F1 and the cutting edge CAD future of racing
Motorsports are some of the most exhilarating events in the world, as drivers and teams put themselves to the test, pushing the limits of engineering and the human psyche for hours at a time.
The leader of the pack here is unquestionably Formula 1, the centre of development for the automotive industry and the place where some of the best drivers in the world race some of the fastest machines on four wheels. Of course, continually developing cutting edge vehicles and staying ahead of the competition requires constant assessment of the most advanced design and manufacturing processes currently available.
This means considering cutting edge computer design tools like SOLIDWORKS.
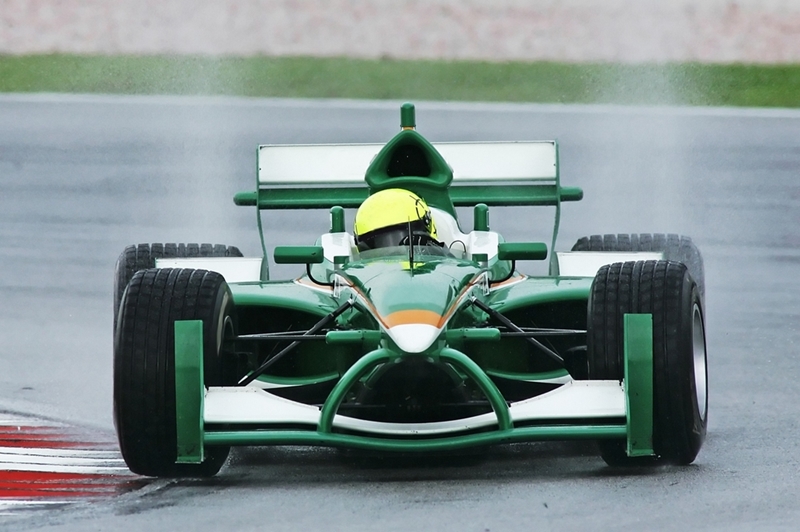
An industry on the bleeding edge
Formula 1 cars change every year, in line with frequent updates to regulation. Rules surrounding the width of spoilers, the distance from the vehicle to the ground and engine size mean teams have to consistently update and redesign vehicles, all while advancing performance standards.
Such gruelling requirements have led to some amazing innovations, according to Red Bull, like the Mass Damper developed by Renault in 2005. This was a technology that absorbed the shock of a bump and sent it into the chassis. Or, there's the FW26, which featured a nose cone never before seen in the sport. Instead of the usual point, the engineering team opted for a wide and flat nose designed to allow better airflow to the lower splitter.
See how CAD software could prove useful here? The need to rapidly innovate and test new ideas is what tools like SOLIDWORKS are all about. For example, such programs could allow engineers to mock up a new splitter, stress test it in realistic conditions, showcase it to the rest of the team and then finally send it off for manufacturing.
There's a reason teams like Red Bull have started to incorporate CAD software into their Formula 1 development process.
Red Bull leading the charge
Most of the major Formula 1 teams are forced to innovate to stay in the competition, but there are undeniably those that have an eye on the future more than others. One of these teams is Red Bull.
This is a team that's constantly looking forward, assessing innovations today that could potentially lead to a win on the track tomorrow. Obviously, new approaches to design and manufacturing are essential.
"3DP is definitely the future of F1," a Red Bull spokesperson explained to TrustedReviews.com. "We could get to a point where we can print out a new front wing at the track if we've damaged one."
iframe.twitter-tweet.twitter-tweet-rendered{ width: 99%!important;}
Who said #F1 was done for 2015? We have some tyre-frying action in Perth next weekend! https://t.co/zK9WvUVntP pic.twitter.com/5lpwJoBIs7
— Red Bull Racing (@redbullracing) December 5, 2015
Right now, however, there's little chance of putting such components on a track vehicle. While it's true current design tools and printers are able to produce tough finished products, F1 vehicles withstand tremendous pressures. This is the reason why Red Bull is only able to use the techniques to develop small test vehicles – those cars that won't be required to endure the rigours of a race weekend.
"The compounds used for filaments, even at 60 per cent scale prototype level, cannot withstand the pressure endured by the carbonite used on the actual racing car," 3D Printing Industry wrote.
Lotus is another team pushing the boundaries of design with CAD software and 3D printing. Gigaom reported in 2013 that Lotus uses the technologies to test thousands of parts prior to the race. What's more, components like the head protection bar are designed using computer tools and then printed using titanium powder for maximum durability.
There's definitely a future for new methods of design and manufacturing in Formula 1, and more teams are likely to join the fray in the very near future. However, better tools and more durable and even lighter composites are going to be essential if the technology really entrenches itself in this fast-paced sport.