Perform Abaqus High-End Simulations from Home with Structural Mechanics Engineer
With the new SIMULIAworks product family on the cloud-based 3DEXPERIENCE® platform, we keep expanding the simulation possibilities for SOLIDWORKS® users to solve any finite element analysis (FEA) problem with confidence. The new (and most powerful) member of the family is Structural Mechanics Engineer.
In this post, and especially if you are a SOLIDWORKS Simulation Premium user working from home, we’ll try to explain what Structural Mechanics Engineer can do for you by answering three simple questions.
- In these difficult times, how do you manage working from home on projects that involve simulation?
Problem: Sharing licenses on a network can be convenient; however, it can be challenging working from home as it might require a VPN connection that slows down your local computer.
Solution: The 3DEXPERIENCE platform is a software as a service (SaaS) subscription model that gives you the flexibility to rent a license for 3-months or one year without having to manage software installs or worry about hardware upgrades.
- Because it is cloud-based, you can access the simulation applications from home, at the office, or on the road. All you need is an internet connection and a web browser to access Structural Mechanics Engineer.
- No need to worry about choosing a cloud provider or having multiple contracts; it is all taken care of under the same SOLIDWORKS roof.
- The power of the platform allows you to exchange real-time information, share lightweight simulation results, chat with other team members, and conduct audio or video conversations.
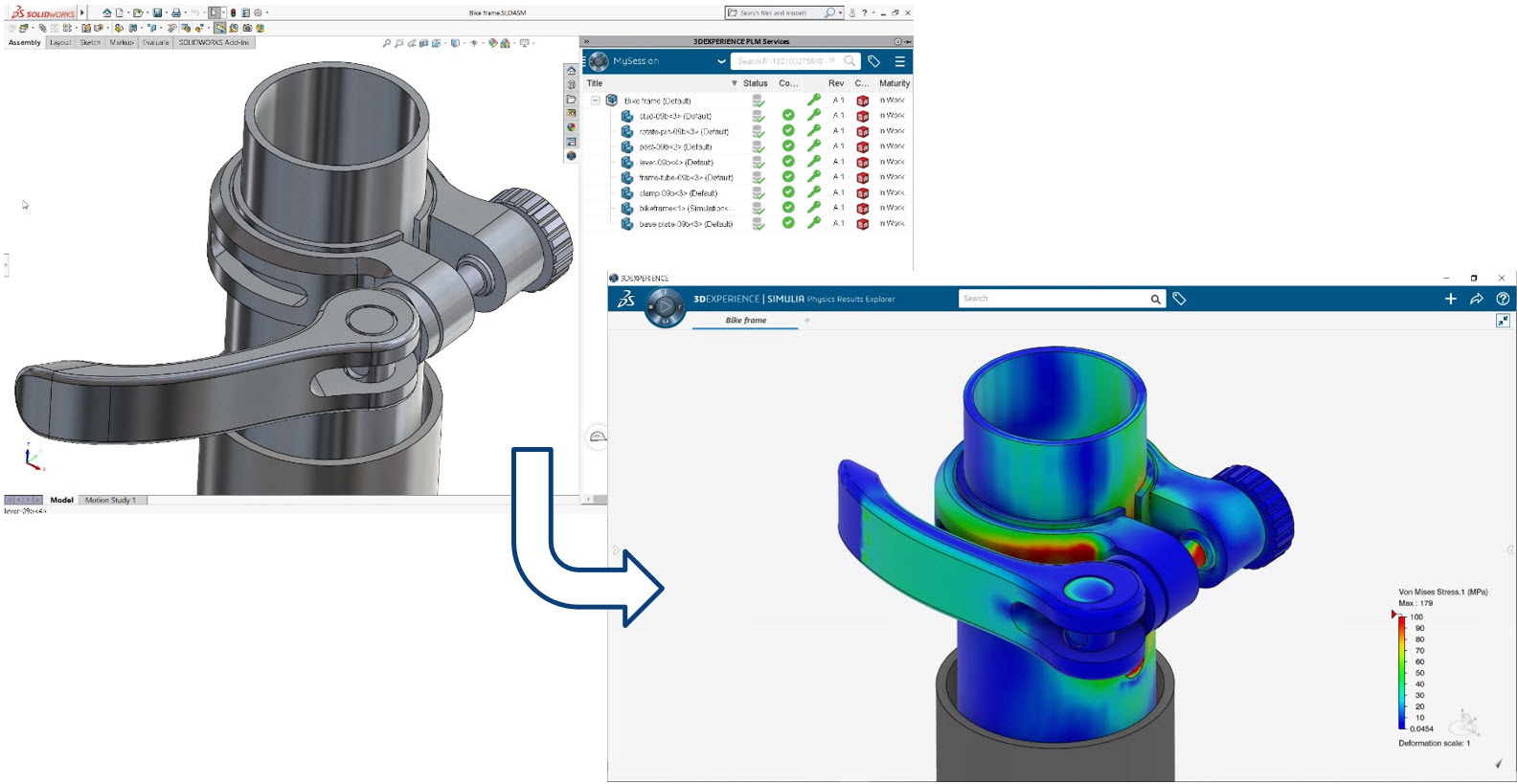
- Do you have enough software or hardware resources when your simulation becomes increasingly complex?
Problem: SOLIDWORKS Simulation Premium is an excellent and well-established FEA tool; embedded in SOLIDWORKS, you can enjoy super-fast design to simulation iterations. However, more complex simulations can be problematic when the solve doesn’t fully converge.
Solution: Structural Mechanics Engineer can handle the more complex jobs such as simultaneous nonlinear effects (low-speed static or high-speed dynamic events); contact with friction between different parts; and nonlinear material like hyper-elastic or other complex materials—even in scenarios with large displacement or large strain.
- There is continuity with your SOLIDWORKS data and processes with a connector that saves and converts CAD geometry (and soon simulation studies and materials) from SOLIDWORKS to the 3DEXPERIENCE platform. The nice part is the associativity and traceability of your data. For example, you can see in one simple graph (Image 2) the links between your SOLIDWORKS data and the simulation data on the platform.
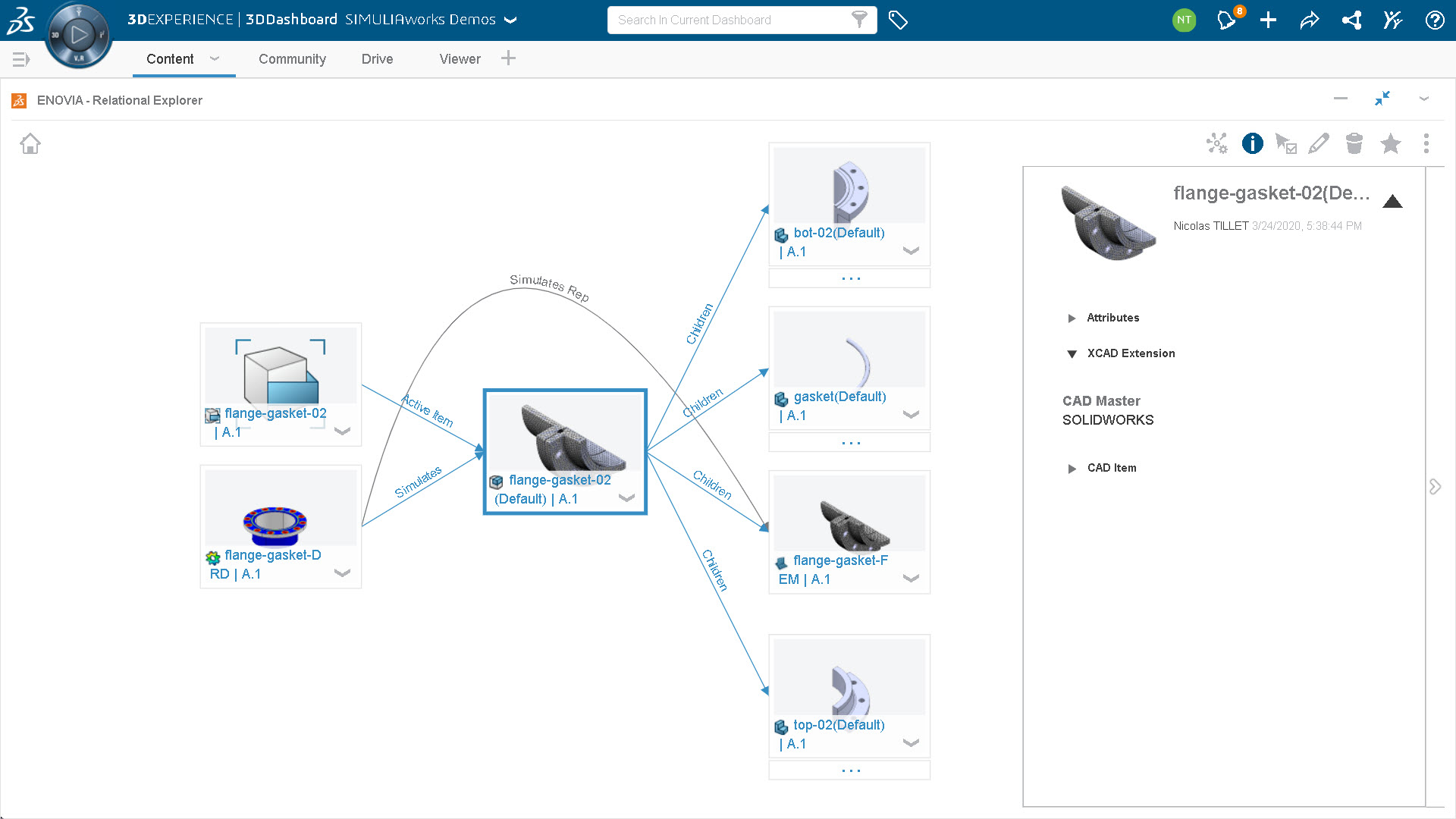
Structural Mechanics Engineer leverages the proven Abaqus/Implicit, Abaqus/Implicit Dynamic, and Abaqus/Explicit solvers so you can solve any structural problem—with confidence!
- Many simulation experts in the industry chose Abaqus as the standard tool for structural simulation.
- You can solve the most advanced problems: low-speed events like rubber gasket/rubber seal in compression, preloaded bolts, three-point bending with plasticity, metal forming, medium speed-events like snap-fit/snap-through, high-speed events like drop test or impact.
- A wide range of mesh element types (linear or quadratic) also helps you to handle complex problems easily and with accuracy (solid hexahedral bricks, surface quads, continuum shells, and more). Create high-quality meshes manually or automatically using a batch mode.
- Considering the right material inputs is critical for a successful and accurate simulation. Structural Mechanics Engineer offers a wide range of material models (hyper-elasticity, plasticity, viscoelasticity, creep, and much more). A unique application offers material calibration so you can easily fit material curves from test data into accurate material properties for your simulations.
- Run your simulation either locally on your desktop computer or remotely on the cloud so you can leverage more hardware, virtually, if you need to solve larger simulations that take more time and require more computer resources. The nice thing is that you can still work in SOLIDWORKS while the simulation is running on the cloud.
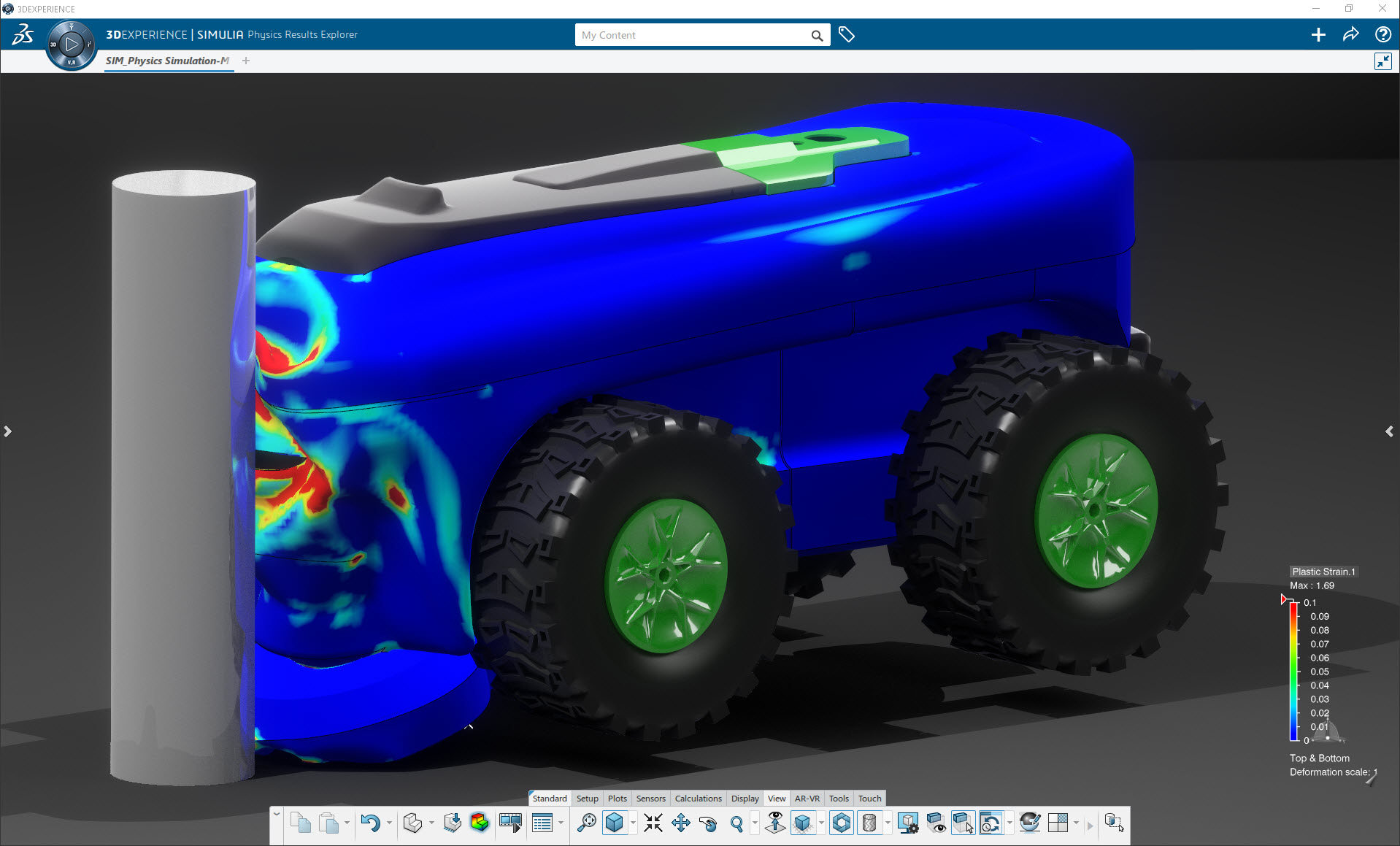
- Do your customers have particular requirements for the finite element analysis (FEA) tools you use?
Problem: Many industries (medical, high-tech, aerospace, automotive, and more) may require you to use specific FEA tools in your engineering project.
Solution: Many simulation experts use Abaqus technology for nonlinear structural simulation, which has been used for decades in the industry. Structural Mechanics Engineer relies on the same proven Abaqus technology. The following guides might be helpful when your clients request specific FEA tools. You can access them by clicking the links below and using your SOLIDWORKS ID to login:
- Abaqus Verification Guide: Contains many test cases that provide evidence that the implementation of the numerical model produces the expected results for one or several well-defined options in the code. The test cases are sufficiently small that they can be executed efficiently while producing results that can be compared to independently calculated solutions or experimental results.
- Abaqus Benchmarks Guide: Contains problems that provide evidence that the software can produce a result from a benchmark defined by an external body or institution such as International Association for the Engineering Modelling, Analysis, and Simulation (NAFEMS). The tests in this guide are sufficient to show accuracy and convergence compared to benchmark data.
- Abaqus Examples Problems Guide: Contains many solved examples from which users can learn how to run simulations involving nontrivial physics.
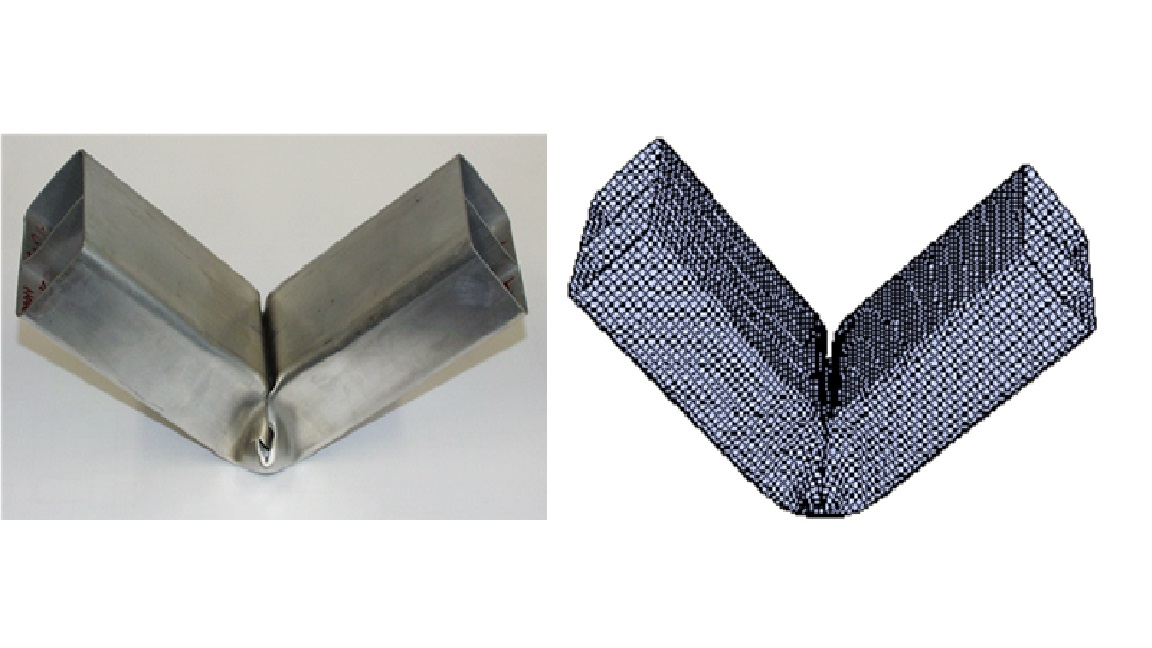
Structural Mechanics Engineer is a new, scalable, structural simulation solution for SOLIDWORKS users. You can access it from the office, at home, or on the road with an internet connection. Plus, SOLIDWORKS and Structural Mechanics Engineer are connected so that there is data continuity, associativity, and traceability. And when you are ready, you can easily share results with others, in real-time, with a web viewer.
If you have comments or questions, please consider making them below. For more information, please contact your local reseller.