Sustainable Manufacturing is the New Key to Profitability
Just a few years ago, sustainability in manufacturing was seen as a nice-to-have. Today, sustainable manufacturing is becoming a critical factor in a manufacturer’s ability to compete and maximize profitability. This was driven home to me in a recent discussion with a Gartner analyst. She noted that the research firm used to give sustainability a weight of 10% in scoring the top 25 manufacturing companies; this year the weight is 15%, and next year, it will be 20%.
Gartner is quick to note that it is not practical for manufacturers to adopt all possible sustainability measures. Instead, the analysts there recommend that executives focus on what is most important to their companies and to customers, partners, and other stakeholders. From talking with our customers and other manufacturers, the three most common drivers are cost savings, customer demands, and new business opportunities. Let’s look a little closer at these.
Sustainable Manufacturing Initiatives that Drive Cost Savings
Two of the expenses that most often impact manufacturers are energy consumption and raw materials. According to the U.S. Department of Energy (DOE), the United States spends over $200 billion dollars per year to power manufacturing plants. To help cut those costs, the DOE has partnered with the National Association of Manufacturers (NAM) to create a Sustainability in Manufacturing partnership. Supported by the DOES’s Better Plants Program, the partnership is focused on helping U.S. manufacturers drive energy productivity improvements and accelerate adoption of energy-efficient technologies.
In September 2019, the DOE reported that its Better Plants and Better Building partners have cumulatively saved $6.7 billion in energy costs. These partners have more than 3,200 facilities and represent roughly 12% of the U.S. manufacturing energy footprint. For those companies, the energy cost reductions translate into better bottom-line performance, as well as the opportunity to compete on price without sacrificing quality.
Meanwhile, the drive to cut unnecessary costs is driving innovation in sustainability. One of my favorite customer examples is Comar, a manufacturer specializing in packaging solutions for markets that demand quality, service and creativity. The company regularly works with customers and partners to reduce, reuse and recycle materials. Recently, Comar collaborated with an injection stretch flow manufacturer to create a bottle design optimized for nutritional supplement gummies, which minimized the resin required. Not only did this cut waste; it also reduced the associated resin costs.
Customer Demands
A growing number of industries are facing demands to demonstrate their commitment to responsible environmental practices—whether due to consumer awareness, government mandates, or other market influences. The automotive industry is a good case in point. Similar to the way automakers drove the adoption of quality initiatives through their supplier networks a few years ago, they are now asking suppliers to demonstrate that they have environmental certifications. Most often, this means complying with ISO 14001, the international standard that specifies requirements for an effective environmental management system (EMS).
Our customer, Somaschini North America LLC, understands ISO 14001 requirements first-hand as a manufacturer of high-precision, high-volume steel timing gears for some of the world’s leading commercial automotive brands, including Detroit Diesel and Daimler Germany. To meet the requirements of these customers and others, it complies with ISO 14001 and has been certified as a zero discharge facility.
Complying with ISO 14001 has represented a serious investment by Somaschini. All recyclable materials, including the steel and aluminum turning waste from the machining process, go to a recycling facility. And it has everything—from trash to batteries and lightbulbs—captured and hauled offsite by an environmental company. Additionally, the company ensures that no wastewater beyond normal sink and toilet sewage goes into the city’s water supply. At the same time, these investments in ISO 14001 compliance give Somaschini a competitive advantage over other suppliers in winning business from commercial automotive OEMs.
New Business Opportunities
Practicing sustainable manufacturing can lead to business opportunities. It may take the form of ensuring customer loyalty as Comar has done by producing a bottle that requires less resin. Or, it may lead to serving new customers and markets altogether. I ran into a great example of the latter at a recent trade show where I met a manufacturer that produces custom pallets for shipping auto parts.
The manufacturer explained that many automotive companies in the U.S. and Europe demand certain colors for their pallets, either for branding purposes or for color-coding. Producing flawlessly colored pallets to spec often means using virgin materials. By contrast, many auto parts companies in China and Vietnam simply want to purchase the least expensive pallets available. For these customers, the manufacturer is able to use regrind to produce streaky but fully functional pallets, which are backed by a 10-year guarantee. The company’s sales rep makes money selling these lower-cost, sustainably produced, “flawed” heavy-duty industrial pallets.
Resources for Kick Starting Sustainable Manufacturing Initiatives
Even as sustainability moves toward becoming a business imparity, many manufacturers have yet to begin evaluating how they can implement sustainable practices. There are two organizations that offer guidelines and resources to help manufacturing firms of all sizes get started.
The DOE Better Plants program discussed earlier offers manufacturers a range of partner solutions and program resources to improve energy efficiency and competitiveness in the industrial sector, saving money in the process. These can be found at https://betterbuildingssolutioncenter.energy.gov/better-plants.
The Organisation for Economic Co-operation and Development (OECD) is an international non-profit that has produced the OECD Sustainable Manufacturing Toolkit. This Toolkit provides a set of internationally applicable, common and comparable indicators to measure the environmental performance of manufacturing facilities in any business size, sector or country. It includes a step-by-step Start-up Guide and a Web Portal with technical guidance on measurement and relevant links. The Toolkit is available at https://www.oecd.org/innovation/green/toolkit/#d.en.192438.
When putting sustainability processes into practice, manufacturers can often take advantage of their enterprise resource planning (ERP) and manufacturing execution system (MES) software to automate monitoring and management.
A great example is our customer, Revere Packaging, which balances superior products and customer service with its commitment to serving the environmental needs of current and future generations. To reduce its ecological footprint, the company purchases recycled raw materials and produces fully-recyclable plastic and aluminum packaging. In deploying our software, Revere Packaging aims to gain a better understanding of costing versus the sell price of its eco-friendly products in addition to improving overall production performance and optimizing its ability to schedule production more efficiently across four facilities.
With the resources available, now is the time for more manufacturers to start looking at how they can implement sustainability initiatives to grow their business, drive customer acquisition and loyalty, and increase the bottom line.
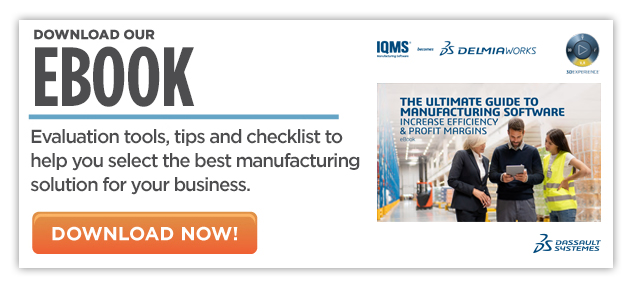