The Growing Reliance on Traceability in Manufacturing Supply Chains
Bottom Line: The heightened priority on health & safety is leading to a renaissance of traceability in manufacturing across many industry sectors as every business strives to keep its employees, customers, and suppliers safe.
Manufacturers are racing to digitally transform their supply chains to gain needed insights to reduce risks to their employees, customers, partners, and the business itself. Acumen Research & Consulting, an advisory firm specializing in industry and vertical market research, predicts global demand for manufacturing traceability, including track and trace software, will soar through 2026. Acumen is forecasting spending on track and trace systems will reach $7.2B by 2026, achieving an 18% Compound Annual Growth Rate (CAGR).
Reliance on Traceability in Manufacturing Is Growing
The pandemic accelerated digital transformation across manufacturing supply chains faster than the most convincing business case ever could. Add to that the risks, costs, fines, and logistical challenges of handling a recall, and the growing popularity of track-and-trace systems becomes clear. According to a recent National Association of Manufacturers’ survey, manufacturers waste over $275B a year on unnecessary product recalls. These losses to recalls could have been averted if they had more effective traceability systems in place, with tracking and tracing being considered table-stakes or a must-have in all manufacturing industries today.
The following are the key reasons why manufacturers’ reliance on manufacturing supply chain traceability is leading to a tracking and tracking renaissance:
- Troubleshooting how a defective part was first introduced into production can save product lifecycles’ revenue and margins that otherwise may have been lost. Track-and-trace gives manufacturers the visibility they need to find the origination point of a defective product immediately. Tracking and tracing which suppliers’ lot number or container delivered the defective part as quickly as possible save valuable time and the high costs of a recall or, at the very least, a product retrofit in the field.
- Supply chain track-and-traceability is foundational to manufacturers’ quality management and compliance strategies. Troubleshooting supplier quality problems is integral to staying in compliance with aerospace & defense, automotive, food & beverage, plastics, medical device manufacturing, and pharmaceutical regulatory requirements. As the pandemic and trade pressures are forcing manufacturers to reconfigure their supply chains overnight, track and traceability deliver the data needed in real-time to stay in compliance and continually achieve higher product quality. Medical device manufacturers who excel at complying with the U.S. Food & Drug Administration (FDA) 21 CFR Part 820 requirement gain the added benefits of achieving new levels of lean manufacturing in the process. Track-and-traceability is proving invaluable to aerospace and defense manufacturers. To successfully sell products in their industry, they need to prove compliance with the International Traffic in Arms Regulations (ITAR) standard, Defense Contract Audit Agency (DCAA), and AS 9100 Rev. C standards. Tracking and tracing materials are so important it’s considered a competitive advantage if aerospace and defense manufacturers do it well.
- A well-managed track-and-trace system helps reduce inventory shrinkage by providing greater visibility and control across supply chains. A state-of-the-art track-and-trace system can differentiate between inbound shipments’ batch, lot, and container level assignments of materials. Most advanced track-and-trace systems rely on advanced sensors to gain greater knowledge of each shipment’s condition. RFID and IoT sensors are now becoming more commonplace across manufacturing. Walmart ran a pilot to see how RFID could streamline a distribution center’s track-and-trace performance and improved efficiency by 16 times over manual methods.
- Traceability in manufacturing also improves production scheduling accuracy and efficiency by providing greater visibility into assembly, part & component inventory. Providing DELMIAwork’s MES system with real-time updates on suppliers’ assembly, part, and component inventories help to keep production on schedule. Immediate insights into inventory can also help manufacturers get more done in less time. Many manufacturers have the goal of offering short-notice production runs to their best customers. Track-and-trace helps to make that happen.
- Collaborate and serve customers with real-time track-and-trace data they need to know. DELMIAwork’s track-and-trace solution is specifically designed to share the most valuable data customers need to meet FDA and quality audits. It’s possible for customers to instantly print detailed tracking reports that are often provided in customer and regulatory agency audits. Relying on an automated approach to tracking and tracing saves valuable time on the shop floor by automating reporting, so quality or production engineering doesn’t have to do the reports manually.
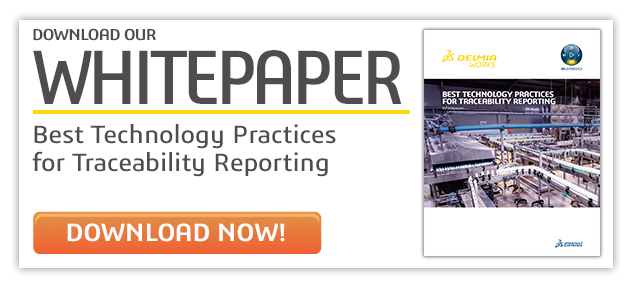