How Blockchain Can Improve Manufacturing In 2019
- The business value-add of blockchain will grow to slightly more than $176B by 2025, then exceed $3.1T by 2030 according to Gartner.
- Typical product recalls cost $8M, and many could be averted with improved track-and-traceability enabled by blockchain.
- Combining blockchain and IoT will revolutionize product safety, track-and-traceability, warranty management, Maintenance, Repair & Overhaul (MRO), and lead to new usage-based business models for smart, connected products.
- By 2023, 30% of manufacturing companies with more than $5B in revenue will have implemented Industry 4.0 pilot projects using blockchain, up from less than 5% today according to Gartner.
Blockchain’s greatest potential to deliver business value is in manufacturing. Increasing visibility across every area of manufacturing starting with suppliers, strategic sourcing, procurement, and supplier quality to shop floor operations including machine-level monitoring and service, blockchain can enable entirely new manufacturing business models. Supply chains are the foundation of every manufacturing business, capable of making use of blockchain’s distributed ledger structure and block-based approach to aggregating value-exchange transactions to improve supply chain efficiency first. By improving supplier order accuracy, product quality, and track-and-traceability, manufacturers will be able to meet delivery dates, improve product quality and sell more.
Capgemini Research Institute’s recent study, Does blockchain hold the key to a new age of supply chain transparency and trust? provide valuable insights into how blockchain can improve supply chains and manufacturing. A copy of the study is available here (PDF, 32 pp., no opt-in). Capgemini surveyed 731 organizations globally regarding their existing and planned blockchain initiatives. Initial interviews yielded 447 organizations who are currently experimenting with or implementing blockchain. Please see pages 25 & 26 of the study for additional details regarding the methodology.
Key takeaways of the study include the following:
- Typical product recalls cost $8M, and many could be averted with improved track-and-traceability enabled by blockchain. Capgemini found that there was 456 food recalls alone in the U.S. last year, costing nearly $3.5B. Blockchain’s general ledger structure provides a real-time audit trail for all transactions secured against modifications making it ideal for audit and compliance-intensive industries.
- Gaining greater cost savings (89%), enhancing traceability (81%) and enhancing transparency (79%) are the top three drivers behind manufacturer’s blockchain investments today. Additional drivers include increasing revenues (57%), reducing risks (50%), creating new business opportunities (44%) and being more customer-centric (38%). The following graphic from the study illustrates the manufacturer’s priorities for blockchain. Capgemini finds that improving track-and-traceability is a primary driver across all manufacturers, consistent with the broader trend of manufacturers adopting software applications that improve this function today. That’s also understandable given how additional regulatory compliance requirements are coming in 2019 and those manufacturers competing in highly regulated industries including aerospace & defense, medical devices, and pharma are exploring how blockchain can give them a competitive edge now
- Digital marketplaces, tracking critical supply chain parameters, tracking components quality, preventing counterfeit products, and tracking asset maintenance are the five areas Capgemini predicts blockchain will see the greatest adoption. Based on interviews with industry experts and startups, Capgemini found 24 blockchain use cases which are compared by level of adoption and complexity in the graphic below. The use cases reflect how managing supplier contracts is already emerging as one of the most popular blockchain use cases for manufacturing organizations today and will accelerate as compliance becomes even more important in 2019.
- Manufacturers have the most at-scale deployments of blockchain today, leading all industries included in the study. Blockchain adoption is still nascent across all industries included in the study, with 6% of manufacturers having at-scale implementations today. Customer products manufacturers lead in pilots, with 15% actively [purusing blockchain in limited scope today. And retailers trail all industries with 91% having only proofs of concept.
- Combining IoT and blockchain at the shipping container level in supply chains increases authenticity, transparency, compliance to product and contractual requirements while reducing counterfeiting. In highly regulated industries including Aerospace & Defense (A&D), Consumer Packaged Goods (CPG), medical devices, and pharma, combining IoT and blockchain provides real-time data on the shipping container conditions, tamper-proof storage, each shipment’s locational history and if there have been changes in temperature and product condition. Capgemini sees use cases where a change in a shipment’s temperature as measured by a sensor change sends alerts regarding contractual compliance of perishable meats and produce, averting the potential of bad product quality and rejected shipments once they reach their destination.
- Capgemini found that 13% of manufacturers are Pacesetters and are either implementing blockchain at scale or have pilots in at least one site. Over 60% of Pacesetters believe that blockchain is already transforming the way they collaborate with their partners. Encouraged by these results, Pacesetters are set to increase their blockchain investment by 30% in the next three years. They lead early-stage experimenters and all implementers on three core dimensions of organizational readiness. These include end-to-end visibility across functions, detailed and defined supportive processes, and availability of the right talent to succeed.
- Lack of a clear ROI, immature technology and regulatory challenges are the top three hurdles Pacesetter-class manufacturers face in getting blockchain initiatives accepted and into production. All implementations face these three challenges in addition to having to overcome the lack of complementary IT systems at the partner organizations. The following graphic compares the hurdles all manufacturers face in getting blockchain projects implemented by the level of manufacturers adoption success (Pacesetter, early-stage experimenters, all implementers).
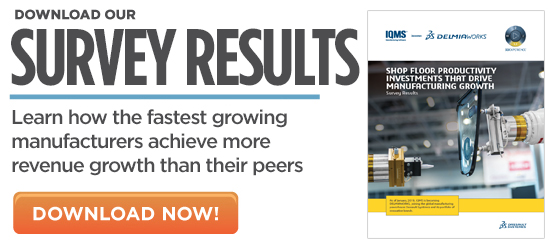