What Is Supply Chain ERP?
A Supply Chain ERP system orchestrates and optimizes forecasting, pricing, procurement, sourcing, and inbound product quality levels across the many supplier relationships manufacturers have, providing real-time accounting and financial reporting of each transaction. Supply Chain ERP systems provide Electronic Data Interchange (EDI) integration support, inventory control and management, inventory and order-level financial reporting, distributed order management, warehouse and distribution reporting, and analytics and integrated asset tracking systems.
Defining Supply Chain ERP
Manufacturers are improving delivery performance, reducing purchasing and materials costs, and minimizing supplier risks by adopting integrated supply chain ERP systems. By combining the supply chain, production, accounting, and finance data in a single integrated supply chain ERP system, manufacturers can achieve greater control and visibility across their operations. For the first time, manufacturers can see the impact of the supply chain, sourcing, production, and quality management decisions on the financial performance of their businesses. Manufacturers are adopting integrated supply chain ERP systems to achieve higher levels of sustainability and lean manufacturing. Managing and leading a manufacturing business using an integrated supply chain ERP system ultimately delivers greater volume flexibility and market responsiveness.
Benefits of Supply Chain ERP Systems
Manufacturers relying on supply chain ERP systems are achieving the following results:
- A single system for managing all suppliers and knowing accounting and financial data in real-time based on inventory transactions
- More effectively managing all distribution channels as a single, unified system with visibility across each distributor network
- Improving the level of inventory turns and inventory management efficiency
- More accurate and real-time inventory management and cost control
- Improve sales effectiveness including upsells and cross-sells by having more products available for sale based on real-time supply chain visbility
- Improve product quality levels and compliance with greater traceability and visibility across the entire supply chain network
- Improve customer satisfaction by meeting delivery dates
- Achieve greater financial control over each distribution center
Lessons Learned From Global Interconnect
The lifeblood of any business is its supplier relationships, and the best-run supply chains are built on a solid foundation of trust. The results being achieved by Global Interconnect (GII) today, a worldwide provider of custom-engineered cable assemblies, connectors, and components, illustrates how supply chains integrated into ERP systems improve product quality by increasing supplier trust. GII is a global leader in the development of cables, connectors, and components for medical applications including electrosurgical tools and critical patient monitoring devices with zero failure requirements. Every manufacturers’ supply chain is unique, designed and modified over time to meet the changing demands of a business. Here are the challenges and results GII solved with an integrated supply chain ERP system:
- Counterfeit components, connectors, and assemblies make their way into plastics supply chains, representing a major risk to GII’s zero failure requirements. The threat existed of counterfeit products leaking into their supply chains when they were relying on a legacy MRP system to manage a broad base of suppliers across Asia. GII’s senior management team went as far as to source parts domestically to make sure they weren’t counterfeit and then shipped them to their supplier factories in Asia. Manual calculations of needed components based on finished assembly usage and inventory levels at the factory took valuable time away from production. Migrating to an integrated supply chain ERP system solved the problem, and today GII can enforce its quality standards across every supplier and factory.
- Manually collaborating with suppliers in locations several time zones away, including Hong Kong and China was taking hours out of every workday, making it more difficult to keep production schedules up to date. GII was finding that their manually-based approaches to collaborating with suppliers across the world were taking a significant amount of time each day. Once an integrated supply chain ERP system was in place, supplier management became much easier. Forecasts are now shared in real-time, and quality by shipment and supplier is measured.
- Accounting for inventory with a manual backflush process was the only way to get an accurate inventory figure. It would take on average three hours of warehouse management analysts’ time to complete an initial inventory. Their results would then be crosschecked by several members of the team. Further slowing down inventory reconciliation was the problem of the legacy accounting application not integrating with purchasing, so invoices ready to be paid would require manual approval as well.
- Having to manually enter invoices into their accounting system, then performing check runs turned into major delays paying suppliers. Incoming receipt of materials was being tracked and process entirely using a manual process. First, receiving would bring in the packing slip, match it with the purchase order, approve it and give it to accounting. But such a practice required someone to manually enter the invoice into their accounting system, run it, and then perform their check run.
How GII Benefits From An Integrated Supply Chain
GII is an example of how integrated supply chain ERP systems are making solid contributions to manufacturers who rely on complex supply chains. By replacing manual processes with a system that integrates accounting, purchasing, sales orders and inventory in a single system, GII was able to achieve the following: growing sales by 50% within four years, increased total productivity by 25% and reduced time spent on accounting and received by 50%. They were also able to improve medical device compliance and now have an entirely automated approach to generating shipping documents.
Conclusion
The more challenging the competitive and compliance demands in any industry, the more crucial an integrated supply chain becomes. GII’s experiences illustrate how any manufacturers can get bogged down with manual workflows that are prone to error and are, at the very least, a waste of valuable time. By adopting an integrated supply chain ERP system, manufacturers can remove the roadblocks in the way of achieving higher product quality and build stronger trust with suppliers.
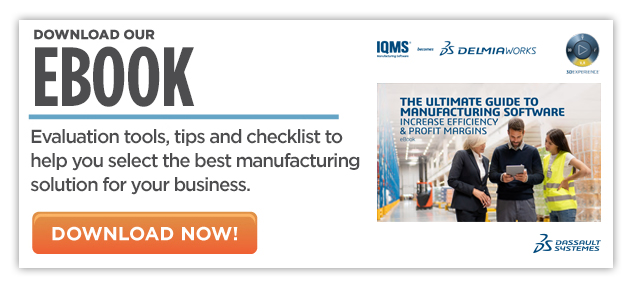