Real-Time Monitoring Fuels IoT Growth In Manufacturing
- 72% of manufacturers say real-time monitoring is essential for streamlining and making inventory reconciliation more efficient.
- 69% are relying on real-time monitoring to increase the accuracy of tracking production time, downtime, total parts created, rejects and parts remaining to be produced.
- 63% are relying on real-time monitoring and consider it essential for tracking machine utilization, scrap and downtime reporting.
- 53% rely on real-time monitoring to increase Overall Equipment Effectiveness (OEE) accuracy.
Manufacturers in the high-performance cohort captured in our latest survey are using real-time monitoring to aggregate metrics and gain a 360-degree view of manufacturing operations accessible from any mobile or handheld device. 56% of high-performance manufacturers are combining real-time monitoring and mobile technologies to provide production teams with accurate, precise views of production performance as it happens.
Manufacturers are prioritizing real-time monitoring to attain the goals of increasing product quality, reducing time-to-market and attaining faster revenue growth. This month IQMS interviewed 151 manufacturers in North America to understand the current and plans for analytics and manufacturing intelligence, mobility, quality and real-time monitoring. Streamlining inventory reconciliation leads all benefits of real-time monitoring with 72% of manufacturers saying having this capability is essential for their success. Improving product quality and increasing Overall Equipment Effectiveness (OEE) by being able to better track machine utilization, scrap and downtime reporting is also a high priority.
Real-Time Monitoring’s Many Benefits Are Fueling IoT Growth
Improving product quality, reducing order turn-around times, keeping sales, manufacturing, and engineering tightly coordinated, having greater flexibility to take on short production runs and succeeding with new product launches are the five characteristics of the highest performing manufacturers based on the latest IQMS survey.
What’s especially interesting about the results is how all manufacturers begin their real-time monitoring journey by concentrating on streamlining and making inventory reconciliation more efficient first, then concentrate on improving shop floor performance. The high-performance cohort is quick to aggregate metrics and gains a 360-degree view of all shop floors, often having real-time availability of Overall Equipment Effectiveness (OEE) across multiple production lines. The graphic below from our survey shows the importance of real-time monitoring approaches over the next 12 months.
Real-Time Monitoring Is At An Inflection Point
Manufacturing is now a digitally driven business where data, insights, and intelligence have become the most valuable asset a company has. Real-time data quickly transformed into actionable intelligence is eliminating cost and job overruns, improving production line productivity, reducing product defects and increasing quality, extending equipment life, and understanding customer requirements better than before.
Manufacturers comprise the most data prolific industry on the planet, generating on average 1.912 petabytes of data a year according to IDC and McKinsey Global Institute. Each faces the competitive challenge of making the most of the data have. And despite being members of the most data-prolific industry on the planet, there often isn’t the right real-time data they need to make quick course corrections on the shop floor.
That’s why the need for real-time data from across their shop floors is driving a revolution in real-time monitoring, leading to an inflection point that is happening today. Progressing from Light Sticks integrated to ERP systems as IQMS has with its RealTime™ Production Monitoring integrated to EnterpriseIQ to Programmable Logic Controllers (PLC) and Internet of Things (IoT) sensors, manufacturers need greater intelligence and knowledge in the following areas:
- Machine, production line and plant optimization based on real-time data captured using IoT sensors across supply chains, inbound inspection, shop floor machinery and assets, logistics and fulfillment systems.
- Improved offline and online condition analysis using richer data sets generated from IoT sensors and advanced analytics, big data and machine learning applications that can produce time-based analysis of machine cycles, cycle time performance and assist in optimizing production scheduling and manufacturing operations.
- Pattern recognition based on machine-level data that can predict product quality problems, machine stability, and reliability, and verify OEE levels.
- Predictive maintenance metrics to the machine level including condition monitoring, frequency analysis, kurtosis and greater accuracy to drive maintenance, repair, and overhaul (MRO).
Our latest survey results show manufacturers are very goal- and outcome-driven in their adoption of IoT as a real-time monitoring technology. They’re balancing traditional Light Sticks and PLCs with IoT based on the cost, data latency, reliability and scale possible.
Being digitally-driven businesses, manufacturers are adopting IoT faster than many other industries as the recent Capgemini study, Unlocking The Business Value of IoT in Operations, illustrates below. Capgemini interviewed senior executives from over 300 global organizations who are already implementing IoT initiatives. The research team also analyzed 300 cross-sector, real-life IoT uses cases used for internal operations spanning industrial manufacturing, retail, consumer products, energy & utilities, automotive and telecommunications, to identify which ones have the greatest impact.
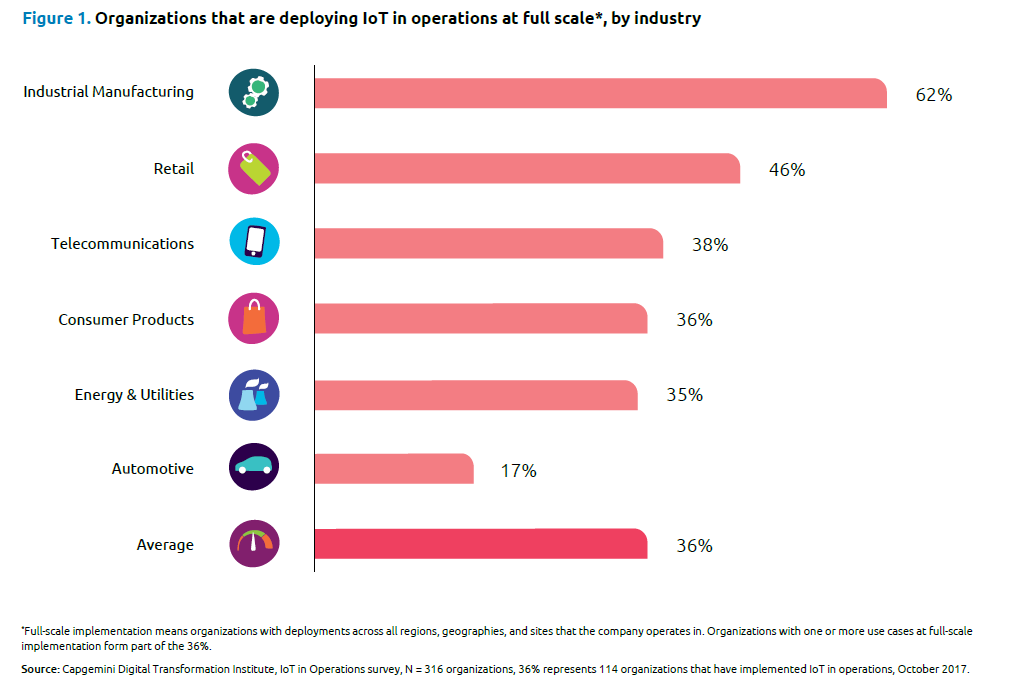
Environmental monitoring, smart metering, renewable plants supervision and inventory intelligence are among the top areas IoT can deliver the most value for in 2018. Additional areas where IoT has the greatest potential to deliver value include improving operator productivity in production plants, improving the accuracy of warehouse management and inventory monitoring, reducing non-technical operations losses and enabling smart product tracking. The following grid compares the benefits from IoT implementation by payback period of investment. Capgemini predicts IoT will contribute to Manufacturing Intelligence and Product Quality Optimization gaining adoption over the long-term.
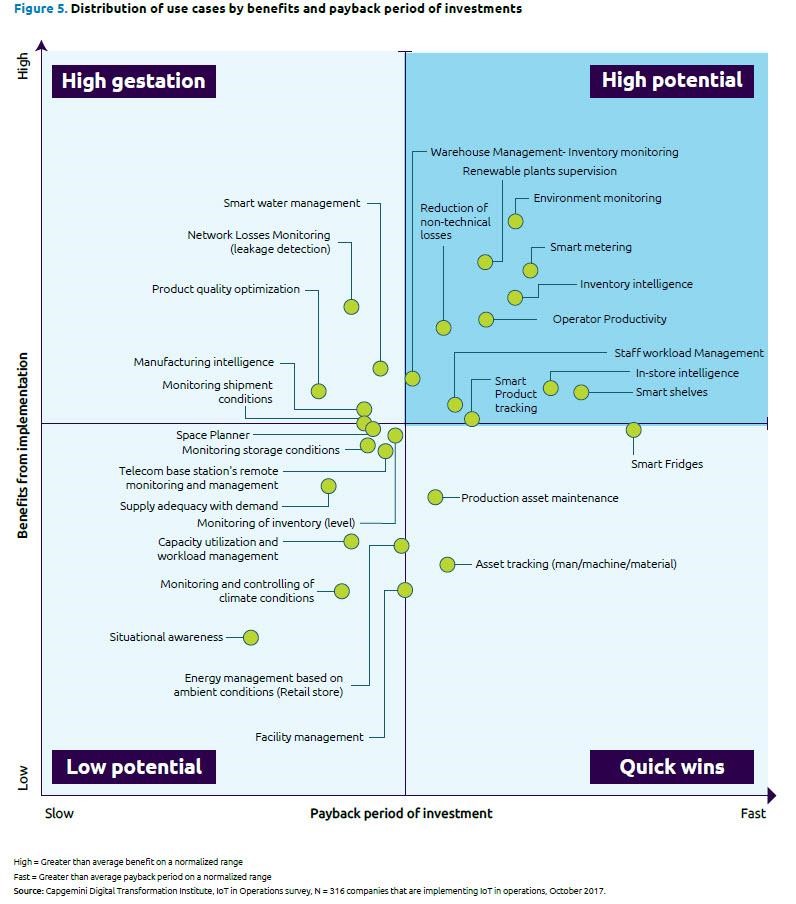