Top 10 2020 Manufacturing Trends
Bottom Line: 2020 manufacturing trends are driven by manufacturers’ strong confidence in their ability to deliver high-quality products that earn repeat orders while delivering excellent customer experiences. Their most anticipated growth barriers are chronic labor shortages, pre-emptive competitive price wars, and early signs of sales cycles slowing down.
Running Lean While Focusing On Keeping Margins Strong
Running lean and struggling to find the employees they need to keep up the pace of production across their shop floors, small and mid-tier manufacturers are prioritizing Inventory Control and Scheduling to make themselves as efficient as possible. The top ten manufacturing trends for 2020 are based on in-person plant visits during the 4th quarter of 2019 along with primary research completed in December 2019 and January 2020. Research firm Decision Analyst in collaboration with Dassault Systemes DELMIAWORKS (IQMS) recently interviewed 150 small and mid-tier North American manufacturers to find out what their top priorities and concerns are for 2020. What we learned together creates the foundation of our top ten manufacturing trends for 2020.
The majority of manufacturers enter 2020 running lean with fewer production technicians available than needed to handle the growing number and complexity of orders in their backlogs. No one wants to sacrifice gross margins, so every one of the manufacturers interviewed is placing a higher level of intensity and effort into improving inventory turns, cycle times, and shop floor efficiency. Going into the New Year, they’re most confident in their ability to deliver high-quality products that will lead to customers repurchasing from them. The following graphic shows manufacturers’ confidence levels in processes going into the New Year, forming the cornerstone of our manufacturing predictions for 2020:
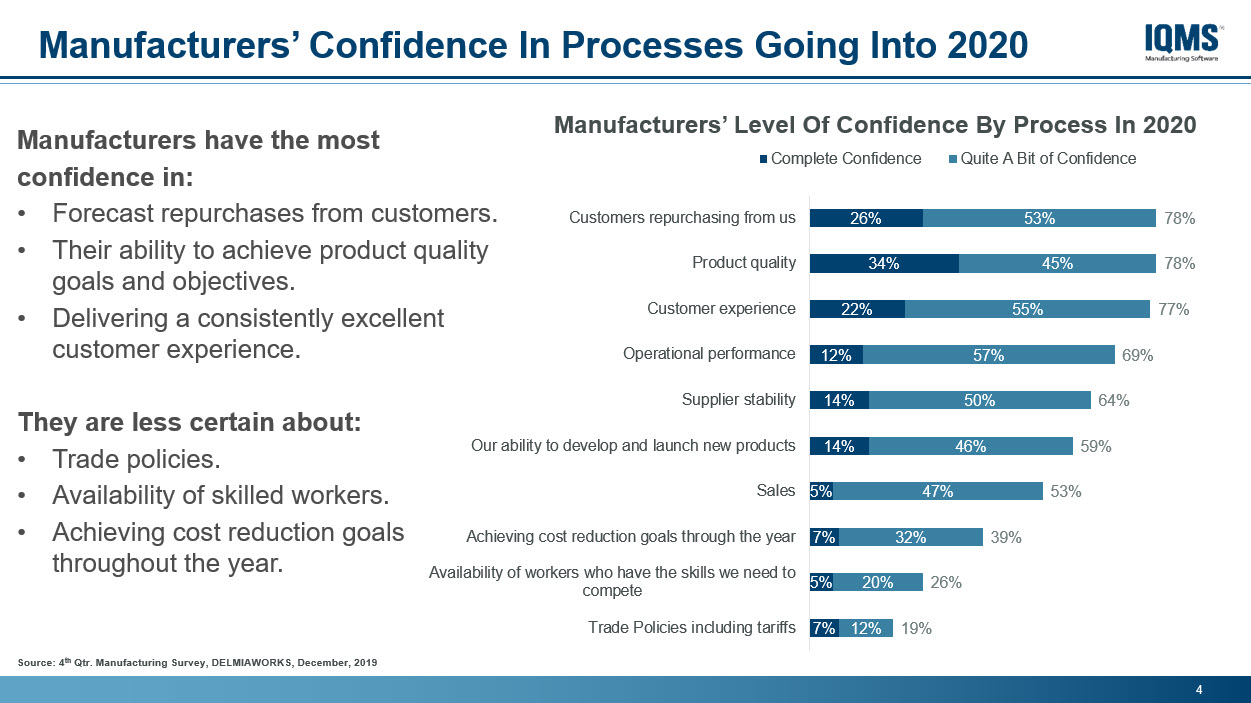
Top 10 Manufacturing Trends For 2020
- Manufacturers are going to focus on improving end-to-end visibility across their plants so they can increase volume production and achieve tighter per unit cost control. Initial efforts are going to focus on fine-tuning track-and-trace workflows to achieve greater order accuracy, improve compliance and reduce risk and improve supplier performance and quality. Manufacturers are going to adopt end-to-end visibility to also increase manufacturing efficiency, lessen the impact of product recalls, optimize manufacturing schedules and reduce manufacturing costs.
- Frustrated with the delays of relying on multiple systems for accounting and production reports, manufacturers will adopt a single, integrated system that tells them the immediate impact of production decisions on their profitability. In 2020, more manufacturers will transition from separate accounting, supply chain, ERP and MES systems to a common platform. Factors driving this change include the following: manufacturers are looking to become more efficient at short-notice productions runs; the pressure to excel as a supplier who can exceed quality benchmarks has never been greater, and the need to track shop floor decisions’ impacts on financial performance are now must-have insights they need to compete.
- Real-time monitoring goes mainstream across process and batch manufacturing, unlocking valuable data needed for better cost control down to the unit level. 81% of manufacturers say real-time monitoring is improving their business in a recent survey. Real-time monitoring goes mainstream across process and batch manufacturing due to the following: streamlining & making inventory reconciliation more efficient is a high priority; better track machine utilization, scrap and downtime reporting; and improving production plan performance
- Robots get installed and used for diverse, repetitive tasks on the shop floor ranging from end-of-arm assembly, labeling, pick and place, packaging, stacking, and palletizing to mitigate recurring labor shortages. 29% of mid-tier North American manufacturers said investing in robotics is their first priority in 2019. Plastics extrusion manufacturers are investing in robotics because they can’t find enough workers for shifts. Geographically remote manufacturers are relying on robotics to scale up fast and take larger customer production jobs they would otherwise pass on due to lack of labor.
- Software user interfaces for shop floor systems get makeovers and simplifications, to drive greater adoption and utilization. Shop floor systems are going to become easier to work within 2020, and the following are just a few of the many developments in this area: configurable alerts, dashboards, & widgets across all devices; sortable and searchable production summary data from any device on the shop floor in real-time; multi-work center dashboards will provide end-to-end production floor visibility; and audit and quality data reporting becomes more automated due to workflow improvements
- Manufacturers learn how to turn sustainability initiatives into a lean, competitive advantage, reducing costs, and improving their industry reputations for being environmentally friendly. A leading West Coast-based manufacturer is turning sustainability initiatives into a lean, competitive advantage by doing the following: investing in water reclamation systems and strategies; equipping production centers with Trim Buyback Programs; having a strategic commitment to energy conservation; and discovering new ways to improve and scale solar energy use across all production centers.
- Private equity investors continue to acquire manufacturers with the goals of consolidating them together to enable greater growth, while also providing manufacturing ownership with the opportunity to monetize their businesses. Leading private equity investors are saying that strategic buyers are looking to expand service offerings and become the single provider of all products and solutions in a given market category.
- Design-for-sustainability is going to motivate manufacturers to create new biodegradable products, lighter-weight products, and recyclable packaging materials. Also, manufacturers will acquire more energy-efficient production equipment such as electric vs hydraulic modeling machines. Sustainability is manufacturing’s greatest inflection point of 2020. Manufacturers are already making long-term investments to retool production lines, and its evident this is going to continue through 2020. Manufacturers are also adding new suppliers who can support biodegradable, lighter-weight products.
- Manufacturers will be more data-driven in 2020, adopting predictive analytics to troubleshoot problems, perform root cause analysis, improve product quality, and control per-unit costs. Searching for new ways to gain production efficiency across their shop floors and minimize the impact of higher material costs, labor shortages and tightening regulatory costs and reporting, manufacturers will turn to predictive analytics more in 2020 than in the past. Knowing how their decisions with suppliers, shop floor and labor scheduling and pricing impact production efficiency is also a driving factor making predictive analytics a higher priority than before.
- Customers will be asking for more quality audits next year, which is going to motivate more manufacturers to automate quality management and compliance reporting, so their quality engineers don’t need to compile reports by hand. Manufacturers will automate quality management in 2020 to more accurately define and track major and minor non-conformances by product, prioritizing them and what action is needed to resolve each faster. They’ll also automate quality management to streamline customer, internal and regulatory audits. Audit data will fuel the development of customer dashboards for the first time in many manufacturers, providing a direct connection between how product quality contributes to customer reorder rates.
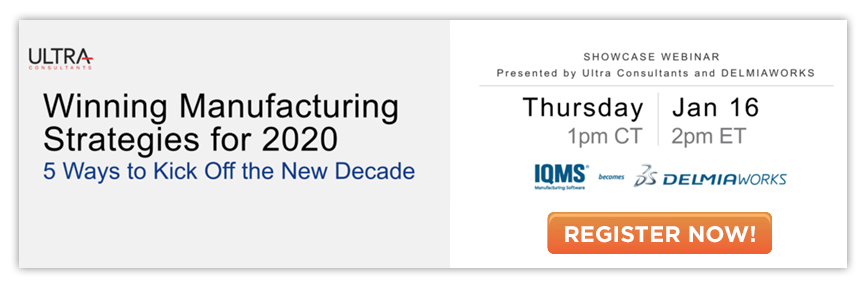