MBD Implementation 10 DOs and 10 DON’Ts – Don’t Be Confined to Design Department Alone
Model-Based Definition (MBD) often starts with Design department, but to fully realize its value, many other departments and teams are needed, such as manufacturing, inspection, purchasing, and supply chain, which is partly why this initiative must be driven from top down. This blog will look into how to take your MBD initiative beyond Design department.
Design teams often create MBD data, but that’s just one side of the coin. The other side is data consumption. In order to enable 3D data flow and reduce 2D drawings, the MBD implementation team and designers need to understand how design data is consumed today and how it will be in the future. Only through patient listening, negotiation, and collaboration can constructive progress be made. Simply throwing data over the wall or pounding with a big hammer wouldn’t cut it. Remember, after all, daily production has to keep running to bring food to the table.
Here is an example of working with a supply chain. A medical device company in U.S. requires its design team to clearly understand its machine shop’s capabilities: hardware, software, expertise, and so on. It comes down to a common sense: know your audience.
- Some shops can read their native SOLIDWORKS formats directly. Great! In-house Design only defines critical-to-function dimensions and tolerances. These shops can always go back to native models for nominal dimensions if necessary;
- Other shops may be still model-based, but can’t read native SOLIDWORKS models, so prefer 3D PDF with fully defined dimensions and tolerance as explicit specifications;
- There are also shops who can’t live without 2D drawings, which is fine too. In this case designers need to generate 2D drawings to keep the job rate and cycle time within control.
- For new suppliers, they evaluate the capabilities thoroughly and provide design data formats accordingly.
As to in-house manufacturing, GE’s on-demand “pseudo drawing” below, presented by Dr. Prashant Kulkarni, is a classic example of accommodating downstream needs. Engineering managers told the product design team, “You can create and release models, but all of our engineers are used to 2D drawings. You have to give us some kind of 2D print, although it may not be released to PLM.” Therefore, this middle-ground pseudo drawing takes every PMI view and puts one view per sheet into a drawing surrounded with a border.
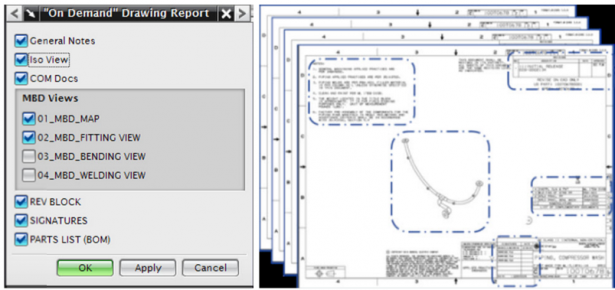
Not every story worked out so well. If Design just throws data over the fence to suppliers without proper support, the consequences could be painful. Many times, suppliers had to take wild guesses and recreate 2D drawings, which led to higher costs and misinterpretations. Some times, customers and suppliers went to court over design disputes and business impact. There are also shops who lost money to finish one order and refused to take similar orders in the future.
If we can properly facilitate MBD data flow across production procedures, however, the benefits can be tremendous. A typical application is for machine-readable PMI to drive Coordinate Measuring Machine (CMM) for Quality Inspection as shown in the screenshot below. Here CMM programming is done automatically by analyzing SOLIDWORKS MBD dimensions and tolerances (Source: CheckMate by Origin International, a fully integrated SOLIDWORKS partner product). Hours are saved in CMM path planning alone. More details on this can be found in this SOLIDWORKS MBD and CMM Programming webinar. We will dive into machine-readable PMI in a future blog post.
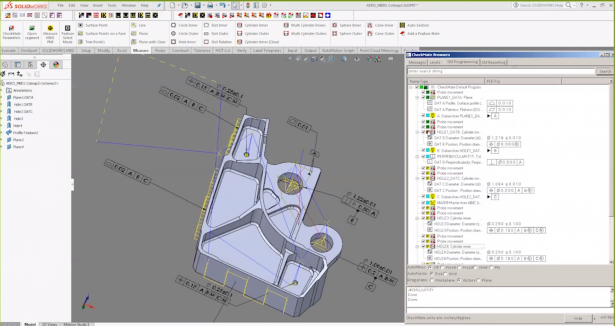
This post concludes the first chapter of this MBD Implementation 10 Dos and 10 Don’ts series regarding People aspect. The next blog will start the Process chapter. Thank you for reading. To learn more about SOLIDWORKS MBD, please visit its product page. Also welcome to discuss with me at Twitter (@OboeWu) or LinkedIn (OboeWu).