Why The Future Of Smart Manufacturing Starts With Connected Workers
Bottom Line: Providing connected workers and teams with the tools they need to excel onsite and remotely while enabling shop floor operations to transition from one manufacturing process to another is the essence of smart manufacturing today.
Connected workers are the cornerstone of smart manufacturing’s future. The business continuity lessons learned in 2020 have become the catalyst that drives more significant innovation across shop floors. Five key technology areas, including supply chain traceability, real-time production & process monitoring, remote access technologies, production cell redesigns, and health screening must be attuned to connected workers first to succeed.
Manufacturers are going to emphasize three key strategies to achieve greater production efficiencies and quality in 2021, according to a recent series of calls with CFOs during December and January:
- Manufacturers are doubling down on remote technologies that enable more of their workforce to work from home and be more productive due to improved real-time monitoring, automation, and reporting.
- Increased spending on training and development keeps current employees’ skill sets current while educating the next generation of the company’s supply chain, production, quality, and manufacturing execution leaders.
- Be a leader in taking the constraint of social distancing guidelines and turning it into a more significant opportunity for every factory employee to achieve more autonomy and ownership of their job.
Smart manufacturing is going to be redefined in 2021 to include the people element more than ever before. Rapidly improving remote working technologies and increased training to sharpen skills across the shop floor create the ideal opportunity for smart manufacturing to achieve its true potential. And that potential begins with the most accurate data possible.
End-to-end visibility has always been a goal manufacturers strive for. In 2021, the combination of remote technologies increased training and development. Turning social distancing constraints into greater job autonomy opportunities takes end-to-end visibility to a new level of accuracy, control, and customer responsiveness.
2021: The Year Manufacturers Set Their People Up To Excel
Smart manufacturing is entering a new phase in 2021 – one where manufacturers compete against each other based on how productive they can enable their people to be. Remote working technologies, improvements in real-time monitoring, and production systems sharing a common database are the foundation. Realizing how productive people can be with these technologies is key – not the technologies themselves, and that’s a big difference from previous years.
Realizing that any technology spending only matters when it removes roadblocks or accelerates a person’s productivity in 2021 and beyond, here are the top six improvements coming to smart manufacturing in 2021:
- Technology tools that enable the connected worker – and productivity of all workers are the highest priority overall. Remote access proved invaluable in 2020, primarily for keeping supply chains, production scheduling, shipping, and customer service moving. Manufacturers who had remote access picked up new customers in 2020 because they could run at capacity while keeping their workers safe at home.
- More intuitive, touchscreen-based shop floor interfaces to ERP systems improve production efficiency with configurable Work Center dashboards. Key benefits of this new class of interface include streamlining data access and real-time information collection and availability, improving quality, and reducing costs. New intuitive user interfaces also help digitize manufacturing operations and improve production efficiency. DELMIAworks SHOPWORKS, a touchscreen-based shop floor interface to DELMIAworks 2020X, improves production efficiency with configurable Work Center dashboards. Key benefits include streamlining data access and RealTime™ information collection and availability, improving quality, and reducing costs. SHOPWORKS also helps digitize manufacturing operations and improve production efficiency. For more information on DELMIAworks 202X, please see the recent post, DELMIAworks 2020X Shows Our Commitment To Keep Innovating For Our Customers.
- The ability to shift quickly from one manufacturing process to another and manufacture new products in days will be a much sought-after strength across manufacturing in 2021. Other manufacturers turned the most popular products they’re producing during short-notice production to new standard products. ERP systems that support pre-built manufacturing processes will become necessary as manufacturers look to gain more short-notice production runs across a broader customer base while launching new products of their own. Connected workers are the cornerstone of enabling manufacturers to shift from one production process to another in days instead of weeks.
- Business continuity lessons learned during 2020 translate into manufacturers’ urgency to gain greater financial visibility across manufacturing operations. Knowing how stable sales, revenue, and production forecasts are for the coming year will drive manufacturers to adopt more finely tuned financial reporting systems. They’re going to set the ambitious goal of excelling at revenue and cost management with challenging new targets for their teams to achieve. Knowing with greater certainty of how manufacturing operations’ variations impact financial statements is the cornerstone they’ll need to measure progress and results.
- Predictive analytics and process control will lead to the adoption of all new technologies in manufacturing in 2021 as manufacturers look to reduce risk and costs with higher quality data. Making the transition to smart manufacturing begins with reliable data that provides manufacturers with new, often unexpected insights into increasing production efficiency and quality. Assessing risks to production and revenue forecasts using predictive analytics will gain momentum because manufacturers will be striving for the most accurate sales and margin forecasts they can get, further improving financial visibility.
- Real-time production and process monitoring will start taking on a new role in risk management by providing real-time consumption, quality, and production efficiency. Manufacturers will increase their use of real-time process and production monitoring to assess and reduce risk. They’ll rely on the insights gained from these systems as an early-warning system of factors that could impact revenue and margins. Knowing that every machine, process, and system is operating and stable brings greater stability to production and revenue forecasts and, ultimately, financial results.
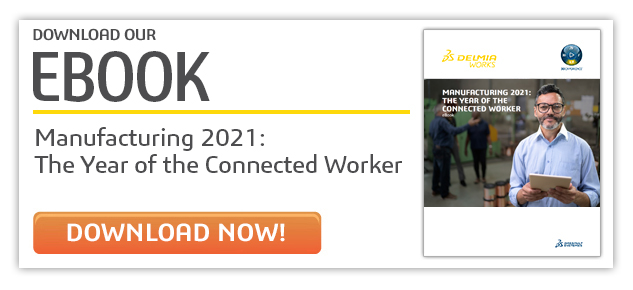