Engineering a Craft Beer Revolution with Phillips Brewing
Phillips Brewing and Malting Company is a small-batch craft brewery in Victoria, British Columbia producing amazing beers since 2001. Known for crafting a wide variety of brews to satisfy any palate, Phillips is a standout example of the global independent brewing revival. From the moment you check out its colorful website and peruse its unique offerings, such as Space Goat (dry-hopped oat pale ale) and Electric Unicorn (white IPA), you know this isn’t a 1990s craft beer.
While it’s clear Phillips conveys a fun attitude, the company is very serious about crafting quality beer. David Gilmour, maintenance engineer at Phillips, is part of the team responsible for ensuring that brewing equipment is performing properly and churning out a consistent, quality product. A lot of engineering work goes into keeping the taps flowing and customers satisfied; and SOLIDWORKS is among the tools used by Phillips to make its brewing magic happen.
Gilmour has been working in the maintenance department at Phillips for the past two years. He and his team perform routine upkeep and also design equipment related to all aspects of the beer-making process, from brewing to packaging. “Technology plays a large role in almost all aspects of the brewing process,” said Gilmour. “Many of the steps that are involved in the process are automated and require precise control, so being able to design equipment specific to our needs is very important.”
This automation process relies on a Swiss watch-level of precision, adding more weight to Gilmour and his team’s work on maintaining brewing technology. “We employ a fully automated brewhouse, so once a recipe is dialed in, the process can be completed using equipment and instrumentation, which allows for very precise brewing,” stated Gilmour. “In the brewhouse, automated systems communicate accurate temperatures and times to the brewers, thereby allowing for accurate control of each brew. The use of automation on the packaging line lets us track the number of bottles and cans that make it through our facility and helps us identify areas that can be made more efficient, increasing productivity on the line.”
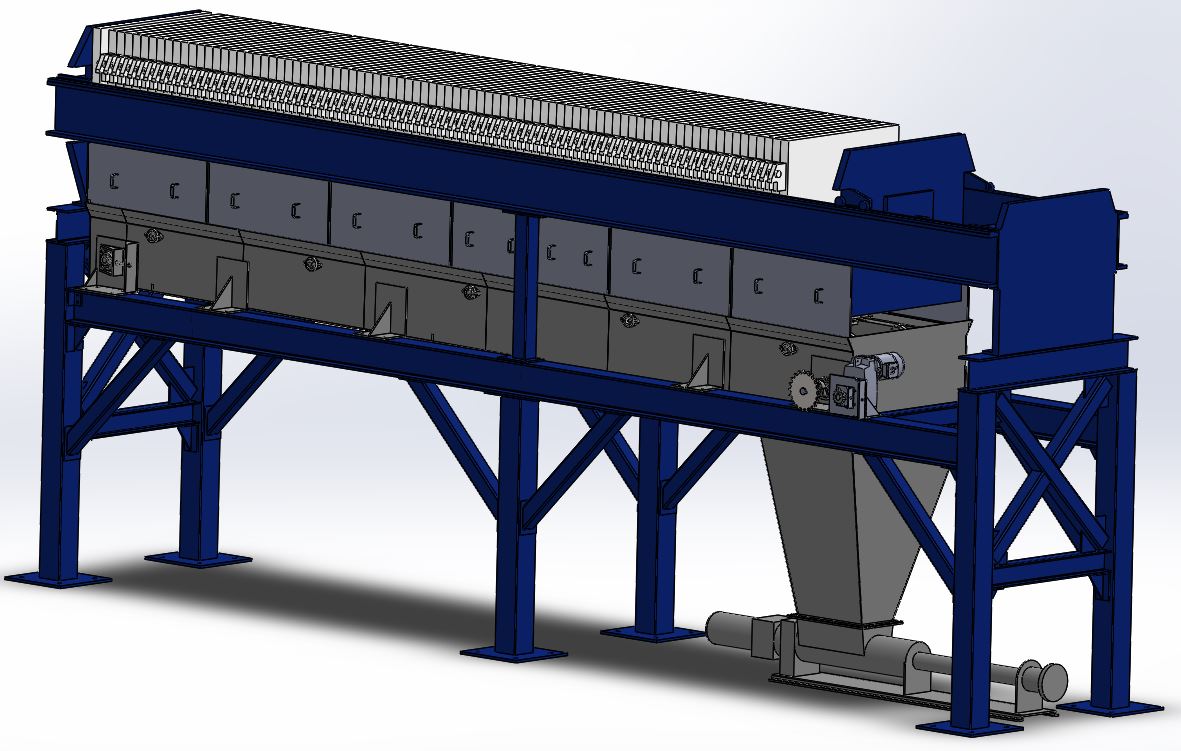
After that quick introduction to the Phillips brewery, it’s clear that no two brewers are the same. Craft brewers, like Phillips, have unique needs specific to their product that might not fit with other craft brewers – never mind macro brewers. Essentially, one size does not fit all in brewing. As Gilmour attests, the ability to quickly design custom parts is critical to maintaining old equipment and guaranteeing efficient brewing processes.
“Since we are a small brewery growing rapidly, we have multiple projects happening all the time,” Gilmour said. “We are in the final stages of installing a new brewhouse, and I utilized SOLIDWORKS in many ways through the installation process. A 3D model of the brewery was used to layout vessels, equipment and plumbing to ensure an efficient workspace. Our brewery uses new and old equipment and it can be difficult to find parts for some of the older equipment in use. I have utilized SOLIDWORKS to design smaller parts and pieces for this machinery to have it fabricated locally.”
While designing, Gilmour often takes advantage of assembly, sheet metal and weldment features, “one of the features of SOLIDWORKS that I think make it stand out from other CAD packages is the ability to efficiently create parts within an assembly,” said Gilmour. “This is a feature that I use to ensure the part I am designing is the perfect size and shape to avoid collision and keep costs down. I also use sheet metal and weldment features quite regularly to create parts with complex bends and welded joints. In previous projects I have used the extensive surfacing package in SOLIDWORKS to create molds for composite manufacturing as well.”
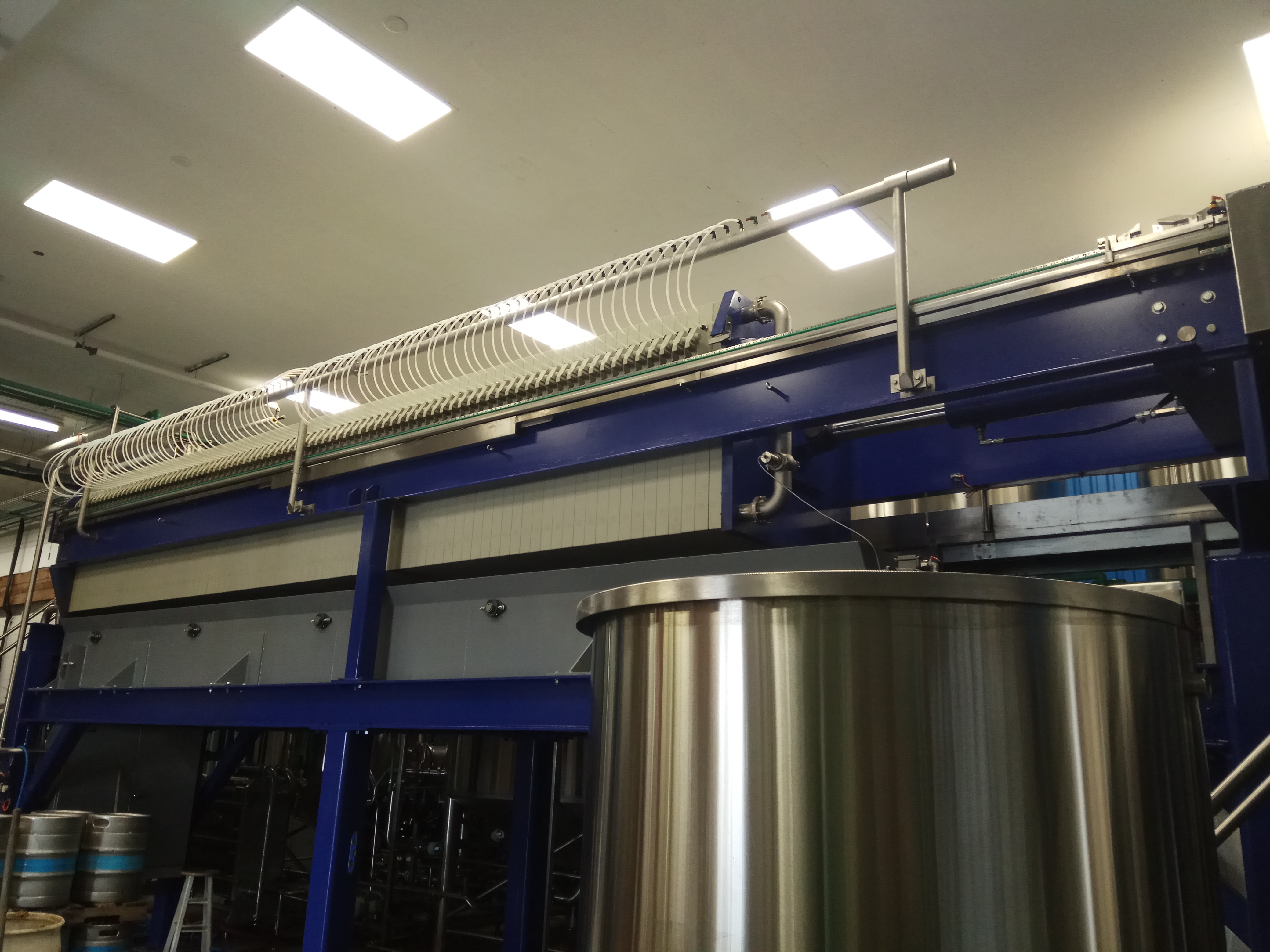
In addition to designing smaller parts for older machinery, Gilmour is using 3D CAD on larger projects. “Right now I am in the testing phase of a large piece of equipment that I designed using SOLIDWORKS,” Gilmour said. “Once the malted barley is boiled to remove all of the sugars and enzymes used in brewing the spent grain must be removed from the wort, the sugary liquid that will eventually become beer. To perform this task we use a mash filter, which is a series of filter plates and air bladders that remove as much of the wort out of the grain as possible. I designed a frame for the press that puts it at a height accessible to the brewers, about 12 feet off the ground, and a large drag conveyor to carry the grain to a pump. I used a 3D model of the brewery I created in SOLIDWORKS to lay out the piping system that carries the grain from the pump to a silo 200 feet away that holds the grain, which is then used by local farmers to feed their livestock.” It’s the brewing circle of life with engineering ingenuity and SOLIDWORKS.
While Gilmour understands that humans play the most important role in crafting a great beer, technology continues to facilitate better brewing processes. “I think that advances in engineering technology will allow for the increase of quality assurance and precise control over all aspects of the beer making process,” Gilmour said. “Advances in design technology are giving craft breweries like Phillips the ability to bring engineering design in house, which helps create specific equipment for the needs of the brewery.”