2021 Manufacturing Trends: Connecting Workers Will Be Key
2021 manufacturing trends will be driven by the lessons learned in 2020. Whether assisting workers on the shop floor or helping back-office employees to continue their jobs remotely, smart manufacturing technologies have been central to enabling business continuity in the wake of the coronavirus pandemic. This focus will only increase as companies compete for business based on the productivity of their people. That’s why we’re calling 2021 the year of the connected worker.
2021 Manufacturing Trends to Improve Decision Making and Productivity
Let’s look at nine areas of technology investment where manufacturers empower employees to improve decision-making and productivity in 2021.
- Bridging the Skills Gap
The competition for jobs in the service sector over those in manufacturing puts greater pressure than ever on manufacturers to pay more and offer attractive work environments—most notably by automating previously manual tasks—to attract and retain employees.
This is a primary driver behind enabling the connected worker. The idea is to create digital work center consoles that guide, record, and inform workers so they can quickly step into a work center, know what to do and how to do it, and take whatever manual actions might be necessary to complete a particular production run. This approach enables faster changeovers, requires less training, prevents the most common types of human errors, and significantly increases labor flexibility.
- ERP for Business Continuity
Enterprise resource planning is no longer optional; it has emerged as the foundation for ensuring business continuity. Top-performing manufacturers use real-time insights from their ERP systems to manage shifts in market demand and keep production on track. They empower employees to do their jobs, whether working onsite or remotely. They will continue to thrive despite the market uncertainty that could remain for another year.
Additionally, manufacturers turn to the more finely tuned financial reporting provided by ERP systems to better understand how stable their sales, revenue, and production forecasts are. Knowing how variations in manufacturing operations impact financial statements will be a cornerstone in measuring the company’s progress in meeting financial goals. The bottom line has end-to-end visibility across manufacturing is what’s needed most to attain business continuity. The following graphic illustrates how manufacturers are achieving end-to-end manufacturing visibility today:
- Automated Quoting and Pricing
Demands for faster time-to-market, greater channel visibility, and more visually compelling quotes of custom-configured products using 3D images increase the use of configure, price, quote (CPQ) tools.
The most effective CPQ tools are available as part of a modern ERP system due to the accuracy and timeliness of working from the same data. This translates into improved price management and control across channels, increased margins, and reduced order errors in the process—helping speed time-to-market and preserve margins. Additionally, by adopting CPQ and ERP capabilities as part of a design-to-manufacturing strategy, manufacturers can speed new product development cycles, improve product quality, and increase yield rates. The following graphic explains why having a CPQ system integral to an ERP platform helps accelerate time-to-market.
Getting more quotes done in less time leads to more sales starts with a CPQ system that’s designed into ERP.
- Real-Time Insights for the Shop Floor and Back Office
“Rapid” has taken on new meaning in the wake of COVID-19, as many manufacturers tightened their reporting from weeks to days and from days to hours. Whether responding to rapid changes in market demand or shifts in the supply chain, manufacturers have relied on real-time data to quickly make informed decisions.
Real-time process and production monitoring have been instrumental in giving manufacturers insights into capacity to take on additional business, identifying potential issues before they affect product quality or delivery times, and—when uses with manufacturing execution system (MES) and quality management software—running lights-out manufacturing shifts.
Now real-time visibility is headed into the back office as CFOs rely on ERP systems to monitor accounts payable and cash flow for a timely, accurate view of the revenues they’re generating. In 2021, manufacturers will increase their reliance on real-time insights across the organization for immediate insights into factors that could impact revenue and margins.
- Competing on Shorter, Predictable Production
Facing unprecedented uncertainty in 2020, customers turn to companies that can deliver quality products quickly and predictably on time. Manufacturers who can meet this demand are growing their business by 115% or more.
Instead of taking six months to get a new production line up and running, manufacturers are doing it one month. In 2021, ERP systems that support pre-built manufacturing processes will become necessary to support more short-notice production runs across a broader customer base. Additionally, integrating their ERP and computer-aided design (CAD) will further tighten the time it takes to develop a new product and get it into production.
- The mainstreaming of IoT
We have seen an uptick in manufacturers investing in either upgrading their existing machinery with the Internet of Things (IoT) sensors or buying new smart, connected machines, which will expand in 2021. The driver might be monitoring the number of cycles on a machine and predicting maintenance needs rather than having maintenance staff look for machine issues. It can be a more complex digital transformation, like measuring critical dimensions with digital scanning devices and alerting for issues through statistical process control (SPC) type monitoring. Early adopters of these smart machines already see returns on their investments with more machinery uptime, higher yield rates from production runs, and new insights into improving manufacturing efficiencies.
- Compliance as a Competitive Asset
In the wake of the pandemic, customers in regulated industries value manufacturers experienced in gaining certifications, collaborating with regulatory auditors, and staying in good standing with compliance organizations. Compliance as a competitive advantage occurs across all manufacturing, with contract manufacturers seeing the greatest gains by offering their compliance expertise to brand manufacturers.
Providing proof that inbound supplier shipments to a manufacturing facility is clean and compliant with health and safety regulations will become an even greater competitive strength in 2021. Trace-and-trace functionality will play a central role in delivering this proof. Acumen Research & Consulting predicts that global demand for manufacturing traceability, including track-and-trace software, will reach $7.2 billion in 2026.
- Sustainability in Manufacturing
Manufacturers are increasingly embracing sustainability best practices. Key motivators include a desire to become a good steward of the environment, the financial benefits of sustainable practices, demands for regulatory compliance, or some combination of these drivers.
Sustainability initiatives may include process redesign to reduce waste, packaging, and product lifecycle improvements; for some, the creation of new biodegradable products, lighter-weight products, and recyclable packaging materials.
More manufacturers will also acquire energy-efficient smart machines that consume an order of magnitude less energy than older equipment. They also produce fewer scrap parts, improving profits, as well as require less direct labor.
- Digital Twins and Modeling
Digital twins are having a breakout year as more pilot digital twin-based projects to ensure employee safety, create more self-contained work centers, and improve machine uptime. Digital twins are also being used to reduce new product risk and provide greater financial visibility by validating that new product designs are buildable and profitable once produced and sold.
Meanwhile, modeling is the cornerstone of the design-to-manufacturing strategies proven so effective this year in accelerating time-to-market, improving yields, and most importantly, serving customers. Look for design data structures, files, and processes to become even more integrated with manufacturing, engineering, sales, and service in 2021.
Clearly, the smart manufacturing technologies that enabled business continuity in 2020 will continue to play a central role in enabling manufacturers to compete for business based on their people’s productivity. By expanding their technology investments to address the nine priorities discussed here, manufacturers can empower employees to improve decision-making and achieve greater productivity in 2021 and beyond.
For more details on manufacturing trends in 2021, download our new e-book here.
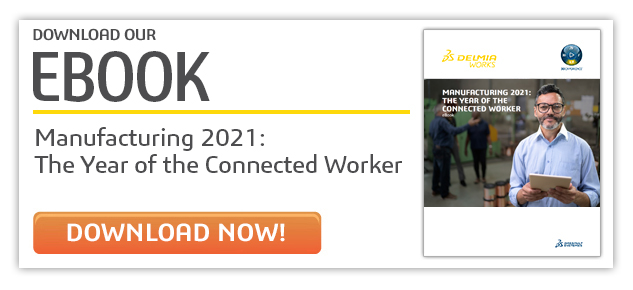