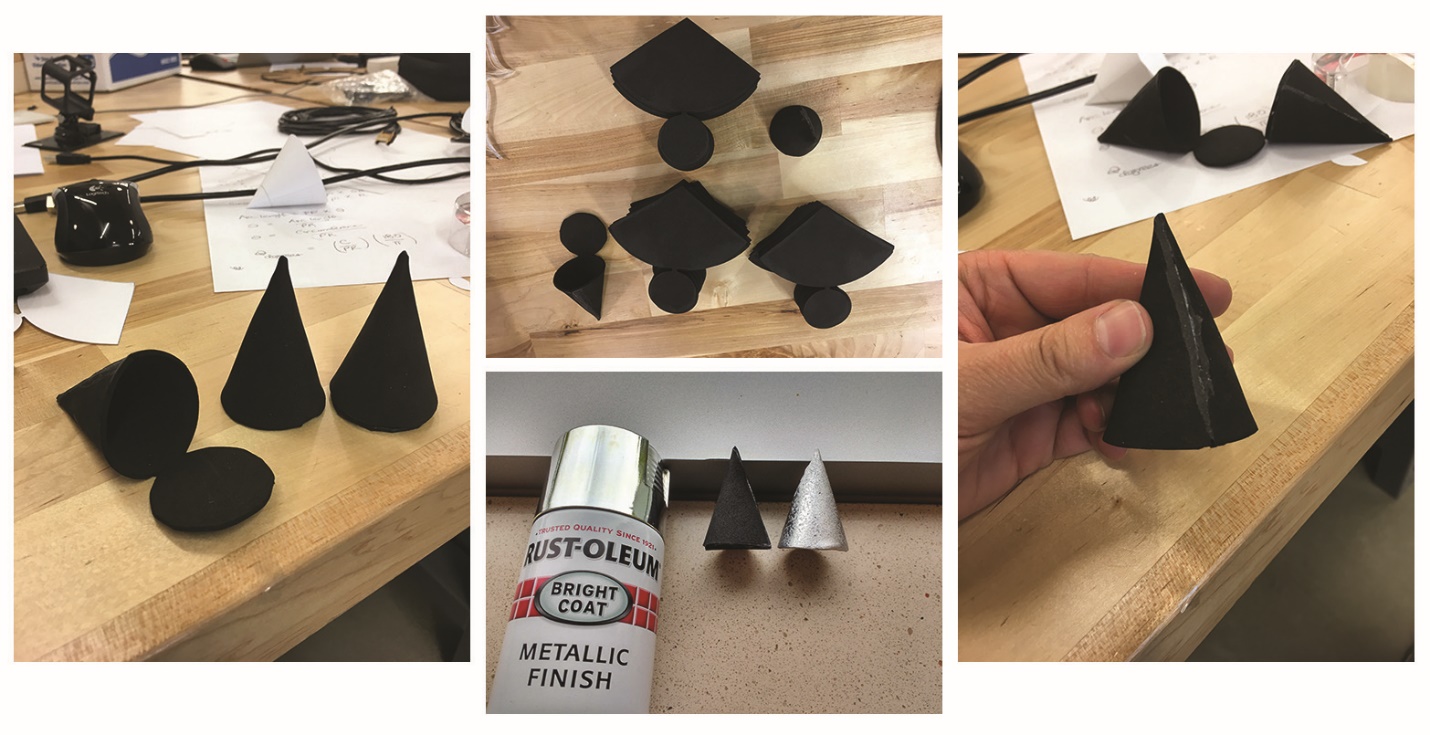
Take the “spikes” and “rivets.” There was a lot of back and forth on the Magic Wheelchair Slack channel over what size the “spikes” should be—again, the team is going all out for scale. But the actuality of a premade Styrofoam cone, that then needs to be shaped, cut, tested for prime, paint, and adhesive, led Annie to some geometry. She created paper cone prototypes to show the team what the best to-scale “spikes” and “rivets” would look like, then created a cut pattern in SOLIDWORKS what would allow the team to not only use material they already had, but also provide flexibility when attaching the “spikes” to the car body. The body of the mini-Max-D has angles and curve to it, and instead of cutting and sanding pre-made Styrofoam cones into submission, the team has flexible foam “spikes” ready to be placed wherever they need to go.
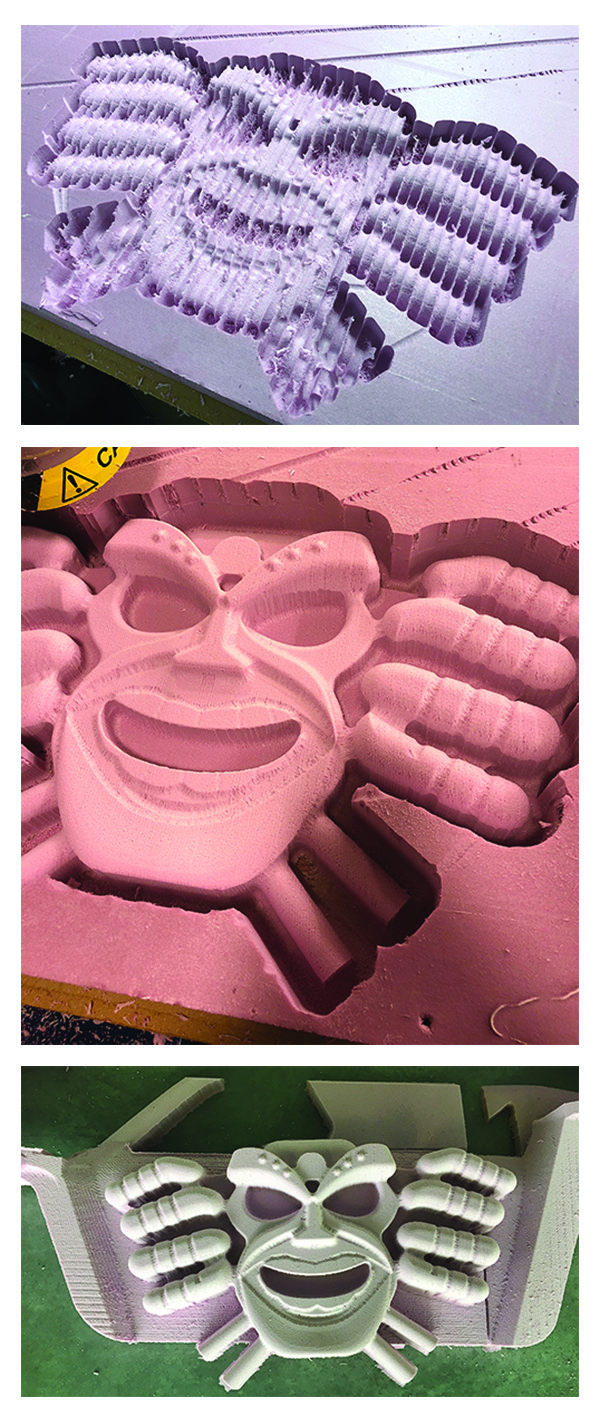
Max-D face progress
One of the details that had to be made via machining was Max-D’s face. This iconic visage is found on both sides of original truck, and as it came to life on the Shop Bot, the build seemed that much closer to making Jonah’s dreams come true. Albert Hernandez ran the face through the Shop Bot with a ½” bit, and rather than risk any issues by passing over the face again with a ¼” bit, the team will do the rest of the face details by hand.
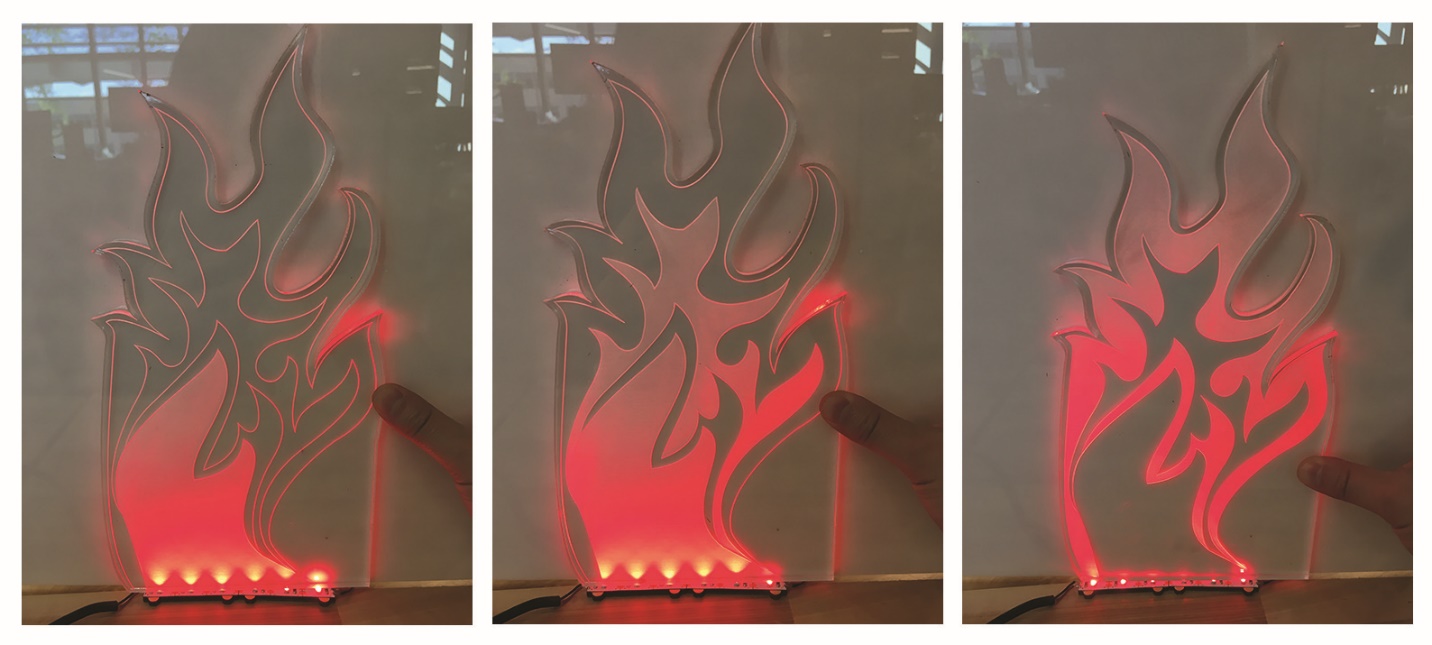
It’s been a while since we’ve checked on the mini-Max-D flames, and there is some news to report! Testing for the flame effect is in full swing, and the team is tossing linear regulators for switching regulars—they don’t want the lights to get too hot! The plan is to have LEDs all over the mini-Max-D: flames on the sides of the car, lights on the dashboard and in the interior where Jonah will sit, headlights and taillights, undercarriage lights, and lights on the faces. Regulating the currents and the placement of wires and the power source is at the forefront of the team’s minds.
The details for the costume are all coming together, and the build team is moving at a brisk, exciting pace. Team members are in and out of the 3DEXPERIENCE Lab and the airplane hangar every day, at all hours. The details are starting to pop, and next it’s hard coating, priming, painting, and putting it all together.
Help support Magic Wheelchair and amazing kiddos like Jonah!
SOLIDWORKS is working hard to make Jonah’s dreams come true, and helping the non-profit Magic Wheelchair achieve its goal of providing kids in wheelchairs with epic costumes. SOLIDWORKS is funding Jonah’s costume build in its entirety, but we invite all our readers to support Magic Wheelchair in Jonah’s name! If you visit this classy.org page, you can donate directly to Magic Wheelchair and help support them and all the lives they touch with their great work. Stayed tuned for more updates on this exciting build and always remember to keep on (monster) truckin’!
SOLIDWORKS is partnering with the Magic Wheelchair to create an over-the-top costume for a child in a wheelchair. According to their mission statement, “Magic Wheelchair builds epic costumes for kiddos in wheelchairs — at no cost to families.” Keep On (Monster) Truckin’ is an ongoing series dedicated to updating our readers on the current project’s progress.
Read about Jonah’s costume from the beginning!
Thank you to all who support our team, including Magic Wheelchair, Monster Jam, Permobil, and MLC CAD.