10 Ways Manufacturing Intelligence Is Revolutionizing ERP In 2018
ERP’s inflection point has arrived, and it’s delivering Manufacturing Intelligence and insights that are revolutionizing operations management from the shop floor to the top floor. Measuring, monitoring and improving every aspect of shop floor operations opens up new opportunities for improving profits and fueling new growth.
- Accelerating and improving process automation using Manufacturing Intelligence (MI) in manufacturing is attracting $1B in investments this year alone according to IDC.
- Manufacturing Intelligence adoption continues to accelerate across all manufacturing sectors with Price Waterhouse Coopers predicting that 83% of all manufacturers will be relying on MI-based solutions within five years.
- 46% of manufacturers agree that implementing and using data analytics is necessary to stay competitive and grow their businesses.
- 69% of decision-makers believe analytics will be crucial for business success in 2020, with 15% considering it essential to operating their businesses today.
- According to a recent McKinsey Global Institute study, a leading aerospace manufacturer is using MI to track and improve Overall Equipment Effectiveness (OEE), reaping a $415M savings with 60% attributed to advanced analytics and Manufacturing Intelligence.
Combining ERP Data And Manufacturing Intelligence Drives Revenue Growth
Always on the lookout for new growth opportunities, manufacturers are looking to MI as the catalyst they need to find and capitalize on new areas of operations improvements and growth. With the manufacturing industry showing solid signs of growth in 2018, it’s time for all manufacturers to redefine and revolutionize how they use their ERP systems as a platform for solid revenue growth. MI is the fuel that transforms ERP systems into revenue growth catalysts that flex to the unique needs of each manufacturer. Monitoring an essential series of manufacturing analytics, metrics and KPIs from the shop floor to the top floor also assists in finding machines, production assets and processes that may need maintenance. Predictive analytics is a core component of MI and is revolutionizing reliability today. The ten ways Manufacturing Intelligence is going to revolutionize ERP in 2018 are defined below:
- Manufacturing Intelligence is enabling ERP systems to deliver real-time Overall Equipment Effectiveness (OEE) for the first time – Many manufacturers consider this is the most important metric there is for making sure their daily production operations are stable and profitable. OEE measures the performance of a given machine, product line, work team or entire production center. This metrics is most often used at the machine level to track each production asset’s utilization rate, performance levels, and quality. It’s calculated using the formula of Availability x Performance x Quality. It’s also pervasively used for predictive maintenance of machinery, which the following graphic is based on:
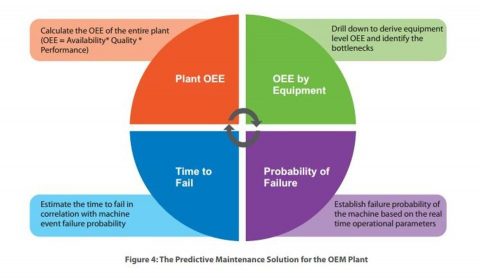
- It’s possible to increase production capacity up to 20% while lowering material consumption rates by 4% by combining ERP apps and Manufacturing Intelligence. Current and future manufacturing systems are being designed to capitalize on predictive data analytics, and Manufacturing Intelligence has the potential to improve yield rates at the machine, production cell, and plant levels. The following graphic from General Electric and cited in a National Institute of Standards (NIST) provides a summary of benefits that are being gained using predictive analytics and Manufacturing Intelligence in a typical production operation today.
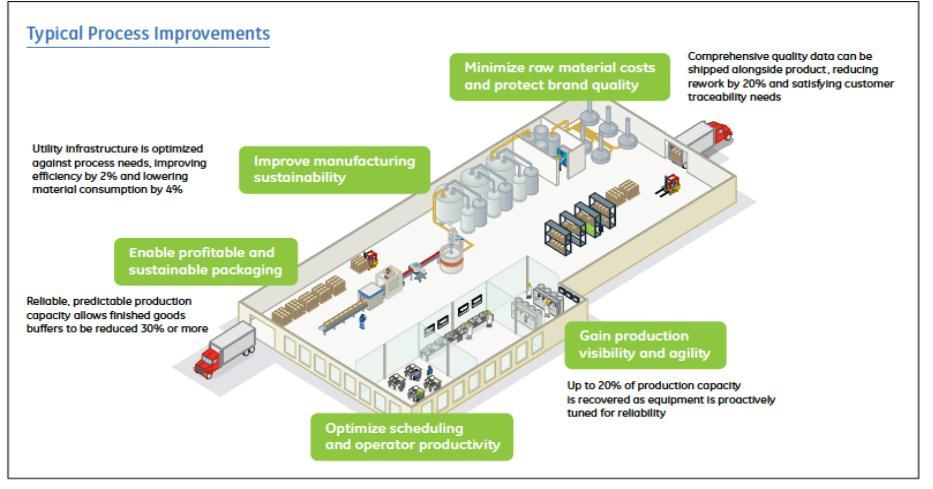
- Manufacturing Intelligence is proliferating quality management and compliance across all shop floors and locations, enabling manufacturers to make quality a core strength quickly. The most enduring, resilient and strong differentiator any manufacturer has is a reputation for product quality. Using Manufacturing Intelligence-based insights from the shop floor and translated into financial metrics for top floor executives, CEOs and other manufacturing leaders can now see financial value of improving product quality. In 2018, more manufacturers will combine ERP, 1quality management systems, and Manufacturing Intelligence to get a 360-degree view of quality across all production centers.
- Optimizing pricing by predicting cost increases and decreases using Manufacturing Intelligence increases gross margins and fuels revenue growth. By monitoring, managing, and optimizing pricing across all product lines, manufacturers can plan out production runs to gain the greatest margins. Pricing is a potential differentiator, and in 2018 this area is where ERP systems are seeing the greatest revolution delivering greater growth.
- Improving production yields by having real-time Manufacturing Intelligence guide the optimizing of the team, machine, supplier and customer order planning and fulfillment. Manufacturing Intelligence is making a difference on the shop floor daily in aerospace & defense, discrete, industrial and high-tech manufacturers today. Manufacturers are turning to more complex, customized products to use more of their production capacity, and Manufacturing Intelligence can help to optimize the best possible selection of machines, trained staffs, and suppliers.
- Combining ERP systems and Manufacturing Intelligence to capture data used in advanced prediction algorithms that predict which factors most and least impact quality company-wide is happening today. Manufacturers often are challenged with making product and service quality to the workflow level a core part of their companies. Often quality is isolated. Manufacturing Intelligence is revolutionizing product and service quality by determining which internal processes, workflows, and factors contribute most and least to quality objectives being met. Using Manufacturing Intelligence manufacturers will be able to attain much greater levels of prediction regarding how their quality and sourcing decisions contribute to greater Six Sigma performance within the Define, Measure, Analyze, Improve, and Control (DMAIC) framework.
- Accelerating Manufacturing Cycle Times based on greater insights from MI. By definition, Manufacturing Cycle Time quantifies the amount of elapsed time from when an order is taken until the product is produced and entered into finished goods inventory. Cycle times vary by segment of the manufacturing industry, size of manufacturing operation, global location and relative stability fo supply chains supporting operations. The greater the level of insight into how cycle times can be improved, the more competitive any manufacturer is. This area is one of the primary catalyst revolutionizing ERP systems’ values delivered in 2018.
- Tracking Perfect Order Performance for the first time across multiple production centers globally using ERP systems as the system of record. Perfect order performance measures how effective a manufacturer is at delivering complete, accurate, damage-free orders to customers on time. The equation that defines the perfect order Index (POI) or perfect order performance is the (Percent of orders delivered on time) * (Percent of orders complete) * (Percent of orders damage free) * (Percent of orders with accurate documentation) * 100. The majority of manufacturers are attaining a perfect order performance level of 90% or higher according to the The American Productivity and Quality Center (APQC). The more complex the product lines, configuration options including build-to-order, configure-to-order and engineer-to-order workflows, the more challenging it is to attain a high, perfect order level. Greater analytics and insights gained from real-time integration and monitoring help complex manufacturers attained higher perfect order levels over time.
- Improving preventative maintenance and Maintenance, Repair and Overhaul (MRO) performance with greater predictive accuracy to the component and part-level is another area Manufacturing Intelligence is driving an ERP inflection point. One of the foundational elements of Manufacturing Intelligence is the development and delivery of predictive analytics and an advanced algorithm that can predict when a production machine will need maintenance. The data hidden in MRO-based processes are now being discovered with Manufacturing Intelligence, fueling entirely new process workflows to improve manufacturing performance.
- Understanding why the Return Material Authorization (RMA) Rate and % Of Manufacturing Returns fluctuates and what can be done to improve quality.Return Material Authorizations (RMA) are by definition the percentage of products shipped to customers that are returned due to defective parts or not otherwise meeting their requirements. RMAs are a good leading indicator of potential quality problems. Manufacturing Intelligence is helping to create new KPIs and metrics that define and quantify the factors that most lead to RMAs happening in the first place. Best of all, ERP systems combined with Manufacturing Intelligence predict which supplier and their quality level, production process and quality metrics need to improve to reduce RMAs.
Bottom Line: Manufacturing Intelligence is driving an inflection point across global ERP systems today by improving data insights, customer knowledge, and infusing greater intensity to improve every phase of the manufacturing process.