Why 2021 Will Be A Breakout Year For Sustainable Manufacturing
Bottom Line: In 2021 and beyond, customers are voting with their dollars for the manufacturers who excel at sustainable manufacturing and make a positive contribution to the environment, dominating B2B supply chains and B2C purchasing decisions.
From automotive components and parts manufacturing to producing recyclable plastics packaging and industrial products, achieve sustainable manufacturing excellence is proving to be a sure catalyst for driving greater revenue, reducing costs while making a positive contribution to the environment.
Consider the following data points that signal 2021 being a breakout year for sustainability:
- To sell to BMW, Ford, GM, Mercedes-Benz, Toyota, and many other tier-1 automotive manufacturers, suppliers need to excel at the ISO 14001 standard, a prescriptive framework that provides manufacturers with guidance on how to excel at environmental operations and to report results.
- 71.9% of all North American manufacturers have a sustainability policy in place, and 8.3% are developing one, according to a recent National Association of Manufacturing (NAM) survey.
- Nestle, Unilever, Mondelez, and PEPSICO have all set the ambitious goal of having 100% sustainable packaging by 2025, requiring their suppliers to independently follow their lead and attain ambitious sustainability goals.
- 66% of customers buying globally known products and brands across 60 different nations are willing to pay more for products produced using sustainable manufacturing, according to Nielsen’s Global Corporate Sustainability Report.
- 49% of all purchasing decisions by consumers evaluating B2C brands is influenced by how effective manufacturers’ sustainability efforts are, according to AT Kearney.
- Sales increased an average of between 4% with 10% in response to manufacturers achieving greater sustainability in their operations alone, according to Accenture.
Sustainability Is The Cornerstone Of Manufacturing Competitiveness
Customers reward manufacturers who have the greatest supply chain transparency and most effective sustainability strategies with more sales. That’s why sustainable manufacturing needs to be integral to every aspect of a manufacturer’s operations today if it’s going to succeed. Sustainability needs to be designed into every manufacturing aspect to succeed with suppliers through production, fulfillment, and end-of-life recovery and disposal.
Here are a few of the many ways manufacturers are achieving more because they’re prioritizing sustainability and all the transparency across supply chains that come with it:
- By achieving greater sustainability and complying with ISO14001 wins Somachini more business. Somachini produces heavy truck timing gears for Detroit Diesel and Daimler to Germany, specializing in high precision, high volume production. To do business in the automotive industry, Somachini has to comply with the ISO 14001 standard. A core part of their efforts is recycling materials used during the production process, including aluminum and steel sent to a nearby recycling facility. Somachini’s commitment to sustainability is exceptional as they have every consumable item recycled from their plant. They’ve also designed water systems that only release standard sink and toilet sewage to their city’s water systems. Their commitment to excelling at sustainability has won them additional contracts over other suppliers in the highly competitive commercial automotive OEM market for truck timing gears. An added benefit of being so sustainable is Somachini has never missed a customer shipment. By standardizing on DELMIAworks’ ERP system, Somaschini has been able to excel on three core dimensions of their business: automotive quality and the IATF 16949 standard, compliance with ISO 14001 for sustainability EDI, which is essential for transacting with their customers.
- Reduce energy-related costs and drive down operating expenses by using more recyclable materials. 2020 brought a strong, immediate focus on business continuity and cost-cutting, and the goal of reducing energy-related costs and carbon footprints became more urgent for many manufacturers to achieve. Lean manufacturing techniques are made stronger when combined with sustainability foundations, as plastics manufacturers worldwide see today. Many DELMIAworks customers have adopted more energy-efficient lighting while installing solar panels on their production plants’ roofs to become more energy-independent while reducing their carbon footprint.
- Forward-thinking manufacturers turn their sustainability initiatives into a lean, competitive advantage, reduce costs, and improving their industry reputations for being environmentally friendly at the same time. A leading West Coast-based extrusion manufacturer, Fabricated Extrusion, is turning sustainability initiatives into a lean, competitive advantage by doing the following. First, they are implementing a water reclamation plan ahead of schedule and delivering cost reductions already. Second, they initiated a Trim Buyback Program to help their customers recycle plastics they no longer need. Third, they’ve initiated an energy conservation program based on their standardizing on solar energy. A video summarizing Fabrication Extrusion’s many sustainability accomplishments is shown below:
- Design-for-sustainability continues to open up new markets for manufacturers while making constant contributions to improving the environment. Manufacturers are reducing operating expenses by designing sustainability into their products from the initial product concepts through production. When one of the primary product development goals is to create more biodegradable, lighter-weight products with recyclable packaging materials, manufacturers have more opportunities to reduce sourcing and procurement costs. Recycling packaging can reduce costs by 60% or more, according to Hewlett-Packard’s extensive work on their Design for Environment (DfE) program.
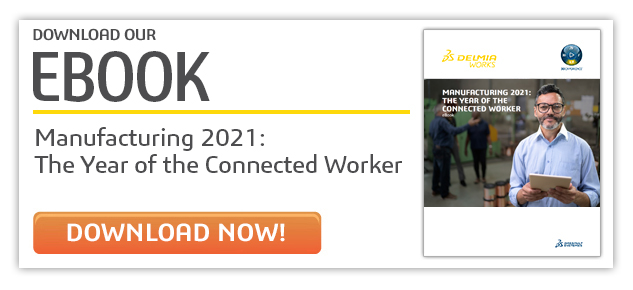